In sanitary applications, appropriate materials can make a difference in safety, efficiency, and compliance. Whether in food manufacturing or the pharmaceutical industry, strict hygienic practices must be observed, and material selection is fundamental to fulfilling these practices. The selection processes often leave crucial questions, such as which materials will satisfy the requirements of the application the most? This guide hopes to highlight the relevance of the right material selections in terms of hygiene, performance, as well as industry requirements. From new system designs to optimizations of existing ones, every professional is bound to find the answers that will aid them in prioritizing compliance and quality. Continue reading to learn the primary considerations that rest behind the significance of material selection in sanitary settings.
What Are the Key Factors in Material Selection for Sanitary Applications?
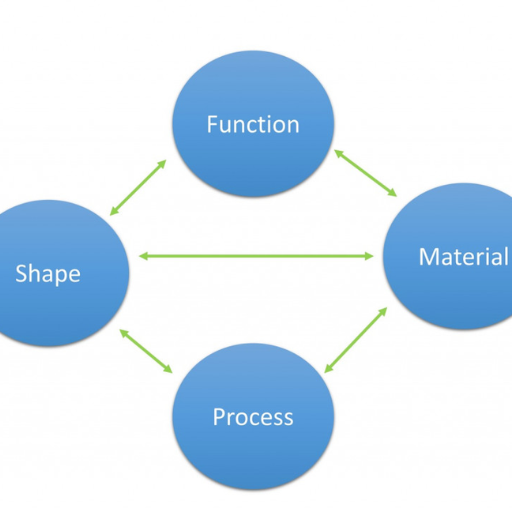
When chosen for sanitary applications, the following primary considerations need to be factored in.
- Corrosion Resistance: Materials must endure exposure to cleaning agents, moisture, and other corrosive substances in order to withstand the test of time while remaining hygienic.
- Cleanability: The material must be able to withstand thorough cleaning to mitigate contamination while meeting sanitation standards.
- Non-Toxicity: Materials must be safe, particularly for food, beverages, or pharmaceuticals, and not capable of leaching dangerous materials.
- Strength and Durability: The selected material needs to withstand operational stresses like temperature and physical wear without losing structural integrity.
- Compliance with Standards: Materials must fulfill applicable legal and industry verification documents ascribed to the sanitary application.
These factors are vital for Safety, performance _and_ compliance in maintaining sanitary conditions.
Importance of Choosing the Right Material for Sanitary Processes
Opting for the right material construction regarding sanitary processes significantly influences safety, efficiency, and productivity. According to the latest reports, there is an increased demand for stainless steel owing to its superior corrosion resistance, risk-free cleanup, and structural soundness when exposed to high pressure and temperature. For instance, Types 304 and 316 stainless steel find usage within the food and pharmaceutical sectors because of harsh sanitization procedures and contamination control prerequisites.
Moreover, modern innovations have made access to cheaper counterparts possible, such as certain high-performance polymers. PTFE (polytetrafluoroethylene) and PEEK (polyether ether ketone) are becoming more popular due to their chemical, high temperature, and non-reactive surface resistance that is needed in sanitary settings.
Increases in material durability also present winning opportunities from an economic perspective. Adopting materials not meeting the required quality standard leads to unanticipated delays and extended periods of downtime due to repairing faulty equipment and presenting dangerous operating conditions. As an example, the global market is expected to significantly increase from billions in 2023 to over $7.2 billion by 2030 due to the growing need for compliance with stringent sanitary requirements.
Industries not only reduce risks and improve long-term efficiency by investing in the appropriate materials, but also make certain that safety protocols are met.
Corrosion Resistance and Durability in Sanitary Systems
In sanitary systems used in food processing, pharmaceuticals, and water treatment, two of the most important properties are resistance to corrosion and durability. The presence of moisture, chemical exposure, and frequent fluctuations in temperature can wreak havoc on metals. Due to these reasons, materials like stainless steel, particularly 304 and 316 grades, are marvels because of their high corrosion resistance. For example, molybdenum-containing stainless steel 316 is further fortified against chloride corrosion, which makes it perfect for demanding sanitary applications.
Reports from the industry indicate that the global market for stainless steel is poised for growth at an approximate CAGR of 5.5% from the year 2023 to 2030, primarily attributed to the rising need for sanitary piping and equipment. Not only this, but also improvements in surface passivation and electropolishing have made these materials stronger and increased their longevity by reducing surface roughness that may contain contaminants or initiate corrosion.
