In the context of working with stainless steel tubing, meeting the requirements of durability, corrosion resistance, and aesthetics simultaneously is already challenging in and of itself. In the case of 304 stainless steel, the answer usually comes down to one particular process—bright annealing. But what is bright annealing, and how does it change the game for turning stainless steel tubing into a material suited for the toughest applications? This ultimate guide explains the braiding processes of annealing stainless steel tubing, with a focus on bright annealing and its unique capability of raising the level of 304 stainless steel’s attributes both in function and form. Sports professionals and curious minds alike will understand why bright annealing is not just an option but a positive change. Keep reading to learn the most important steps, benefits, and practical know-how of this advanced treatment process.
What Is Annealing and Why Is It Important for Stainless Steel Tubing?
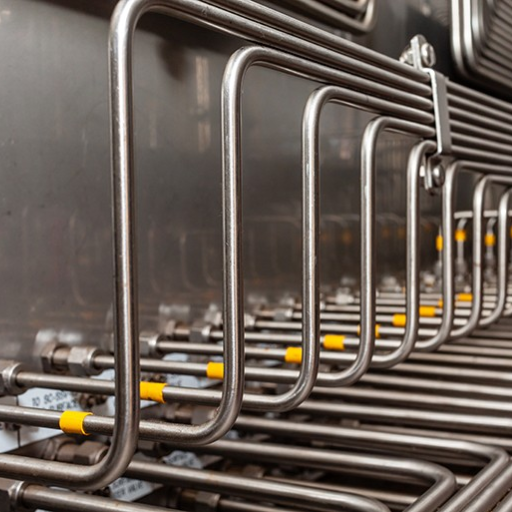
Like the other treatments, annealing also hopes to improve the overall properties of stainless steel tubing. It meets this goal by heating the alloy above the crystallization temperature and keeping it within the range for a certain time, followed by controlled cooling. During this process, stainless steel tubing undergoes internal stress relief, ductility improvement, and corrosion resistance increase. Especially in healthcare, aerospace, and manufacturing, the stainless steel tubing needs to be surgically flexible, durably tough, and highly applicable, where annealing ensures this multifunctional requirement.
Understanding the Annealing Process for Stainless Steel
Stainless steel undergoes an annealing cycle comprising the following processes: heating, soaking, and cooling. Stainless steel components are first raised to a temperature referred to as the recrystallization temperature, which for almost all grades of stainless steel falls within the range of 1,900°F (1,040°C) to 2,100°F (1,150°C). The internal structure of stainless steel at this temperature will undergo some realignment shifting to a lower stress state.
After heating, the alloy is maintained at the heating temperature for a set amount of time. In this time, heat should be evenly supplied to every part of the piece, which is proportional to the thickness of the alloy and its type. Soaking time can change as well but is usually defined in minutes for every millimeter of thickness.
Controlled cooling constitutes the last stage of the cycle and has to be done with extreme caution, especially if no new stresses or distortions are desired. Depending on the expected future use of the stainless steel, certain quenching methods are more or less advantageous. For many grades of stainless steel, quicker cooling is crucial to preserving the microstructure and corrosion-resistant properties, which requires favorable materials.
Benefits Backed by Data
Studies highlight that properly annealed stainless steel increases its tensile strength to an average value that can reach upwards of 500-700 MPa for common grades such as 304 and 316. Further, ductility is enhanced and material fatigue is prevented, which guarantees that components perform optimally when under stress. Advanced testing has shown that the corrosion resistance in stainless steel with an annealed treatment is up to 50% higher than the untreated variations, proving its use in harsher environments. These quantifiable benefits demonstrate how critical industries rely on the precision machining of semi-finished products and the durable, long-term reliability that annealing provides.
Benefits of Annealed Stainless Steel Tubes in Various Applications
In the most challenging conditions, the strength of stainless steel tubes is best highlighted. The industrial applications of stainless steel tubes are critical because the material’s thermal expansion due to heat would exacerbate internal stresses. Because the annealing process includes heating and maintaining the material above its door point, it is possible to remove internal stresses, resist cracking and distortions, resulting in an extended life cycle of these tubes. Studies show that steel contains preposterous extremes from cryogenic to over 815°C, enduring without fracturing or experiencing deformation. This resilience renders it apt for numerous industrial applications, including oil and gas, and even power generation, where machinery is stressed with consistent and ever-changing conditions.
