Understanding the distinctions between AISI (American Iron and Steel Institute) and ASTM (American Society for Testing and Materials) standards is crucial for anyone working with steel grades in engineering, construction, or manufacturing. These two organizations serve pivotal roles in defining guidelines for steel production, yet their approaches and scopes vary significantly. This blog post aims to demystify the relationship between AISI and ASTM, exploring how their standards intersect, diverge, and influence material selection and quality assurance processes. Whether you are an industry professional striving for compliance or a newcomer eager to grasp the fundamentals, this guide will provide the clarity you need to make informed decisions in applications requiring steel. Stay tuned as we break down these critical standards and their real-world implications.
What Is the Difference Between Aisi and Astm?
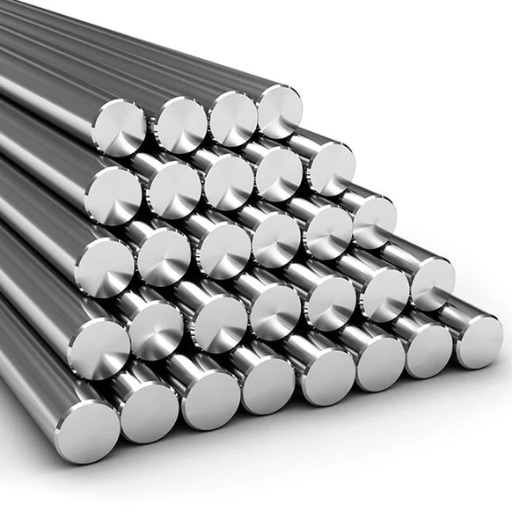
The key difference between AISI and ASTM is that AISI focuses on detailing steel compositions and classifications, while ASTM primarily provides standards for testing methods, material performance, and specifications.
Parameter |
AISI |
ASTM |
---|---|---|
Objective |
Classification |
Testing |
Focus |
Steel grades |
Material standards |
Scope |
Steel-specific |
Broad materials |
Methodology |
Composition |
Testing methods |
Application |
Steel identification |
Quality assurance |
Organization |
Industry association |
Standards organization |
Standard Type |
Composition-based |
Performance-based |
Overview of AISI and ASTM Standards
Detailed Comparison of AISI and ASTM Standards
AISI (American Iron and Steel Institute) and ASTM (American Society for Testing and Materials) are two major organizations that set standards widely recognized in the steel and broader materials industry. While both provide essential frameworks for material performance and classification, their focus and applications differ.
The AISI primarily focuses on classifying steel grades based on their chemical composition. It is widely utilized in the steel industry for identification and product standardization. Manufacturers rely on AISI designations to specify alloying elements and structural properties of various steel grades, creating a foundation for material selection during production.
ASTM, on the other hand, develops performance-oriented standards that encompass a wide range of materials beyond steel. This organization’s testing protocols and quality assurance measures ensure that materials meet stringent performance and safety requirements across industries. ASTM classifications are particularly vital in regulatory compliance, product testing, and certification processes.
Together, AISI and ASTM complement each other by addressing different but interconnected aspects of materials engineering. AISI emphasizes the categorization of steel by its chemical makeup, while ASTM ensures that materials meet specified performance benchmarks under real-world conditions. Both standards are instrumental for engineers, manufacturers, and quality control specialists in designing reliable and durable products.
Historical Background of AISI and ASTM
The American Iron and Steel Institute (AISI), established in 1908, was formed to unify and advance the iron and steel industry in the United States. Initially, its focus was on providing technical expertise, promoting steel usage, and standardizing the classification of steel grades. Over time, AISI evolved into a prominent organization that develops active guidelines for steel applications and maintains a public database of alloy compositions.
The American Society for Testing and Materials (ASTM), now known as ASTM International, dates back to 1898. It was founded to address failures in technical standards for railroads, creating systematic testing methods for steel materials. Over the decades, ASTM expanded its scope to include standards across a wide range of industries, covering everything from construction materials to environmental products. The organization pioneered the standardization of testing procedures, ensuring safety and consistency for materials used in engineering and production worldwide.