Adopting materials that resist corrosion helps meet hygiene and safety regulations while simultaneously protecting equipment over time, minimizing maintenance, repair, and downtime expenses. The value of constructing with sturdy, durable materials is most evident in clearly defined sanitized spaces that are kept clean using strong disinfecting chemicals.
Compliance with 3-A Sanitary Standards
Following the 3-A Sanitary Standards helps maintain cleanliness, safety, and the quality of the products. With compliance to these standards, I ensure that the relevant equipment and processes maintain critical hygienic boundaries, mitigate contamination hazards, and promote dependable and efficient performance in demanding conditions.
How Do Different Materials Affect Sanitary Pipe and Valve Performance?
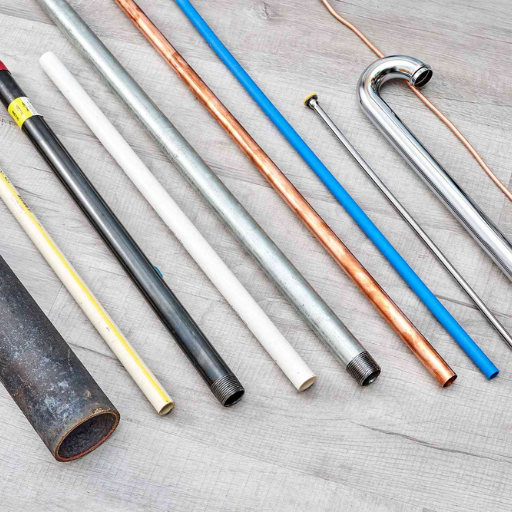
As noted above, different materials affect the performance of sanitary pipes and valves in terms of durability, hygiene, and compatibility with different substances. For instance, stainless steel, especially 304 and 316 grades, is often preferred because of its high corrosion resistance, strength, and ease of cleaning, which is very important in food and pharmaceutical industries. On the other hand, plastic materials like PVC or polypropylene are lightweight and resistant to some chemicals, but do not have the durability and temperature tolerance that metal does. Choosing the right material provides durability, decreases contamination risk, and aids in compliance with sanitary standards.
Stainless Steel vs. Other Materials: What to Choose?
Stainless steel has unmatched benefits, such as having a longer lifespan than other types of materials since it withstands moisture and high temperatures, along with requiring little maintenance and repairs. When you contrast steel with other materials, other types of mounting brackets, such as PVC or polypropylene, degrade above 140°F. They usually can’t withstand surpassing 1700°F. This makes steel the ideal selection for industrial objectives that require extreme temperatures.
Unlike steel, polypropylene plastic is advantageous in fields where weight savings and flame resistance are crucial. These plastics can slice up to 80 percent of the weight and effortlessly save shipment costs, yet need replaceable rests since the softer nature can cause scratches and contamination.
Steel requires more expenditure at first, however, the long service time makes it a worthy investment. Compared to plastic, which needs to be maintained every 5–10 years, steel’s service life stretches over 20 years.
As always, the decision between stainless steel and other options will depend on the requirements of the particular application, including the environment, operating conditions, and regulatory requirements.
Impact of Material on Food Safety and Contamination Risks
Choosing the right material for equipment in food processing has to be done with utmost care, as it can greatly affect the safety of the food and possible contamination. Massachusetts Institute of Technology, or MIT, has done a study where it is recommending that the most suitable materials for food preparation and processing applications are stainless steel because of its smooth and lasting nature. Stainless steel offers a non-porous surface that is very smooth as compared to certain plastics and wood, which have a tendency to absorb moisture and food particles. In addition, unlike other weak materials, stainless steel is tough enough to resist corrosion, passive Kupfer, and infestation of contaminants, allergens, and pathogenic entities, which can be hazardous for one’s health, making it ideal for kitchens where hygiene standards have to be maintained.
Moreover, for proper deep cleaning and disinfection, stainless steel can endure high temperatures, aggressive cleaning agents, and other conditions. It has been proven that the use of stainless steel will reduce the chances of cross-contamination, unlike other weak materials that are prone to cracks or bacterial growth. As an example, some grades of pliable plastics will tend to soak up food debris or liquids, leading to the risk of growing harmful bacteria and contaminating the environment.
Stainless steel, unlike some plastics under specific circumstances, does not allow chemicals to seep out, ensuring compliance with worldwide food safety standards. Chemical leaching presents serious risks to health and can compromise the quality of food. Considering these factors, stainless steel provides durability while mitigating risks of contamination in food production environments, making it the preferred material in the food industry.