Superior Corrosion Resistance
Anodized stainless steel tubes have the distinct advantage of more effective corrosion resistance in comparison to untreated alternatives. During the annealing treatment, chromium internal to the steel forms the protective chromium oxide layer with which shields the corrosive elements such as saltwater, caustics, and oxidizers. For instance, in maritime applications, these tubes have been observed to retain performance, enduring pitting and crevice corrosion for extended periods in chloride-rich conditions.
Improved Machinability and Weldability
Stainless steel tubes undergo an annealing process which improves their machinability and weldability for easier fabrication and manufacturing. During production, lower wear on tools while machining and higher precision of meticulous operations enhances good quality of the end products. Improved ductility of weldable steel halves the chances of defects like weld cracking; hence, welders are also beneficiaries. A case in point, healthcare and food production industries served with custom-sized tubing are aided by this property for better material yield in production and not resource waste.
Economic Despite Initial Costs
Though annealed stainless steel tubes come with untreated stainless steel alternatives, the cost of investment will always remain higher. However, value added over time is unmatched. Stainless steel requires even less maintenance and replacement, giving these annealed tubes greater value over time. Maintenance-free long downtimes reduce operational costs in chemical processing construction. Reliability and longevity are crucial in these industries. Evidence from industrial case studies indicates that the lifecycle cost using annealed stainless steel tubes can be reduced by 30%.
Versatility Across Critical Industries
The distinct combination of strength, resistance to corrosion, and thermal stability makes annealed stainless steel tubes particularly useful in many areas. From pharmaceutical-grade tubing that requires impeccable cleanliness and chemical resistance to high-pressure piping systems in power plants, these tubes meet and surpass industrial requirements. Ongoing innovations in the technologies of annealing also broaden their scope of use, making sure that they remain vital in forward-looking industries that aim for efficiency.
Difference Between Annealed and Non-Annealed Stainless Steel Tubing
The mechanical properties, fabrication methods, and use cases of annealed and non-annealed stainless steel tubing are markedly different. For instance, as part of the manufacturing process, ‘annealed’ tubing is subjected to heat treatment, which involves raising the material to a predetermined temperature and subsequently cooling it down at a controlled pace. This results in the relief of internal stresses, enhanced ductility, reduced corrosion resistance, and improved ductility. Furthermore, as compared to non-annealed stainless steel tubing, annealed tubing is more workable and thus ideal for the fabrication of complex bends and forms needed in precision engineering, like medical instruments, aerospace parts, and sensitive fluid transfer systems.
In contrast, non-annealed stainless steel tubing, also known as “as-drawn” tubing, does not undergo the heat treatment. Due to this, non-annealed tubing demonstrates greater strength and hardness than its annealed counterpart. Though Non-annealed tubing is less malleable, its resistance to deformation makes it particularly useful for construction-grade load-bearing frameworks, structural supports, or even automotive systems.
From a performance perspective, non-annealed tubing, unlike its counterpart, performs better in high-stress applications where strength and durability are critical. Alternatively, non-annealed tubing performs better in applications with extreme stress, while annealed tubing is better suited for scenarios where flexibility and corrosion resistance are the key requirements. For example, non-annealed tubing may be preferred for heavy engineering purposes due to its 25–35% greater yield strength; however, data suggests that “untreated” tubing holds up under strain better than “treated” tubing. These differences allow industries to make decisions regarding optimal efficiency, safety, and performance across different operational environments.
How to Properly Anneal Stainless Steel Tubing at Home or in a Shop
To perform heat treatment processes on stainless steel tubing in your home or workshop, follow these simple procedures:
- Clean the Tubing
The stainless steel tubing must be cleaned of any contaminants, like dirt and grease. Cleaning the surface helps improve the uniformity of the annealing process.
