Stainless steel can be found almost everywhere. From kitchen tools to building structures, their application are innumerable. It is strong, does not corrode easily, and looks good, which is why it is extensively used in various industries. The twist, however, is that some types of stainless steel are practically non-magnetic. If that comes as a surprise for you, then learning about stainless steel’s and magnetism’s relationship will definitely spark your interest. Why is it that some types of stainless steel are magnetic while others aren’t? What determines such behavior? This article aims to answer these questions by examining the composition and structure of stainless steel while providing clarity about its magnetic properties. You do not have to be a materials science expert or an industry professional, a mere curious learner will enjoy the insights uncovered in the depths of stainless steel’s domain.
What Makes Stainless Steel Magnetic or Non-Magnetic?
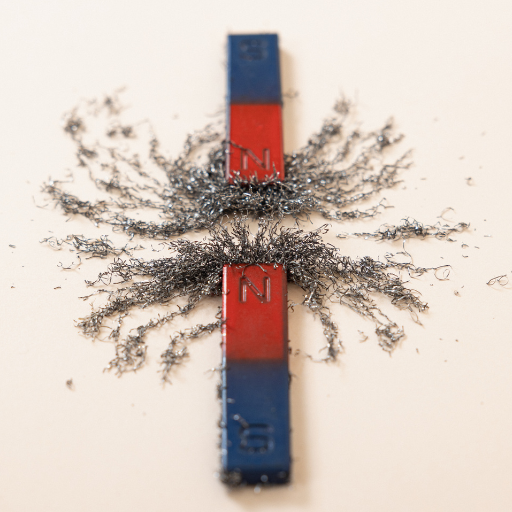
The microstructure of stainless steel, which is affected by its chemical composition and the alloying elements, is what primarily controls its magnetic properties. Austenitic stainless steels are generally non-magnetic due to their face-centered cubic (FCC) crystall structure, containing high amounts of chromium and nickel. Conversely, ferritic and martensitic stainless steels containing less or no nickel and possessing body-centered cubic (BCC) structures are magnetic. It is clear that both composition and processing determine magnetic characteristics since heat treatment and mechanical processing also affect whether a specific grade becomes magnetized.
Understanding the Role of Alloy Composition
the properties of stainless steels, especially their magnetic response, are critical to the alloy composition. The amount of nickel, chromium, and iron present in a material will determine whether it is magnetic. For example, the high nickel content in austenitic stainless steels non-magnetic due to the stabilized FCC structure, while ferritic or martensitic grades with lower or no nickel tend to the BCC structure, which is magnetic. Which combination of alloy composition and processing techniques is equally important; slight changes to formulation or heat treatment cycles can change performance significantly. Each application requires materials with great attention to these criteria.
Influence of Crystal Structure on Magnetism
The crystal structure directly correlates with whether a material is magnetic or not. Take, for example, the FCC structure that austenitic stainless steel has; it is non-magnetic because it interferes with the alignment of a magnet’s polarity. On the other hand, the BCC structure, which is common in ferritic or martensitic stainless steels, is a magnetic material since it facilitates the alignment of magnetic domains. As a result, the relationship between alloy constituents and crystal structure is the main reason for the magnetic characteristics.
How Does the Type of Stainless Steel Affect Its Magnetism?