Types of Sanitary Seals: Which Material is Best?
Consideration of the kind of material to use for the production of seals is paramount as it affects the performance as well as the life span of the sanitary seals. It also determines how well the seal performs under extreme conditions and according the industry standards. Each type of material has unique characteristics suited for specific purposes in the food, beverage, pharmaceutical, and chemical industries.
- EPDM (Ethylene Propylene Diene Monomer)
The wide use of EPDM Seals is attributed to the excellent resistance to extreme temperatures, steam, and water. These seals excel in both hot and cold environments. They can withstand temperatures ranging from -70°F to 300°F (-57°C to 149°C). Furthermore, EPDM is known to age without much change, it resists most chemicals. This makes them an ideal choice for applications involving cleaning agents and acids.
- Silicone
Silicone gaskets are used in a variety of appliances because of their flexibility and excellent high-temperature resistance, with the ability to tolerate temperatures up to 450°F (232°C). These gaskets are used in places requiring extreme temperature sterilization, like autoclaves. One drawback of silicone is that it is not very resistant to abrasive chemicals, making its range of application limited.
- PTFE (Polytetrafluoroethylene)
PTFE is a great contender in sealing applications where there are aggressive chemicals and or high temperatures involved due to its chemical-resistant features and nonstick attributes. It can also handle temperatures as high as 500°F (260°C). It is excellent in friction and is unreactive, making it efficient with sanitization systems. On the downside, under constant stress, PTFE deformable and less flexible.
- Viton® (Fluoroelastomer)
Seals made of Viton® are best known for their amazing chemical resistance against oils, fuels, and even a great deal of solvents. Considered best in functionality with incredibly harsh chemicals within a range of -15°F to 400°F (-26°C to 204°C), it is often employed where prolonged exposure to harsh chemicals is present. Viton® has great resistance to wear and compression, increasing its lifespan in difficult conditions.
- Nitrile (NBR)
Application-wise, Nitrile seals are perfect due to their resistance against oil and fuel, performing well from -40°F to 250°F (-40°C to 121°C). Though consisting of a cost-effective option with strong abrasion resistance, nitrile seals lack functionality in extreme temperatures and harsh chemicals.
Key Considerations for Selecting Sealing Materials
When choosing a sanitary seal material, one must consider factors like temperature limits, flexibility, and chemical composition balance, along with any applicable regulations. The material also has to pass an FDA inspection or other relevant authority’s regulations on safety and hygiene. Proper selection mitigates contamination risks by enhancing system performance, reducing operational costs, and prolonging seal life in industrial processes.
What Are the Best Practices for Installation and Maintenance of Sanitary Equipment?
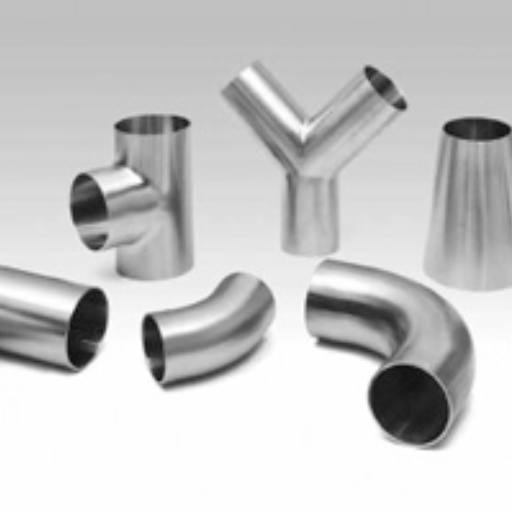
- Follow Manufacturer Guidelines: Use and take care of the equipment, as the manufacturer has provided instructions in great detail, which, if followed, can make the equipment last longer.
- Regular Cleaning and Sanitization: Hygiene as well as Contamination prevention,n is an important aspect, therefore, cleanliness protocols with approved cleaning agents should be maintained.
- Inspect Components Frequently: Inspect critical parts such as seals and gaskets for wear and tear, damage, or corrosion at regular intervals.
- Ensure Proper Assembly: Lack of leaks or operational issues should be verified, in order to check if all components have been correctly aligned and properly fastened.
- Train Personnel: Staff for basic maintenance tasks should be trained in recognizing and as well as correcting underlying issues before they escalate.