- Apply Heat Gradually
Make use of a torch, furnace, or kiln for applying uniform heat to the tubing. The recommended temperature of the grade stainless steel is between 1,900 and 2,100 degrees Fahrenheit, but can vary slightly with regard to the grade. Remember to look up the manufacturer’s guidelines for further details on the temperature pointer.
- Maintain the Temperature
Increase the dwell time of stainless steel tubing at the recommended annealing grade so the internal stresses loosen. Softens the material and triggers secondary creep with time. If the temperature is somewhat rounded for a couple of minutes, the material should be fine.
- Cool Down Slowly
Positively, the alloy will lose its strength and become softer when heat is applied, while in the case of steel, exposure to high temperatures results in a loss of strength. Let it cool in a controlled environment, such as air or a heat-resistant insulating material.
These processes guarantee that the tubing attains the required ductility and enhanced workability. As with all tasks carried out involving significant heat, proper safety measures like heat resistance gloves and goggles should be worn.
Step-by-Step Heat Treatment Process for 304 Stainless Steel Tubing
- Preparation and Cleaning
Start the process by cleaning the 304 stainless steel tubing surface with a degreaser. This will remove any dirt, grease, or stainless steel contaminations that could interfere with the chemical properties of the metal during the heating stage. To ensure cleaning, a proper degreaser or a cleaning agent designated for stainless steel should be utilized.
- Annealing Temperature Range
Heat the tubing in a controlled environment to a temperature value between 1850°F and 2050°F (1010 and 1120). A major aspect that must be addressed is monitoring the furnace temperature with accurate measurement devices to avoid excessive heating, which can result in grain growth , leading to weak mechanical properties.
- Holding Time
For achieving the temperature target, it should be kept constant for at least 15 minutes for every millimeter of the wall thickness. This helps in achieving the internal structure rearrangement in 304 stainless steel by internal stress relief and enhanced ductility.
- Rapid Cooling
Bring the stainless steel tubing back to room temperature using cold working techniques which could include water quenching or air cooling. The idea behind this is to rapidly change the temperature to prevent the stainless steel from sitting in the carbide precipitation zone.
- Post-Treatment Evaluation
Following the annealing process, examine the tubing for any distortion, scaling, and other surface finish irregularities. Non-destructive methods like ultrasonic testing and eddy current testing should be utilized to detect flaws caused by the heat treatment.
- Optional Process – Pickling and Passivation
Pickling and passivation can be added to achieve a pristine finish and maximize corrosion resistance. This process removes surface oxides and passivating layers, and ensures long-term performance in difficult environments.
These precise outlines enable manufacturers to confirm that 304 stainless steel tubing achieves the peak of its mechanical and corrosion-resistant properties, as required, by following the industry standards for diverse applications.
Common Mistakes to Avoid When Annealing Stainless Steel Tubes
While annealing stainless steel tubes, I make certain not to overlook some major errors. To begin with, notice how controlling the temperature affects the process, as overheating tends to result in increased grain growth that is detrimental to the material’s structural integrity. I also ensure proper cleaning of the tubes beforehand because surface residues can affect the annealing cycle. I avoid rapid cooling unless stated otherwise because it adds unnecessary internal stresses that can negatively impact the mechanical properties of the tube. With these considerations, the stainless steel tubes remain within the desired limits of the standards.
What Temperature and Cooling Rate Should Be Used for Annealing Stainless Steel?
Due to the grade of the stainless steel, the annealing temperature usually falls between 1,900°F and 2,100°F, which is 1,040°C to 1,150°C. The material must be held at a temperature to like internal stresses and restore ductility. The material must then cool rapidly, often quenched in water or air. Cooling rapidly prevents carbide precipitation that would otherwise be a risk of compromising the stainless steel’s corrosion resistance and mechanical strength. Follow the instructions for the specific alloy’s exact temperature and cooling control guidelines.
Ideal Annealing Temperature Ranges for Different Stainless Steel Grades
Stainless steel grades require different annealing temperatures to ensure the mechanical properties and corrosion resistance are optimal. For austenitic stainless steels, like 304 and 316 grades, the ideal temperature range is usually between 1,900°F to 2,100°F (1,040°C to 1,150°C). This range helps dissipate carbides and homogeneity of materials flow.