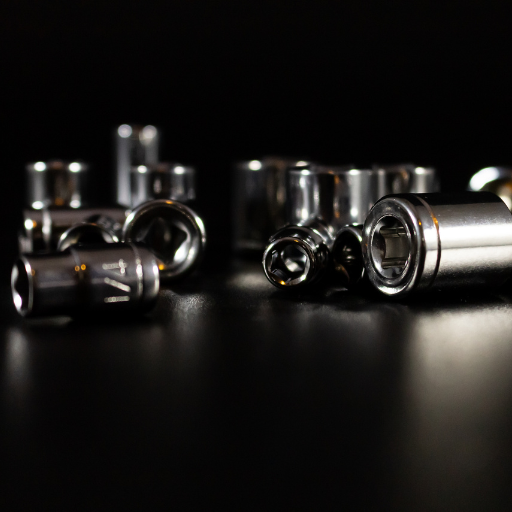
The kind of stainless steel is important in magnetism, as I’ve learned over the years. Austenitic stainless steels, with FCC crystal structure, are non-magnetic because their magnetic domains aren’t aligned. Whereas, ferritic and martensitic stainless steels with BCC structure are magnetic, as their domains can align under a magnetic field. The crystalline structure with the amount of alloying elements such as chromium, nickel, and carbon, defines the magnetic behavior of the material. Understanding the specific type of stainless steel and its magnetism poses great importance when selecting stainless steel for particular applications.
Characteristics of Austenitic Stainless Steel
Austenitic stainless steels have non-magnetic properties, exceptional corrosion resistance, and superior ductility. These qualities stem from their FCC (face-centered cubic) crystal structure, which are stabilzed with alloying nickel and nitrogen. Their ability to maintain mechanical integrity over a vast range of temperature makes them useful in chemical processing, food production, medical applications, and other critical industries.
Exploring Ferritic Stainless Steel’s Magnetic Properties
In terms of stainless steel, ferritic has very unique and distinct characteristics, one being its magnetic properties. Unlike austenitic stainless steel, ferritic grades have a body-centered cubic (BCC) crystal structure, further explaining why they are inherently magnetic. Their high content of iron, alongside the low amounts of nickel, supports these properties. This is why ferritic stainless steels are so useful in industries such as electrical engineering and automotive, where magnetism is crucial. From an environmental viewpoint, their magnetic behavior makes sorting and recycling easier, which is arguably more beneficial.
Differences Between Martensitic and Duplex Stainless Steels
I notice that the composition, properties, and uses of martensitic and duplex stainless steels differ. Let me explain them one by one.
- Composition
-
-
- Over time, it has been recognized that martensitic stainless steels encompass higher amounts of carbon in conjunction with chromium, which greatly aids in attaining the distinctive hardness characteristic of stainless steels after appropriate thermal treatments.
- In contrast, duplex stainless steels are interstitial solid solutions of an austenitic and a ferritic phases, with nickel and chromium in equal proportion, and often, other elements such as molybdenum and nitrogen for improved performance attributes.
-
- Strength and Hardness
-
-
- Martensitic stainless steels are renowned for their hardness and are often employed in situations where wear resistance is critical. Their high hardness can be attributed to the controlled heat treatment of the material and the amalgamation of a martensitic crystal structure.
- As strong as the duplex stainless steels are, their strong suit is their excellent tensile and yield strength. Their functionality makes them perfect candidates for heavy-duty applications such as the construction of chemical plants or offshore facilities.
-
- Corrosion Resistance
-
-
- In the case of Duplex steels, these can be expected to exhibit moderate corrosion resistance making them useful for applications where strength is put in focus as opposed to the degree of exposure to aggressing environments.
- Thanks to their peculiar micro and macro structure and the unique alloying elements, duplex stainless steels outclass martensitic types in resistance, namely to stress corrosion cracking and pitting corrosion.
-
- Ductility and Toughness
-
-
- Toughness increases with martensitic steels, yet curbs ductility, making them prone to fracture in some situations.
- Duplex steels outperform and offer better balance of ductility and toughness compared to austenitic and martensitic steels, excelling in a myriad of scenarios.
-
- Applications
-
-
- Knives, surgical instruments, and even turbine blades utilize martensitic stainless steels because of their enduring nature towards hardness and wear resistance.
- Due to their extreme mechanical attributes and ability to endure rust, duplex stainless steels are preferred in the oil and gas industry, marine equipment, and even chemical tankers.
-
The decision regarding the selection of these two alternatives is determined by the parameters of your project, which either need hardness and strength or toughness and resistance to corrosion. Having this information allows you to easily make choices that take performance and durability into account.