- Replace Worn Parts Promptly: In the event of a safety or performance issue emerging, avoid falling components as failures and worn-out parts should be replaced without delay.
- Maintain Documentation: Abide by safety and health protocols while documenting maintenance and repair logs to ensure that compliance is met.
Equipment must be well-maintained to function properly, be safe for use, and meet compliance. Following these practices, sanitary equipment can.
Understanding Sanitary Fittings and Their Material Requirements
Sanitary fittings are critical in food processing industries, pharmaceuticals, and biotechnology due to their need for hygiene. The materials that are used for these fittings are basic, clean, durable, and non-corrosive. Arguably, stainless steel is the most common fitting material, especially grade 304 and 316, since it’s smooth, easy to clean, and doesn’t corrode.
Stainless Steel 316 is, for instance, ideal due to its molybdenum content since it increases the resistance of the material to chlorides and other harsh cleaning agents. This material can be used in heavily sanitized locations. Furthermore, gaskets and seals out of food-grade polymers like PTFE (Teflon) and EPDM are also popular because of their good chemical resistance and flexibility at a wide range of temperatures.
Approval from the FDA and the European Hygienic Engineering & Design Group (EHEDG) is not the only issue; internationally accepted documents for sanitary fittings also need to outline the materials used. They ensure the equipment has minimal to no leakage of harmful substances, low porosity to bacterial growth, and can endure multiple sterilization rounds. For instance, surface roughness average (Ra) must be capped at 0.8 micrometers to limit microbial adherence.
As industries focus on sustainability, modern sanitary fittings are now designed to be more energy efficient, as well as to reduce the amount of water used during cleaning processes. Compliance with the requirements pertaining to materials, along with these advancements, helps to ensure that sanitary fittings achieve both performance and regulatory requirements effortlessly.
Maintaining Cleanliness and Preventing Contamination
For the purpose of ensuring product safety and regulatory compliance, the avoidance of contamination and the proper maintenance of sanitization systems are very crucial operations. These initiatives start with the installation of CIP, or cleaning in place, systems, which faculty automated cleaning features, thus allowing unhindered cleaning of complex machinery. Removing microbial and other forms of biological residue, such as debris, from the equipment using high-temperature H2O, detergents, and mechanical action.
Moreover, sensor technology developments allow for the monitoring of the effectiveness of cleaning procedures in real-time. As an instance, cleaning fluid residue can be gauged using turbidity sensors therefore enabling cleaning while minimizing water and detergent consumption. Furthermore, modern studies claim that modern CIP systems can now reduce water usage by almost ten percent, with some claiming it can go up to thirty percent compared to older systems.
However, hygienic equipment design, such as stainless steel 304 and grade 316L, is commonly used due to their pitting resistance and susceptibility to CIP, and improves operational efficiency while ensuring hygiene standards are met. In addition, hygienic equipment design smooth surfaces with minimal dead ends helps to further reduce the accumulation of microbes and debris.
Regular Checks for Corrosion in Sanitary Pipes
Periodic inspection of sanitary piping systems is vital for injury and health hygiene sanitation, as degradation may damage the equipment, exposing it to contamination hazards. Neglect strengthens the possibility of attack from moisture, cleaning agents, temperature, and pH alterations.
Corrosion can be detected by modern methods: Ultrasonic testing, eddy current inspection, and visual examination. Ultrasonic testing, for instance, is able to gauge the thickness of the pipe walls and walls thinned through corrosion. Lesser pipe rupture is said to occur with regular ultrasonic inspection at a 30% reduction, according to some research.
Observing water quality and cleaning methods goes a long way in preventing terrain automedicable. Maintenance of sanitary systems to prevent breakdown that would jeopardize the entire system ensures the business is profitable and adheres to the municipal health codes.
What Are the Regulatory Standards Governing Material Selection in Sanitary
Applications?