Together, AISI and ASTM emerged during the industrial growth of the late 19th and early 20th centuries, addressing the growing need for standardized materials and practices. Their collaborative evolution reflects their shared goal of improving material performance, safety, and global compatibility.
Key Classification Differences
AISI focuses primarily on steel and alloy grading systems specific to composition, while ASTM provides comprehensive testing and performance standards for a wide range of materials.
Parameter |
AISI Focus |
ASTM Focus |
---|---|---|
Material Type |
Steel/Alloy |
All materials |
Scope |
Composition |
Performance |
Standards Code |
Numeric |
Alphanumeric |
Primary Use |
Grading |
Testing |
Global Reach |
Limited |
Extensive |
Process |
Specification |
Testing/Specs |
Industry Focus |
Engineering |
Multisector |
How Do AISI and ASTM Impact Material Selection?
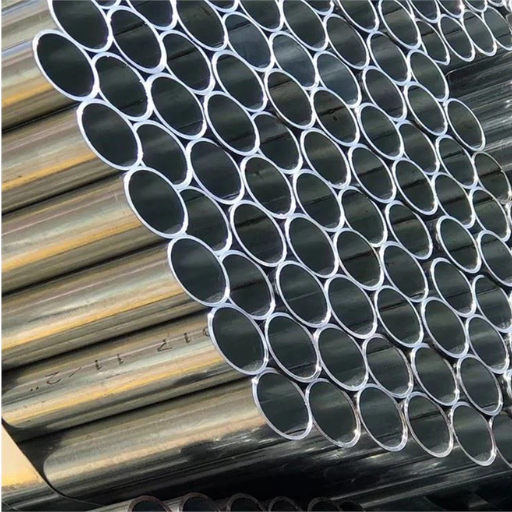
AISI and ASTM significantly influence material selection by providing standardized guidelines that ensure consistency, reliability, and suitability of materials for various applications. AISI focuses on the classification and grading of steel and alloys based on their composition, which is critical for engineers when selecting materials with precise chemical properties. On the other hand, ASTM provides a broader framework that includes performance-based testing protocols and specifications for a wide range of materials, ensuring they meet the functional requirements of diverse industries. Together, these standards help streamline the material selection process, enhance safety, and support global industry compliance.
Influence on Steel Grades
The influence of material standards, such as those provided by ASTM and ISO, on steel grades is substantial, as they define the classification, mechanical properties, and chemical composition of steel. For instance, ASTM A36 specifies carbon structural steel with a minimum yield strength of 250 MPa and a tensile strength range of 400-550 MPa, ensuring its suitability for structural applications. Similarly, ISO 630-2 covers structural steels with defined mechanical properties and specific carbon content limits to achieve desired performance. These standards govern critical parameters such as tensile strength, impact resistance, ductility, and fatigue properties, ensuring materials meet the operational demands of various industries. By providing clear technical benchmarks, these standards guide the production of steel grades tailored for use in construction, automotive, and mechanical engineering applications, balancing durability and cost-efficiency.
Role in the Steel Industry
- Quality Assurance: Standards ensure that steel products meet predefined quality requirements, minimizing defects and ensuring reliability in critical applications.
- Design Optimization: By specifying performance parameters, standards enable engineers to select appropriate grades of steel for specific applications, optimizing both design and functionality.
- Safety Compliance: Adherence to standards guarantees that steel components meet safety regulations, reducing the risk of structural failures and ensuring public safety.
- Global Trade Facilitation: Unified standards promote compatibility across markets, allowing manufacturers and suppliers to engage in international trade without the need for extensive modifications.
- Innovation Catalyst: Standards provide a framework that manufacturers can innovate within, encouraging the development of advanced steel grades and production techniques to meet evolving industry requirements.
Considerations for Material Selection
1.Mechanical Properties: Evaluating the capability of the material with regard to tensile strength, hardness, ductility, and impact resistance and ensure these parameters die at the operational levels.
2.Corrosion Resistance: Any material must be evaluated against its capability to withstand rust and other types of chemical degradation in relation to its use, especially where corrosive elements exist.