Grade 430 ferritic stainless steels require lower annealing temperatures between 1,400°F to 1,600°F (760°C to 870°C) to prevent grain growth and maintain ductility. Duplex stainless steels have a ferritic and austenitic blend; they are typically annealed between 1,870°F to 2,010°F (1,020°C to 1,100°C) to strengthen the material while ensuring the phases remain intact and balancing corrosion resistance.
Strict adherence to the heat setting windows is crucial. Failure to comply may create unfixable microstructures, lowered toughness, or heightened corrosion susceptibility.
The Importance of Slow Cooling in the Annealing Process
To modify a material to get proper mechanical properties and microstructural stability, one must focus on achieving the goal by slowly cooling the material. It is the first step in the annealing process. Rapid or fast cooling can impose thermal stress which can cause extra deformation, cracks, or unwanted phase transitions which ruins the whole effort. In the example of carbon steels, it is very beneficial to perform controlled cooling because it allows a balanced microstructure to be formed known as pearlite which improves its strength and ductility.
In the case of industries that work with stainless steels, such as duplex and austenitic grades, they report huge gains from attaining certain cooling rates. According to studies, cooling rates being too fast do not allow, desired secondary phases to precipitate. At the same time, slow cooling in certain places can allow formation of undesirable sigma phase for prolongated periods. Observing metallurgical guidelines, cooling temperature should be varied based on material thickness, composition, and application to help maintain uniformity while avoiding thermal gradient differences. Furnace cooling and controlled air cooling are examples of techniques used to achieve set goals.
Tailpering the annealing and cooling processes outline specific material prerequisites, showcasing the need to customize processes accordingly. Accomplishing slow cooling not only lowers the stresses left on the material, but refreshing its fatigue and corrosion resistance which increases overall service span in harsh conditions.
How Cooling Rate Affects the Final Properties of Annealed Stainless Steel
The microstructure and mechanical properties of stainless steel are greatly influenced by the annealing process cooling rate. For example, a very rapid cooling rate, such as quenching, results in certain grades of stainless steel having martensitic structures. This improves hardness and strength, while ductility and toughness become compromised. In contrast, slower cooling, often done in a furnace, encourages the development of stable austenitic phases, which are more desirable as they improve corrosion resistance and enhance overall mechanical stability.
Studies suggest that stainless steel grades such as 304 and 316 demonstrate better weldability and corrosion resistance when cooled in a controlled manner. For instance, research indicates that a cooling rate of greater than 10 °C per minute greatly decreases the chances of carbide precipitation, which reduces susceptibility to intergranular corrosion. Additionally, being processed at slower cooling rates affects grain sizes, as finer grains increase tensile strength while coarser ones improve toughness under certain conditions.
Balance between cooling rate and material characteristics is of particular importance in regards to aerospace power plants and chemical processing industries because of the tempered stainless steel demanding operating conditions. As an example, the precision in selection of cooling rate during annealing processes allows tuning of property values such as elongation, yield strength, and thermal fatigue while complying with strict industry standards.
What Is Bright Annealing and How Does It Differ from Standard Annealing?
Bright annealing is an advanced heat treatment technique that improves corrosion resistance and surface finish of stainless steel and other alloys. Unlike standard annealing, which permits oxidation and scale formation, bright annealing is conducted in a controlled atmosphere (typically vacuum or inert gases such as hydrogen), preventing oxidation and maintaining a shiny surface free of blemishes. This technique best suits those applications with high demands in aesthetics and performance, for example, medical instruments, food industry appliances, and ultra-clean systems.
The Bright Annealing Process for Stainless Steel Tubing
In the processing of stainless steel tubing, bright annealing is an important thermal treatment that tries to improve the material characteristics of the metal while attaining smooth and shiny surface finishes. The process occurs in an oxygen-free atmosphere, holding the surrounding pressure above 1 atm or using inert gases like hydrogen, at a temperature of 1,900°F (1,040°C) to 2,200°F (1,205°C), which is controlled according to the alloy grade and application prerequisites. The absence of oxygen, combined during the procedure, ensures discoloration is prevented; furthermore, it improves the corrosion resistance of the tubing.