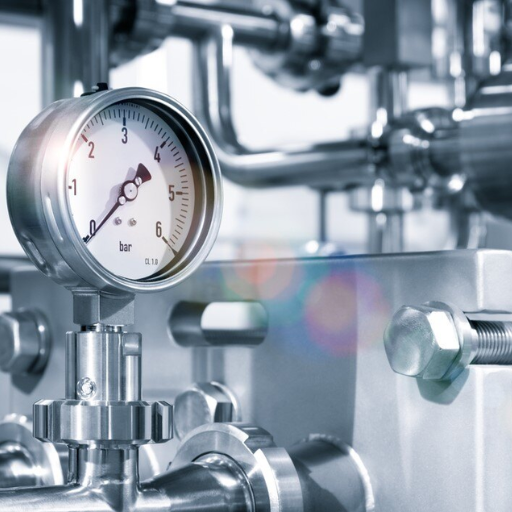
The criteria for selecting materials in sanitary applications focus on public safety, hygiene, and optimum performance. Some of the criteria include:
- FDA (Food and Drug Administration): concerns that materials should meet the requirements stated in the Code of Federal Regulations (CFR) of 21, particularly CFR 21, which covers materials intended for food contact and sanitary services. It contains specific rules under Section 70, which enumerates ‘Exemptions to Premarket Approval Processes’.
- 3-A Sanitary Standards: They provide the design and construction features of the equipment and systems for the dairy, food, and beverage industries, ensuring cleaning and prevention of contamination.
- ASTM International: The standards of ASTM provide specifications for the properties of the materials, particularly corrosion and sanitation durability, including the environments where they are intended to be used, in this case, sanitary conditions.
- EHEDG (European Hygienic Engineering & Design Group): For worldwide uses, its standards serve as the basis for the hygiene and design builds of hygienic materials and equipment.
Following these standards ensures that materials used in sterile applications are safe, clean, and durable enough.
Industry Standards for Food Equipment and Processing
Like other industries, the food processing industry enforces specific principles considering the quality and safety of food products. 3-A Sanitary Standards, FDA, and EHEDG provide pertinent instructions dealing with food hygiene and equipment design, and processing.
As an example, 3-A Sanitary Standards considers maintainability and retention of sanitized conditions. They require that the equipment be made of stainless steel and other non-poisonous, corrosion-resistant materials. They also require that equipment is made in accordance with the Current Good Manufacturing Practices (CGMPs), especially in regard to hygiene and contamination mitigation.
Recent data suggests that there is increasing industry adoption of global food safety regulations like ISO 22000 and HACCP. For instance, ISO 22000 certification in the food industry is estimated to have increased by more than 18 percent between 2017 and 2021, which signals enthusiasm towards international standards.
Such standards are essential for fostering and enhancing compliance, consumer confidence, and reducing operational challenges. Meeting these rigorous requirements for the machinery and equipment augments food safety with regard to extension of shelf life, recalls, and health emergencies.
How to Ensure Compliance with Sanitary Regulations
Compliance with sanitary regulations is achieved through combining up-to-date industry practices, regular audits, and employee training. In order to hold business certifications and avoid violations, they need to pay attention to the latest standards like ISO 22000 and local food safety rules. They are further compounded by rampant foodborne illnesses, with 600 million cases being reported annually across the globe, which strengthens the argument for verified sanitary practices.
Companies can also support compliance with stringent cleaning and sanitization of all equipment and surfaces that come into contact with food. Modern technology, like automated and robotic cleaning systems, can dramatically increase the efficiency and consistency of sanitary conditions before and during use. Employee education is equally vital; routine training focused on hygiene and food handling drastically drops the odds of contamination.
Besides all that, maintaining cleaning schedules, inspection reports, and actions taken to clean issues aids in maintaining traceability while proving regulatory measures during an audit. All audits, whether external or internal, can be passed if companies adopt stringent standards towards maintaining hygiene and safeguarding public health.
How to Choose the Right Materials for Specific Sanitary Applications?
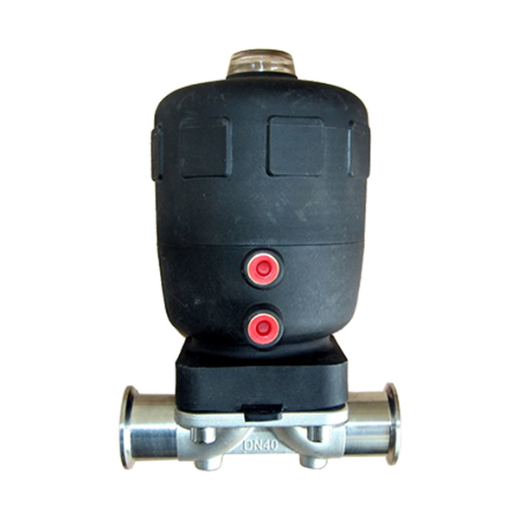
- Understand the Application Requirements
Determine the actual operating conditions, which include temperature, moisture, and exposure to any chemicals. This guarantees that the selected materials will serve their purpose appropriately.