3.Temperature Tolerance: The most extreme ranges of both hot and cold conditions should be maintained, setting limits to avoid gross shrinkage in thermal expansion/contraction.
4.Manufacturability: These processes, including easy welding, machining, and forming/shape alteration affect the cost and efficiency of production processes; hence all need to be considered at the design phase for selection.
5.Cost-Efficiency: The focal point should remain on the expenditures attributed to the material in the beginning and contrast it with the expected durability and maintenance level achieved over the life span of the object.
Exploring the Standards of ASTM

ASTM International, formerly known as the American Society for Testing and Materials, establishes technical standards to guide material specifications, testing methods, and performance requirements across various industries. These standards provide an authoritative framework for ensuring quality, consistency, and safety in materials and processes. For example:
- Material Specifications: ASTM standards define the properties and acceptable tolerances for materials, ensuring suitability for specific applications. This helps engineers and manufacturers select materials that fulfill structural, thermal, and durability requirements.
- Testing Methods: Standardized procedures ensure uniform evaluation of material properties such as tensile strength, impact resistance, and thermal behavior, supporting reliable comparisons and compliance with design needs.
- Performance Requirements: ASTM guidelines specify performance thresholds for diverse applications, ensuring that materials can withstand operational stresses or environmental conditions effectively.
These standards streamline engineering processes, fostering innovation while maintaining quality control and regulatory compliance.
Development of ASTM Standards
The development of ASTM standards is a collaborative and systematic process that ensures precision and reliability. First, technical committees composed of subject matter experts, including engineers, scientists, and industry leaders, identify the need for a new or revised standard. These committees draft, discuss, and refine the proposed standard based on extensive research, testing data, and industry feedback. The drafts then undergo rigorous balloting among committee members and stakeholders, allowing for thorough review and consensus. Once approved, the standard is published, providing a comprehensive framework to guide manufacturing, testing, and quality assurance across industries. This iterative process ensures that ASTM standards remain relevant, accurate, and applicable to evolving technological and regulatory requirements.
Understanding ASTM Steel Specifications
ASTM steel specifications are categorized to standardize materials for specific applications, ensuring consistency, reliability, and performance in engineering and manufacturing processes. Each specification typically includes key technical parameters such as chemical composition, mechanical properties, and testing requirements. For example:
1. Chemical Composition:
-
- Specifies the allowable percentages of alloying elements (e.g., carbon, manganese, chromium, and nickel) to achieve desired material properties.
- Example for ASTM A36 steel:
- Carbon (C): ≤ 0.26%
- Manganese (Mn): 0.60-0.90%
- Phosphorus (P): ≤ 0.04%
- Sulfur (S): ≤ 0.05%
- Mechanical Properties:
- Defines the material’s performance under stress, including tensile strength, yield strength, and elongation.
- Example for ASTM A36 steel:
- Tensile Strength: 400-550 MPa (58-80 ksi)
- Yield Strength: ≥ 250 MPa (36 ksi)
- Elongation (in 8 inches): 20% (min)
- Testing Requirements:
- Standards often require specific quality control tests to verify compliance, such as:
- Tensile Tests
- Charpy Impact Tests (for certain grades)
- Hardness Tests
- Standards often require specific quality control tests to verify compliance, such as:
- Dimensional Tolerances:
- Ensures uniformity in product dimensions as per application needs, often referenced through related ASTM standards.
- Applications:
- ASTM specifications are tailored for diverse sectors, such as construction (e.g., structural beams and plates), automotive, and pressure vessels, ensuring optimal performance in demanding environments.
Compliance with these specifications guarantees material durability, compatibility, and safety, making ASTM steel a critical component in engineering standards worldwide.
The Role of ASTM International
- Development of Standards: ASTM International plays a crucial role in developing and publishing voluntary consensus standards for materials, products, systems, and services, ensuring consistency and reliability across industries.
- Facilitating Global Trade: By offering widely recognized and accepted standards, ASTM supports global trade by reducing technical barriers and aligning international practices.