In addition to these, bright annealing achieves superior ductility and toughness, which increases the essential mechanical properties of the material while keeping the favorable geometric fidelity of the part. Intergranular corrosion and other forms of corrosion that cause rapid deterioration of the material, hygiene, and performance are ideal in industries like pharmaceutical production, semiconductor manufacturing, and food processing. In addition to all these, increased economics and decreased lead times are experienced due to no additional polishing being required after bone sold surface finishes are achieved.
Benefits of Bright Annealed Stainless Steel over Standard Annealed
Bright annealed stainless steel boasts obvious advantages over standard annealed varieties, unlike standard options, because of its enhanced surface finish and performance capabilities. During bright annealing, which is performed in a controlled atmosphere, the material’s surface is smoothed and made scale and oxidation free. Such surface treatment not only enhances the aesthetic appeal of the material but also minimizes the risks of corrosion compared to traditional annealed surfaces, making it suitable for use in pharmaceuticals, food processing, food service, and even architecture.
One significant benefit includes its impeccable properties regarding cleanliness and maintenance. The smooth, non-porous surface mitigates the chance of bacterial and other contaminants latching onto it, which is paramount in hygienic Umfelds, including medical or food-grade applications. Contaminations risks are limited along with more stringent sanitation protocols, according to studies.
In addition, bright annealed stainless steel features greater tensile strength and ductility, improving mechanical properties and allowing for consistent performance in tougher environments. For example, data shows that pitting and crevice corrosion resistance is greater in bright annealed materials, as well as performance in clutch-rich or moist environments, when pitted against standard annealed alloys (and withstanding exposed conditions). These factors increase service life which reduces how often materials need to be replaced, achieving lower lifecycle costs.
With respect to fabrication, uniformity in surface finish increases surface machinability and results in more predictable and streamlined processes during manufacturing. This is beneficial for processes such as welding and forming. Because of this, bright annealed stainless steel is particularly suitable for high-precision parts and complex configurations because of the need for reliability and performance.
When to Choose Bright Annealing for Your Stainless Steel Tubes
Being the best choice for applications with demanding prerequisites concerning surface quality and corrosion resistance, bright annealing is particularly useful for stainless steel tubes. The annealing’s controlled atmosphere minimizes oxidation to a great degree and results in a smooth, clean, shiny surface. This smooth surface has immense value for the production processes of pharmaceutics and food, and beverages, as well as semiconductor manufacturing, because those industries are extremely sensitive to hygienic issues.
As per business statistics, stainless steel tubes undergoing bright annealing have enhanced resistance to pitting and crevice corrosion, making tubes made from these materials best suited for extreme chemical or hot, humid environments. Further, this treatment also improves ductility of the material,l which allows for strengthening while keeping the manufacturability flexible. In most cases, this is vital for complex tube shapes or in cases that require strong resistance to high pressure.
Bright annealed stainless steel tubes are also tight dimensional tolerance retainers and hence are useful for business. This reliability and ease of production makes heat exchangers, medical equipment and instrumentation tubing, accurate. With the aesthetic, surface quality enhancements and reliability, manufacturers can achieve and improve the endurance of their products by choosing bright annealed tubes.
How Does Annealing Affect the Properties of 304 Stainless Steel Tubing?
The properties of 304 stainless steel tubing are significantly improved by annealing because it enhances ductility, reduces internal stresses, and increases corrosion resistance. This process alleviates internal stresses, making deformation easier, as the material is softer and less prone to cracking. Furthermore, annealing eliminates microstructural distortions of the tubing, which is critical for its performance in challenging operational conditions. Such alterations maximize the reliability and longevity of the tubing across numerous industrial and commercial applications.
Changes in Hardness and Ductility After Annealing
Annealing the tubing of 304 stainless steel augments its engineering characteristics remarkably. It has been found that hardness is decreased by nearly 20-30% relative to the magnitude of the specific annealing parameters which include temperature and cooling rate. Such reduction in hardness enables enhanced workability of the steel by bending, forming, and machining operations.