- Prioritize Durability and Safety
Use materials that are easy to clean, non-porous, and corrosion-resistant. Such attributes help to maintain a high level of hygiene and avoid contamination.
- Ensure Regulatory Compliance
Use materials that are FDA compliant or food grade certified. Such choices will ensure that compliance regulations and laws pertaining to safety are met.
- Assess Maintenance Needs
Evaluate how practically simple the materials are to keep clean, ensuring that maintenance overhaul is cost-efficient and effective over an extended period of time.
Factors to Consider for Sanitary Pumps and Valves
- Material Durability and Corrosion Resistance
- Choosing corrosion-resistant materials, such as SS316 stainless steel, for sanitary pumps and valves is critical because they undergo rigorous cleaning with chemicals and different temperatures. Stainless steel 316 is common in the food, beverage, and pharmaceutical industries because it needs stainless steel that does not corrode easily in furnish or corrosive materials.
- Flow Efficiency and Precision
- To conserve energy and ensure product uniformity, high flow capacity is a must. Baltichela and Marjani noted that thorough designs help minimize smooth fluid transitions, which decrease spaces that allow bacteria growth and contamination. According to the research, modern sanitary pumps have optimized flow paths that enable up to 20%enhanced operational efficiency, hence decreasing the cost of operations.
- Compliance with Industry Standards
- To make sure the valves and pumps observe all stringent health and quality requirements, check the 3-A Sanitary Standards, EHEDG, and FDA compliance certifications. For example, 3-A Sanitary Standards compliant systems are built with features that control bacterial growth for better safety in operations across industries.
- Energy Efficiency
- Today’s modern spare parts sanitary pumps now come with VFD-equipped energy-efficient motors, improving overall energy management. Industry report data suggests that the use of VFDs can reduce energy consumption between 30% and 50%. This presents significant savings in the long run while improving cut costs and adhering to sustainability practices.
- Advanced Automation Capabilities
-
Smart pumps connected to IoT networks are capable of self-diagnosing and monitoring essential performance metrics like pressure and temperature, and adjusting them to ideal settings and maintaining self-sustaining optimal conditions. Autonomous control helps to stabilize the system by reducing processes unattended by humans. These innovations further enhance business reliability through reduced downtime, which is critical in industries that have a constant demand for products.
Case Studies: Successful Material Choices in Food Processing
- Stainless Steel in Dairy Production
Stainless steel marks its place as a construction material of concern in the dairy industry due to its concern with corrosion, durability, and hygiene. As an example, Grade 316 stainless steel is frequently used because of its resistance to pitting and crevice corrosion associated with acidic dairy products. Research indicates that equipment made using this material outlives many other metals and tends to have less downtime, which increases productivity. Productivity being one of the most important key performance indicators.
- High-Performance Plastics in Meat Processing
High-performance plastic like UHMWPE (Ultra-High-Molecular-Weight Polyethylene) is utilized widely in cutting boards, conveyor systems, and various other meat processing equipment. This material has excellent Wear resistance, low friction, and non-porous surfaces, which prevent bacteria from growing. A case study done at a large meat packaging facility indicated the inclusion of ineptness and not only lower maintenance costs but also cleaning water usage by 25%.
- Silicone in Baking Operations
Silicone is a prominent material within baking processes, more specifically in ‘baking molds or non-stick coatings’. Silicone’s non-toxic properties, as well as its ability to withstand high temperatures, makes it safe for use with food. Research has reported that silicone molds do not degrade until higher than 500°F, and thus, such molds can be reused frequently. Their reuse has been correlated to a 30% decrease in material costs for a mid-size bakery over the course of a fiscal year.
- Aluminum in Beverage Canning
Aluminium’s resistance to corrosion and lightweight properties make it essential in the canning of beverages. Roughly 75% of aluminium cans are recycled across the world, showing their sustainability advantages. One of the most popular drink producers noted that being able to switch to recycled aluminium results in less production costs by 15% and lowers their overall carbon footprint, which is favorable in today’s consumer market.
Strategic incorporation of the following resources alleviates operational efficiency while observing the heightened food safety regulations. This impacts the consumers and Manufacturers positively.
What Are the Common Challenges in Material Selection for Sanitary Use?