- Advancing Innovation: ASTM serves as a platform for collaboration, enabling researchers, manufacturers, and engineers to contribute to and access the latest advancements in technology and materials.
- Ensuring Safety and Quality: ASTM standards directly contribute to product safety, performance, and quality assurance, protecting consumers and industries alike.
- Providing Technical Expertise: Through its committees and networks of professionals, ASTM offers authoritative insights and serves as a trusted resource for addressing technical questions and challenges in various fields.
How Are AISI and ASTM Standards Developed?
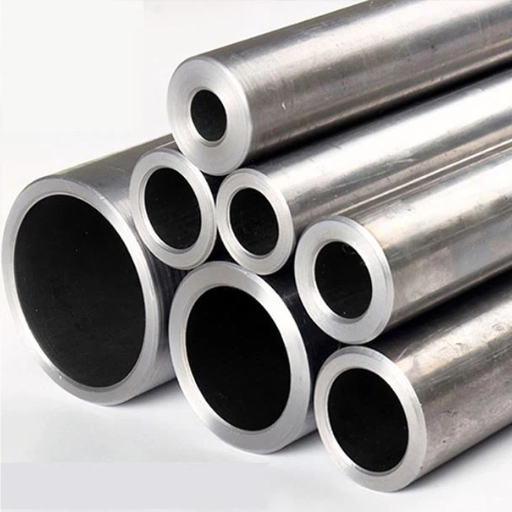
The development of AISI and ASTM standards is a systematic and collaborative process involving experts from industry, academia, and government. For ASTM, the process begins with committees of technical professionals who draft and review standards, ensuring they align with current industry needs and technological advancements. These standards undergo rigorous consensus-based processes, including public reviews and voting, prior to publication. Similarly, AISI standards are developed by incorporating research data and feedback from steel industry stakeholders, focusing on material properties and performance requirements. Both organizations emphasize precision, transparency, and adaptability in creating standards that ensure global applicability and relevance.
Involvement of the American Iron and Steel Institute
Role and Contributions of the American Iron and Steel Institute
The American Iron and Steel Institute (AISI) plays a critical role in advancing the steel industry through advocacy, standardization, and technological innovation. AISI provides technical expertise in the development of steel-related standards, ensuring the materials and processes meet structural integrity and performance benchmarks. The organization collaborates with industry stakeholders, regulatory bodies, and academic institutions to facilitate research, encourage sustainable practices, and enhance product durability. Additionally, AISI actively supports public policy initiatives that promote the competitiveness of North American steel producers while advocating for robust infrastructure investment and the elimination of unfair trade practices. Through these efforts, AISI remains a leading authority in shaping the future of the steel industry on a global scale.
Contributions from the Society for Testing and Materials
The Society for Testing and Materials (now ASTM International) has been instrumental in developing and standardizing technical parameters that underpin industrial and manufacturing advancements globally. Its key contributions include the creation of robust testing frameworks for material properties such as tensile strength, hardness, ductility, and corrosion resistance. These parameters ensure uniform quality and safety standards across industries.
For instance, the ASTM A370 standard provides detailed guidelines for mechanical testing of steel products, including tensile testing, yield strength determination, and elongation analysis. Another critical contribution is the ASTM G48 standard, which defines methodologies for testing the pitting and crevice corrosion resistance of stainless steels and related alloys. These standards are essential in guaranteeing material performance under diverse operational conditions, ranging from construction to chemical processing environments.
By setting these benchmarks, ASTM International creates a foundation for engineering reliability, safety, and innovation, serving as a critical resource for engineers, researchers, and manufacturers worldwide.
International Standards Development
International standards development involves a rigorous and collaborative process to establish consensus-based technical specifications, guidelines, and benchmarks. This process ensures uniformity, interoperability, and safety across industries, facilitating seamless trade and innovation globally.
Key Questions and Corresponding Parameters:
1. What are the critical factors considered in material standards development?
- Chemical Composition Limits (e.g., carbon content in steels ≤ 0.03% for enhanced corrosion resistance).
- Mechanical Properties (e.g., tensile strength, yield strength).