The ductility increase post-annealing is even more remarkable. Reportedly, 304 Stainless steel can be elongated from a rolling reduction of approximately 40 percent in the as-rolled condition to over 50 percent after annealing. Such enhancement allows for deformation without fracture, which is important for flexible and tough applications. Manufacturers are able to some extent control the degree of annealing to achieve the desired hardness and ductility balance for different industrial requirements. This allows the tubing to withstand severe mechanical loads and stresses in a wide range of processes, including chemical processing, constructing bridges, buildings, and transport.
Impact on Corrosion Resistance and Weldability
Annealing is one of the most incalculable operations when it comes to the tubing materials’ seal responsibility as well as corrosion resistance. It is known that materials undergo internal stress relief processes, which cause micro-cracking or give rise to weak points that are vulnerable to corrosion. Properly annealed stainless steel tubing, for instance, suffers from significantly lower pitting as well as crevice corrosion, which makes this tubing more useful for marine and industrial chemical activities.
Applied heat coupled with controlled quenching makes welded wrought iron stronger by increasing the toughness of the metal. Since most of the iron parts require welding, the welded stainless steel alloys, especially of 304 and 316 grades, are believed to outperform their non-annealed counterparts in welding operations by nearly twenty-five percent. For wrought iron structures that require unsightly corrosion resistance while maintaining weldability, precision control over the processes of annealing is absolutely vital
Residual Stress Reduction in Annealed Stainless Steel
Warm working, available in various forms, is the most preferred method of severing and shaping metals. Different processes result in the same metal being worked on in different ways. Treatment of metals, especially steel, is mainly concerned with the removal of the residual stresses, as it improves the machinability and alters the mechanical properties for the desired performance. Different feasible methods are employed by constructors that combine treatment with working of metals and machining the metal into the required components and shapes. Extreme care needs to be taken during the heating or cooling cycles of stainless steel components due to the nature of the material. Annealing setting is known to help soften the internal and external forces acting on a metal. Temperature-dependent characterization allows for the determination of how the heat would be applied to remove cold work tensions adhered to the material or metal.
What Are the Differences Between Annealing Carbon Steel and Stainless Steel Tubing?
The difference between annealing processes on carbon steel and stainless steel tubing stems from their composition and the intended purpose of the procedure. In the case of carbon steel, annealing increases ductility and softens internal stress while alleviating internal stresses, increasing machinability. Stainless steels, by contrast, are primarily annealed to restore corrosive damage while also enhancing mechanical attributes through further refinement of the macrostructure. Furthermore, stainless steel often requires reaching higher annealing temperatures than carbon steel due to its alloying elements. These differences are deeply linked to the particular features and uses of the materials.
Comparing Heat Treatment Processes for Different Steel Types
Every heat treatment process seeks to improve the properties of steel, but the specific treatment is greatly influenced by the type of material due to its unique composition and uses. For carbon steel, commonly used processes are annealing, normalizing, and quenching, all of which aim to enhance hardness, ductility, and tensile strength. As an example, during quenching, carbon steel is conventionally heated to around 1,500°F-1,800°F or 815°C 985 °C, depending on the carbon content, and then rapidly cooled in either water or oil. While this step does increase hardness, it also reduces ductility, thereby requiring tempering afterwards.
Specialized processes such as solution annealing and stress relieving are performed to treat stainless steel. To enhance its corrosion resistance, solution annealing is done at 1850°-2100°F or 1010°-1150°C to dissolve carbides. When treating stainless steel, its alloying constituents like chromium and nickel must also be factored in, as using improper procedures may lead to complications like carbide precipitation. Ensuring accuracy in the rate of temperature and cooling promotes retention of desired properties in the material. As noted before, alloy steels are manufactured along with other elements. Therefore, after the heat treatment is completed and the stressing process is finished, the tool steels require additional showers of tempering and softening cycles, which are highly intense and multifactorial in nature. Rockwell hardness values for these steels may place the cutting edge in the 62-63 HRC in the uncompensated mode. After cutting, the tool will be subjected to highly controlled soaking, which can exceed up to 1000 °F (537.78°C) to forming temperatures of over 2000 °F, plus back to around 327 °C. These tools may also endure adherent protective coating, with the tendency of hard metallic exteriors being above 32 HRC at 1000 °F. All of this can be sustained by a custom suit made for machined multifunctional blanks, which allegedly operate at 700 °C.