Why Are Some Stainless Steels Magnetic While Others Are Not?
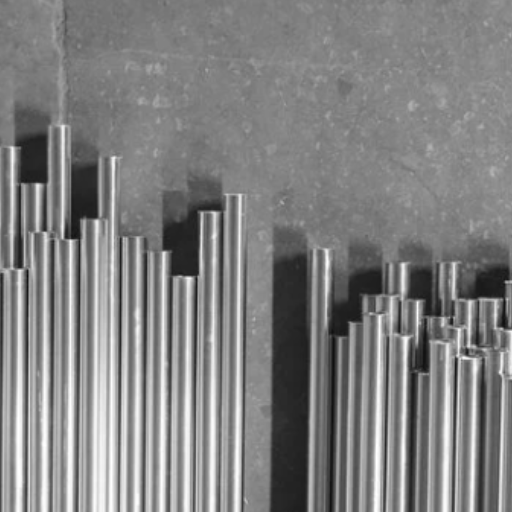
The primary distinctive qualities of stainless steels and their grades, from supermartensitic to austenitic, rest on the magnetic interactions arising from the atoms’ positioning in the crystalline lattice. Stainless steels of BCC (Body Centered Cubic) or Body Centered Tetragonal dominated structural types like the ferritic and martensitic grades, are magnetic on account of their iron atoms’ alignment. Alternatively, austenitic stainless steels having face-centered cubic (FCC) structure predominantly are non-magnetic because this configuration tends to destroy the magnetism of iron. In austenitic steels, deformation or cold working can slightly magnetise the material because of martensite formation. Knowing these distinctions is important when choosing the right stainless steel for appealing magnetic or anti-magnetic features.
The Impact of Nickel and Chromium in Steel
nickel and chromium are perhaps the most important constituents of stainless steel, and neither of their components should be undermined. Nickel, for instance, adds significantly to the ability of steel to resist further corrosion and increases the toughness of the steel while also stabilizing the austenitic structure, which is critical for steel used in extreme conditions. Chromium, on the other hand, as the name suggests, forms protective oxides on the surface of steel, which is responsible for the stainlessness or corrosion resistance of the steel. The addition of both these features is why stainless steel can excel under aggressive conditions. Having worked extensively with these materials, it is apparent to me that too much or too little nickel or chromium in an alloy impacts how well the steel performs, holds up, or outlasts its competition in the aerospace, construction, or medical device industries. It is crucial to understand what factors to study in order to choose the correct alloy because they play a critical role in selecting the proper alloy for any given application.
How Heat Treatment Alters Magnetic Properties
By modifying the internal structure of a material, heat treatment has the capacity to change its magnetic properties. Processes like quenching or annealing impact the spatial position of atoms, the phase composition of the atoms, and the volume of the magnetic domains within the material. An example includes heat treatment being able to alleviate some internal stresses or changing some ferritic structures to austenitic ones, which reduces the magnetic permeability. On the other hand, controlled cooling has the potential to maintain or improve magnetic properties depending on the type of alloy. The specific material composition and the heat treatment process determine the results.
Can Non-Magnetic Stainless Steel Become Magnetic?
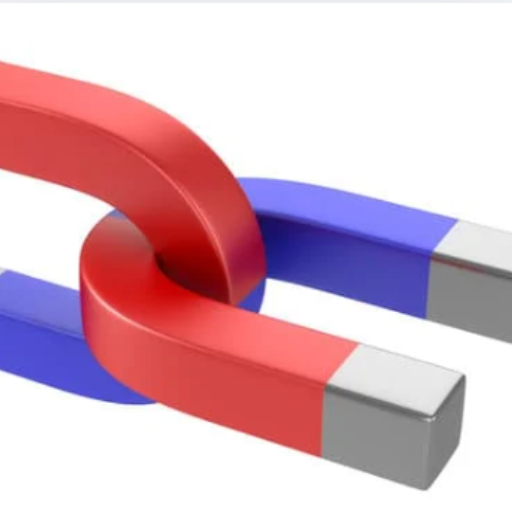
Indeed, non-magnetic stainless steel can acquire magnetic properties under specific circumstances. the most important factor is the microstructural changes of the material. Physical processes, such as bending, rolling, and extensive machining of stainless steel, can induce the formation of a magnetic phase known as martensite. Improper heat treatment and thermomechanical processes may change the structure and increase magnetism as well. These processes, if not carefully controlled, may be able to achieve the required magnetism, or lack thereof, in components made of stainless steel.