- Corrosion Resistance Metrics (e.g., pitting resistance equivalent number, PREN ≥ 40 for high-performance alloys).
- Temperature and Pressure Tolerances (specific ranges depend on operational environments, e.g., 600–800°F for heat-resistant materials).
2. How is reliability ensured in material standards?
- Use of Reproducible Testing Protocols (e.g., ASTM G48 for pitting and crevice corrosion).
- Mandatory Quality Assurance Processes (e.g., non-destructive testing like ultrasonic inspection).
- Alignment with International Codes (e.g., ISO 9001 for quality management systems).
3. What are the primary benefits of international standards?
- Enhanced Global Compatibility (e.g., standardized dimensions for fittings and connectors).
- Improved Safety and Risk Management (standards dictate minimum safety requirements).
- Facilitation of Research and Development (providing uniform benchmarks for innovation).
These parameters and methodologies exemplify how international standards serve as a vital framework for global engineering and industrial advancements.
Why Are ASTM and AISI Important to the Steel Industry?
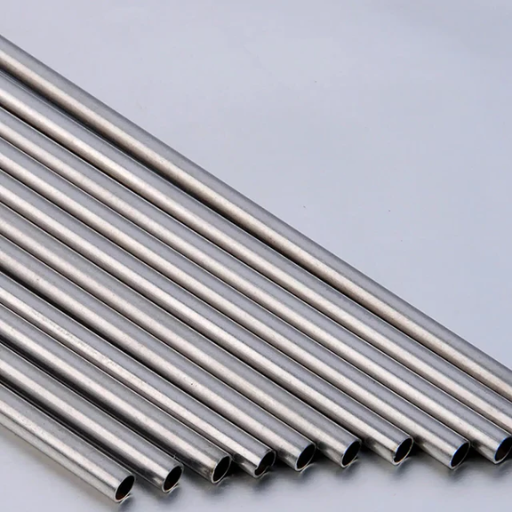
Both ASTM (American Society for Testing and Materials) and AISI (American Iron and Steel Institute) play pivotal roles in the steel industry by establishing globally recognized standards that ensure consistency, quality, and safety. ASTM provides specifications for steel composition, mechanical properties, and testing methods, enabling manufacturers to produce reliable materials that meet specific applications. AISI, on the other hand, focuses on industry-wide support by promoting the use of steel, developing product standards, and contributing to innovative research. Together, they facilitate interoperability, enhance trade, and drive technological advancements within the steel sector, making them indispensable to the industry.
Enhancing the Iron and Steel Industry
Key Strategies for Enhancing the Iron and Steel Industry
To enhance the iron and steel industry, it is essential to focus on a combination of innovative technologies, sustainable practices, and effective policy implementation. Investments in advanced manufacturing processes, such as electric arc furnaces (EAF) and hydrogen-based steel production, can significantly reduce carbon emissions while improving efficiency. Adopting circular economy principles, including increased recycling rates and waste minimization, plays a key role in achieving environmental sustainability.
Furthermore, robust workforce training programs are critical to upskilling employees and fostering innovation within the sector. Governments and industry leaders must collaborate to establish favorable policies and trade agreements that protect domestic production, encourage exports, and ensure supply chain resilience. By integrating these strategies, the iron and steel industry can become more competitive, environmentally conscious, and better equipped to meet evolving global demands.
Supporting the American Steel Industry
Key Strategies to Support the American Steel Industry
1. Upskilling the Workforce
-
- Technical Parameter: Implement targeted training programs to improve worker proficiency in advanced manufacturing and automation technologies. Metrics to track include the number of employees certified in relevant technical fields and percentage adoption of AI and machine learning within production systems.
- Outcome: A qualified and adaptive workforce capable of handling state-of-the-art production processes, boosting both productivity and innovation.
- Enhancing Supply Chain Resilience
- Technical Parameter: Invest in smart logistics systems, including real-time supply chain monitoring tools and predictive analytics to identify potential disruptions before they impact operations. Key indicators include reduced lead times and inventory turnover ratios.
- Outcome: Greater operational stability and less susceptibility to global supply chain fluctuations.