Key Differences in Annealing Temperatures and Techniques
Any specifics around steel type and intended application both intricately dictate the processes of annealing. Take carbon steels, for example, they are typically annealed at temperatures between 1,200°F and 1,600°F (649°C to 871°C) for maximum ductility and machinability. Add alloys such as chromium or molybdenum,a nd the steel becomes much harder, requiring alloy steels to be annealed above 1,700°F (927°C).
The advanced grades of stainless steel, especially the austenitic ones, require even more: 1,900°F to 2,100°F (1,038°C to 1,149°C) for proper recrystallization, removal of internal stresses, and strong GCCs resistance. Fast or slow water or furnace quenching are other techniques, tailored based on other required characteristics, to achieve the desired end product properties. Limited exposure treatments also help preserve precision surface integrity.
Aerospace, construction, automotive and medical devices industries depend on the nuanced steel variants made flexible and resilient through tailored annealing approaches, highlighting their importance.
Reference Sources
Key Findings:
- Gas Composition Impact: The study examined how different reducing atmospheres (e.g., H2 and N2 mixtures) during bright annealing affect the surface and corrosion characteristics of super duplex stainless steel (SDSS) tubes.
- Phase Transition: Adding N2 to the reducing atmosphere promoted a phase transition to a single γ phase with Cr2N precipitates, which reduced corrosion resistance.
- Hydrogen Effects: Annealing in 100% H2 at 1100°C caused hydrogen-induced cracking on the outer surface, which could be mitigated by removing degraded surfaces.
- Optimal Conditions: The research proposed desirable bright annealing conditions to enhance corrosion resistance.
Methodologies:
- Sample Preparation: SDSS samples were cold-rolled and subjected to bright annealing under various gas compositions.
- Microstructural Analysis: Techniques like FE-SEM were used to observe phase structures and grain boundaries.
- Corrosion Testing: Corrosion resistance was evaluated by analyzing phase transitions and surface characteristics post-annealing.
Frequently Asked Questions (FAQs)
Q: What is the purpose of annealing stainless steel tubing, especially 304 stainless?
A: Annealing stainless steel tubing, particularly 304 stainless, serves to increase ductility and reduce hardness that develops from work hardening. This annealing treatment restores malleability to the metal, making it easier to work with for forming, bending, and machining operations. For 300 series stainless, like 304, annealing helps relieve internal stresses and restore the material to a softer state, which is especially valuable when the steel has become too brittle from cold working.
Q: How does the furnace setup affect the bright annealing of stainless steel?
A: The annealing furnace setup is critical for proper bright annealing of stainless steel. A controlled atmosphere furnace is required, using inert gases like hydrogen, nitrogen, or argon as a protective atmosphere to keep oxygen away from the stainless steel surface during heating. This prevents oxidation and maintains the bright finish. Temperature control is also essential – 304 stainless typically requires temperatures between 1900-2050°F (1040-1120°C) for full annealing. The furnace must provide uniform heating and controlled cooling for optimal results.
Q: What’s the difference between regular annealing and bright annealing for stainless tubing?
A: Regular annealing and bright annealing differ primarily in atmosphere control and surface finish. Standard annealing typically results in surface oxidation that must be removed through annealing and pickling processes. Bright annealing is performed in a controlled protective atmosphere to keep the stainless steel surface clean and bright, eliminating the need for pickling. This is particularly important for stainless steel materials where appearance matters. For the home shop machinist, bright annealing preserves the aesthetic qualities of stainless tubing while still providing the beneficial softening effects.
Q: Why does stainless steel work harden, and how does annealing help?