Effects of Mechanical Stress on Magnetism
A contribution of mechanical stress can markedly change the magnetism of stainless steel by modifying its microstructure. Processes such as cold working or deformation lead to the formation of strain-induced martensite, which improves magnetic characteristics. Control of stress through heat treatment, deliberate machining, and grade selection of the stainless steel performed is crucial to minimizing or tailoring the magnetic effects for certain applications.
Temperature Changes and Their Influence on Magnetic Properties
Temperature plays a crucial role in the behavior of the material’s microstructure and, consequently, the magnetism of the material. As it relates to changes in temperature and the impact on the stainless steel’s magnetism, I may say it is pretty reasonable and pertinent to study these effects. Remember these core aspects:
- Curie Temperature: This is a noteworthy threshold involving ferromagnetic entities like certain variants of stainless steel. Above this temperature, the material tends to transform from a ferromagnet to a paramagnet. For example, ferritic stainless steels are exposed to an increased temperature near or above their Curie point, where there is a significant decrease in their magnetic response.
- Thermal Expansion and Structural Changes: At higher temperatures, thermal expansion can lead to a change in the atomic spacing within the steel. This small alteration can lead to the modification in the order of magnetic domains, hence decreasing the magnetic properties. This phenomenon is particularly prominent among grades that are susceptible to phase transformations, and in particular, those which are both ferritic and austenitic.
- Phase Transformation: Some stainless steels can achieve some phase transformation at a given temperature range, including but not limited to austenite to ferrite and even martensite at lower temperatures. This transformation has a direct effect on magnetism because, unlike austenitic steel, which is mostly non-magnetic, both ferritic and martensitic phases are considerably more magnetic.
- Quenching and Cooling Rates: The pace at which the heat is removed, following exposure to high temperatures, dictates the nature of microstructure phases that may or may not form, including martensite. An increased magnetism due to quenching could be caused by strain induced phases or lower magnetism due to controlled cooling that enables a more stable structure.
Grasping these parameters allows us to forecast and manage the magnetic characteristics of stainless steel with extreme precision at different temperature levels. This is particularly important, for instance, in cryogenics, high-temperature environments, or delicate electromagnet systems, where magnetism is crucial to operational capacity.
What Are the Practical Applications of Magnetic and Non-Magnetic Stainless Steel?
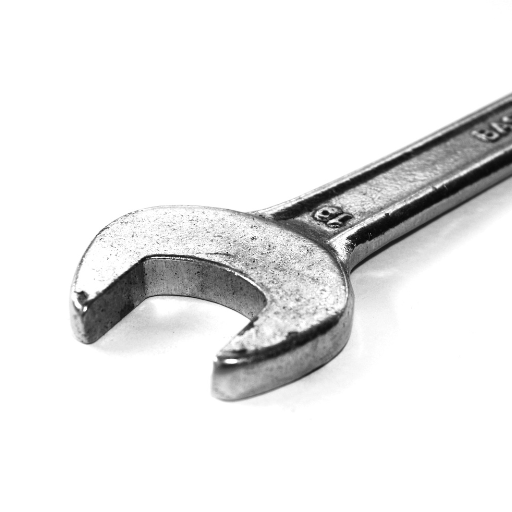
Such machinery includes motors and industrial sensors, as well as other specialized equipment, which makes use of magnetic stainless steel. Stainless steel with non-magnetic properties is more suitable for medical equipment and instruments, aerospace parts, and advanced electronics, where a lesser magnetic impact is required. Industries are able to select the most appropriate kind of stainless steel relevant to their exact operational and surroundings requirements, owing to its varied characteristics.