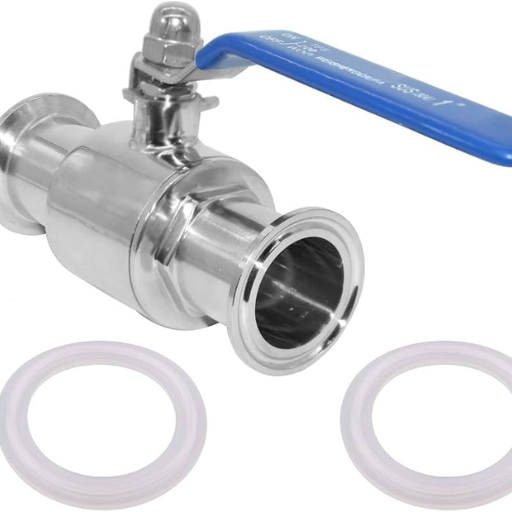
Choosing appropriate materials for sanitary applications poses the following problems:
- Compliance with Regulations – All selected materials must be regulated by pertinent law, such as health safety standards from the FDA or EU, which in turn guarantees safety for food and pharmaceutical contact.
- Resistance to Contamination – There should not be any bacteria or other biological contaminants accruing on the surfaces of the materials, which would impede hygienic contamination practices.
- Durability – They need to withstand cleaning, high temperatures, and harsh chemicals without degrading or corroding.
- Cost – Sanitary materials of good quality, depending on the functional requirement, are costly; thus should be economical.
- Maintenance and Lifespan – Materials used should be easy to clean and maintain, have an extended life span, and enhance operational.
Addressing Corrosion and Contamination Risks
Assuring safety and efficiency while doing materials selection to manage corrosion and contamination risks requires attention to detail. As the corrosive process continues due to moisture, chemicals, or heating/cooling cycles, it will weaken the surface of machinery and equipment, which will inevitably lead to mechanical failure or safety issues. The corrosion-resistant stainless steels 304 and 316 grades are widely used because of their chromium content, which forms protective oxide layers. Molybdenum-added 316 stainless steel is best suited for food processing and pharmaceutical industries since it has a considerably better resistance to chloride-induced corrosion, especially for seawater applications.
Equally important is preventing contamination in food and chemicals, especially in healthcare industries. Irregular surfaces in the shape of gouges or cavities tend to collect a large number of germs or dirt, which is bad for cleanliness. Sanitary polished,d and seamless finish is an additional enhancement that can further reduce these problems. According to some researchers, compared to untreated metals, electropolished stainless steel does significantly better when it comes to controlling biofilm growth, which provides further assurance of cleaner and safer work environments.
Covering these risks requires regular maintenance and inspections, alongside compliance with cleaning protocols. These would further be aided by new coating technologies such as epoxy or polymer coatings, which protect against corrosion and microbial growth, making surfaces more hygienic. Proactive approaches towards corrosion and contamination control are critical for operational success, meeting the required standards, and compliance with governing bodies.
Balancing Cost with Quality: How to Make Informed Choices
Balanced decisions arise from evaluating both cost and quality; leaning too much on one side can jeopardize an optimal outcome. While choosing materials, equipment, or services, businesses have to think of the total cost of ownership (TCO) instead of just the initial cost. High-quality materials, for example, are often framed as being more expensive due to their higher upfront pricing; however, they offer better long-term savings. Studies suggest these durable materials can save businesses upwards of 30% from replacement and repair costs over a five year period.
Quality control is also something that requires consideration. Products and services fulfilling ISO certification requirements provide assurance of consistent dependability and performance. Companies complying with these standards reportedly suffer 20% less production downtime while receiving higher customer satisfaction. Furthermore, advanced technologies that employ predictive analytics for maintenance or automated production systems may increase capital investment but greatly improve productivity, operational efficiency, and overall effectiveness.
In the end, companies can effectively balance cost and quality by performing thorough cost-benefit analyses, benchmarking them with industry leaders, and contracting clear pricing, price-sensitive suppliers with proven histories. Decisions based on measurable indicators and aligned with organizational goals guarantee balanced advancement and a competitive position within challenging markets.
Overcoming Misconceptions About Sanitary Materials
Often neglected, sanitary materials ensure hygiene and health in a number of spheres such as healthcare, food processing, and personal care. High-quality sanitary materials are often considered to be very expensive. This myth is untrue as advancements in manufacturing and material science have greatly improved these products without compromising on quality. Take protective gear as an example, nonwoven surgical masks and protective gowns are lightweight, durable, and increasingly produced using spunbond and meltblown techniques, which offer excellent filtration and are cheaper in comparison to prior production techniques.