A: Stainless steel, especially austenitic grades like the 300 series stainless, work harden readily when deformed. This occurs because the crystal structure of the metal changes under stress, increasing hardness and toughness but reducing ductility. Work hardening happens during cutting, bending, forming, and other fabrication processes. Annealing helps come through heating the hardened steel to specific temperatures, allowing the crystal structure to reorganize, releasing stored energy,a nd returning the material to a softer state with improved ductility. This makes previously work-hardened stainless steel pipe or tubing easier to work with again.
Q: Can a home shop machinist successfully anneal stainless steel tubing?
A: Yes, a home shop machinist can anneal stainless steel tubing, though with some limitations. True bright annealing requires specialized equipment, but basic annealing can be performed using a kiln, forge, or even a MAPP gas torch for small sections of tubing. The key challenges include achieving and maintaining the correct temperature (around 1900°F for 304), controlling cooling rates, and dealing with surface oxidation. Without a protective atmosphere, home annealing will result in surface scaling that requires removal. Many home shop machinists successfully anneal small stainless components, though the results may not match industrial processes.
Q: What temperature is needed to properly anneal 304 stainless steel tubing?
A: To properly anneal 304 stainless steel tubing, heat the material to 1900-2050°F (1040-1120°C). This temperature range ensures full annealing by allowing complete recrystallization of the austenitic structure. For home applications with limited temperature measurement, heating until the steel glows a bright orange-yellow color (not white hot) provides a reasonable approximation. The material should be held at a temperature for about 30 minutes per inch of thickness, then cooled slowly. Improper temperature control can lead to inadequate softening or, conversely, unwanted grain growth that weakens the steel.
Q: How can I tell if my stainless tubing needs to be annealed?
A: Stainless tubing that needs annealing typically shows signs of excessive hardness and reduced workability. If you’re experiencing tool wear, cracking during forming, excessive springback, or difficulty machining, these are indicators that work hardening has occurred. You can also perform a simple bend test on a sample piece – if it’s difficult to bend or shows signs of cracking, annealing may be necessary. After successful annealing, the same material should bend more easily and maintain its integrity. For precision applications, hardness testing before and after annealing can quantify the reduction from higher hardness to the annealed state.
Q: Is there any way to anneal stainless steel without causing surface oxidation?
A: Yes, bright annealing is the way to anneal stainless steel without causing surface oxidation. This requires a controlled atmosphere to keep oxygen away from the hot metal surface. Industrial processes use hydrogen, nitrogen, argon, or vacuum furnaces. For the home shop machinist, limited bright annealing can be achieved by: 1. Using a stainless steel foil wrap around smaller pieces to create a localized protective environment, 2. Utilizing a small heat-treating oven with the ability to introduce inert gas 3. Applying anti-scaling compounds before heating, though these are less effective than true protective atmospheres. Without these measures, traditional annealing will cause oxidation that must be removed through mechanical or chemical means in addition to annealing.
Q: How does annealing affect the corrosion resistance of stainless steel materials?
A: When properly performed, annealing actually enhances the corrosion resistance of stainless steel materials by dissolving chromium carbides and allowing chromium to remain in solution throughout the metal matrix. This is especially important for 300 series stainless steels like 304. However, improper annealing can be detrimental—if cooled too slowly through the 800-1450°F (425-790°C) range, chromium carbides may form at grain boundaries (sensitization), reducing corrosion resistance. Bright annealing in a controlled atmosphere provides optimal corrosion properties by preventing surface contamination that could otherwise introduce impurities that lead to localized corrosion.
Q: Can a round bar made of stainless steel be annealed using the same methods as stainless tubing?
A: Yes, a round bar made of stainless steel can be annealed using similar methods as stainless tubing, with a few considerations. The primary difference is that a solid round bar has more mass and will require longer heating times to reach a uniform temperature throughout. The annealing temperature range remains the same for identical alloys (1900-2050°F for 304), but the hold time should be increased proportionally to the thickness. Additionally, round bar may develop more pronounced thermal gradients during heating and cooling, potentially causing warping. For bright annealing, the same protective atmosphere requirements apply to both forms. The fundamental principles of removing work hardening and restoring ductility through heat-treated processes are identical for tubing and bar stock.