Choosing the Right Type of Steel for Industrial Use
a thorough examination of both the application and environmental conditions is vital in choosing the right type of steel for industrial purposes. An excellent example is the use of magnetic stainless steel in industries where strength and magnetism are highly needed, like in the manufacturing of motors or certain types of machinery. In contrast, non-magnetic stainless steel is better suited in situations where there is minimal magnetic interference, like in the medical and aerospace fields. A detailed analysis of the operational requirements alongside the material characteristics ensures optimal performance, durability, and safety for every project.
Impact on Consumer Products and Kitchenware
Both types of stainless steel, magnetic and non-magnetic, are important components in consumer products as well as kitchenware. Because ferritic grades are magnetic stainless steels, they are more durable and cheaper, which makes them favorable for knife blades and some types of cookware. Non-magnetic stainless steels, such as austenitic grades, have greater resistance to corrosion and are commonly used with expensive kitchen appliances, cutlery, and even storage containers. In the end, the choice relies on the expected application in relation to the levels of durability, resistance, and functionality required.
Reference
- Why is Stainless Steel Not Magnetic? – Mead Metals
- Magnetic Properties of Stainless Steel – Geometrics
- Is Stainless Steel Magnetic? – Metal Supermarkets
Frequently Asked Questions (FAQs)
Q: What makes stainless steel magnetic or non-magnetic?
A: The magnetic properties of stainless steel depend on its crystal structure. Austenitic stainless steels, like 304 and 316, are typically non-magnetic because their structure prevents a magnetic pull. In contrast, ferritic and martensitic stainless steels, which are part of the 400 series, have a structure that allows them to be magnetic.
Q: Is 304 stainless steel magnetic?
A: 304 stainless steel is generally considered non-magnetic in its annealed state. However, it can become partially magnetic after cold working due to the formation of martensitic structures.
Q: Why is 316 stainless steel non-magnetic?
A: 316 stainless steel belongs to the austenitic family of stainless steels, which have a face-centered cubic crystal structure. This structure is not conducive to magnetism, making 316 stainless steel non-magnetic in its annealed form.
Q: Can cold working affect the magnetic properties of stainless steel?
A: Yes, cold working can affect the magnetic properties of austenitic stainless steels like 304 and 316. Cold working can induce a transformation to a martensitic structure, which has a little magnetic pull, making the steel partially magnetic.
Q: Are all types of stainless steel non-magnetic?
A: No, not all types of stainless steel are non-magnetic. While austenitic stainless steels, such as those in the 300 series, are typically non-magnetic, ferritic and martensitic stainless steels, like those in the 400 series, are magnetic.
Q: What role does nickel play in the magnetism of stainless steel?
A: Nickel is added to austenitic stainless steels to stabilize their face-centered cubic crystal structure, which is non-magnetic. This is why 304 and 316 stainless steels, which contain nickel, are generally non-magnetic.
Q: How do grades 304 and 316 compare in terms of magnetic properties?
A: Both 304 and 316 grades are austenitic stainless steels and are non-magnetic in their annealed state. However, they can become slightly magnetic after cold working. The primary difference between them lies in their corrosion resistance, with 316 offering greater resistance due to the addition of molybdenum.
Q: Why do some stainless steels become magnetic over time?
A: Some stainless steels can become magnetic over time due to mechanical deformation or cold working, which can induce a change in the crystal structure, resulting in increased magnetic properties.
Q: What is the significance of ferrite in magnetic stainless steel?
A: Ferrite is a magnetic phase of iron, and its presence in stainless steel contributes to its magnetic properties. Steels that contain higher amounts of ferrite, such as ferritic stainless steels, have a weak magnetic attraction.