Another common misunderstanding surrounds the impact of sanitary materials on the environment. Innovations in material production have led to the creation of biodegradable and recyclable sanitary materials that were previously unsustainable. Eco-friendly sanitary products are expected to capture over 7% CAGR until 2030, which demonstrates worldwide demand for eco-friendly materials.
There is also a belief that sanitary disposable materials are less hygienic than their reusable counterparts. Quite the contrary, single-use products are designed to be as safe as possible when it comes to contamination, especially in non-sterile environments. ISO 13485 certification ensures that products meet stringent safety and hygiene standards, reinforcing the claim.
Clearing these misconceptions with credible information alongside advancements in technology and sustainability aids both consumers and businesses in making informed choices centered around health, efficiency, and ecological responsibility.
Reference Sources
-
Implementation of MS1500: 2009: A Gap Analysis1:
- Key Findings: This study analyzed the implementation of Malaysia’s Halal Food Guidelines (MS1500: 2009). It identified gaps in compliance, particularly in premises layout and the processing of halal food. The study emphasized the importance of stringent implementation to build consumer trust and ensure food safety.
- Methodology: A cross-sectional survey was conducted with managers of halal-certified companies in Malaysia. Importance-performance analysis was used to evaluate compliance levels.
-
Risk Factors Associated with Hygiene and Sanitation Practices in Public Secondary Schools in Kitale Municipality, Kenya2:
- Key Findings: The study highlighted inadequate sanitation facilities, poor water distribution, and insufficient funding as major challenges. It also identified a lack of adherence to cleanliness protocols and recommended increased funding and regular inspections by public health officers.
- Methodology: A descriptive cross-sectional study using stratified random sampling, structured questionnaires, and observational checklists. Data were analyzed using SPSS.
-
Design and Materials Selection: Analysis of Similar Sanitary Pads for Daily Use3:
- Key Findings: This research focused on the materials used in sanitary pads, identifying polypropylene and cellulose as key components. It emphasized the importance of material selection for improving product design and user comfort.
- Methodology: The study used FTIR/ATR spectroscopy and scanning electron microscopy to analyze the chemical composition and morphology of sanitary pad materials.
Frequently Asked Questions (FAQs)
Q: Why is selecting the right material important for sanitary applications?
A: Selecting the right material is crucial because it directly impacts the hygiene and safety of food and beverage processing. The material must maintain the highest standards of cleanliness to ensure that it does not compromise food safety.
Q: What is the most suitable material for your sanitary piping applications?
A: Stainless steel is often the most suitable material for your sanitary piping applications due to its durability, resistance to corrosion, and ability to maintain cleanliness. It is widely used in the food and beverage industry for its compatibility with sanitary design principles.
Q: How do 3-A standards influence material choice in sanitary applications?
A: 3-A standards set the highest standards for sanitary design and materials used in food contact surfaces. Adhering to these standards ensures that the materials chosen effectively maintain sanitary conditions throughout the production process.
Q: What role does the material for your sanitary piping system play in food safety?
A: The material for your sanitary piping system plays a pivotal role in ensuring food safety by preventing contamination. It must be non-reactive and easy to clean to maintain the highest standards of cleanliness during food and beverage production.
Q: What are the key considerations when installing and maintaining sanitary piping systems?
A: Key considerations include selecting the right sanitary materials, ensuring proper installation to avoid leaks, and implementing regular maintenance protocols. This helps to maintain the highest standards of cleanliness and ensures the effective sanitary operation of the system.
Q: How can I ensure that my sanitary applications meet cleanliness standards?
A: To ensure that your sanitary applications meet cleanliness standards, choose suitable materials that comply with 3-A standards, regularly inspect and clean the piping system, and train staff on proper sanitary practices.
Q: What are the benefits of using stainless steel pipes in sanitary applications?
A: Stainless steel pipes offer numerous benefits, including durability, resistance to corrosion, ease of cleaning, and compliance with 3-A sanitary standards, making them ideal for maintaining effective sanitary conditions in food and beverage processing.
Q: How does the choice of material affect the overall efficiency of sanitary systems?
A: The choice of material affects the overall efficiency of sanitary systems by influencing flow rates, ease of cleaning, and longevity of the system. Using suitable materials that meet 3-A standards ensures effective sanitary operation and reduces downtime for maintenance.