- Driving Environmental Sustainability
- Technical Parameter: Transition to low-emission production technologies like electric arc furnaces (EAF), paired with renewable energy sources. Measure progress through metrics such as CO₂ emissions per ton of steel produced and percentage use of recycled materials.
- Outcome: Compliance with environmental regulations and improved perception of the steel industry as a sustainable sector.
- Encouraging Policy and Trade Support
- Technical Parameter: Advocate for protective tariffs against unfair foreign imports and incentives for domestic innovation. Success can be quantified by the implementation of favorable trade laws and growth in export figures.
- Outcome: A level playing field and a global competitive edge for American steel producers.
Integrating these strategies is essential for strengthening the American steel industry’s position in a competitive, globalized economy. By focusing on technical excellence, policy reform, and sustainability initiatives, the sector can achieve long-term growth and stability.
Ensuring Standard Specifications
Ensuring standard specifications across the steel industry is crucial to maintaining quality and consistency in production. From my understanding, this involves adhering to established benchmarks such as ASTM or ISO standards, which provide detailed guidelines for material properties, fabrication practices, and product testing. By implementing uniform specifications, we can enhance product reliability, facilitate trade by meeting international requirements, and reduce production errors. Furthermore, these standards support technological advancements and promote sustainability by optimizing resource use and manufacturing processes. Compliance with these specifications not only strengthens the industry’s global reputation but also fosters trust among consumers and stakeholders.
Reference Sources
- Difference between AISI and ASTM standard specification – Oshwin
- Difference between AISI and ASTM standard – Nickel Alloys Online
- AISI and ASTM steel grades discussion – Reddit Engineering
- What are the Different Types of Steel and Steel Grades? – Metal Supermarkets
- Steel Grades Guide – Acrodyne
Frequently Asked Questions (FAQs)
Q: What is the primary difference between AISI and ASTM standards?
A: The primary difference between AISI and ASTM standards is that AISI is the American Iron and Steel Institute, which focuses on the classification of steel and iron types, while ASTM is the American Society for Testing and Materials, an international organization that develops voluntary consensus technical standards for a wide range of materials and products, including steel and iron.
Q: How does AISI classify steel types?
A: AISI classifies steel types based on their chemical composition and physical properties, providing a standard classification that helps in identifying materials with similar characteristics within the North American steel industry.
Q: What role does ASTM play in the steel industry?
A: ASTM plays a significant role in the steel industry by setting standard test methods, standard practices, and terminology standards to ensure materials and products meet specific quality and safety requirements. This helps maintain consistency and reliability in the steel and iron industry.
Q: Are AISI standards applicable internationally?
A: AISI standards are primarily used within the North American steel industry. In contrast, ASTM is an international organization whose standards are recognized and used worldwide, making ASTM’s reach much broader in terms of global applicability.
Q: Can ASTM standards apply to materials other than steel?
A: Yes, ASTM standards apply to a wide variety of materials and products beyond steel and iron, making it one of the largest standards organizations. It covers materials with similar characteristics across different industries, ensuring broad applicability.
Q: Is there a particular standard that both AISI and ASTM collaborate on?
A: While AISI focuses on steel type classification and ASTM on testing and material standards, they sometimes collaborate to ensure that the standard classifications and practices complement each other, particularly in developing comprehensive steel standards.
Q: Why are ASTM standards considered a benchmark in the industry?
A: ASTM standards are considered a benchmark in the industry due to their rigorous development process, which involves voluntary consensus technical standards. This process ensures that the standards are comprehensive, reliable, and applicable across various industries globally.
Q: How do these standards benefit the construction industry?
A: These standards benefit the construction industry by providing clear guidelines for the quality and performance of materials. This ensures safety, reliability, and consistency in construction projects, which is crucial for structural integrity and long-term durability.
Q: What is the historical significance of AISI and ASTM in the steel industry?
A: AISI and ASTM are two of the oldest trade associations in the steel industry, with AISI focusing on steel and iron classification and ASTM on developing comprehensive standards. Their historical significance lies in their contributions to the development and regulation of steel standards, which have shaped the industry’s evolution.