Selecting the most appropriate type of stainless steel for your application is pivotal in achieving optimal performance, cost-effectiveness, and the desired life of the product. Two of the most controversial choices in the market are Duplex Stainless Steel and 316 Stainless Steel, both known for their usability and corrosion resistance. But which one best suits your requirements? This article examines the differences, benefits, and disadvantages of these alloys in depth so that you can make an educated choice. Stemming from the most basic of mechanical properties to environmental considerations for the materials, we’ll strive to cover all the necessities to aid you in deciding which stainless steel will best suit your next project.
What Are the Key Differences Between Duplex Stainless Steel and 316 Stainless Steel?
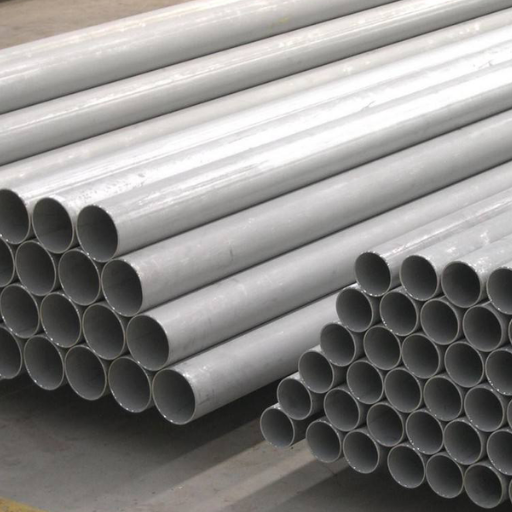
The differences between Duplex Stainless Steel and 316 Stainless Steel include composition, strength, and resistance to corrosion. Compared to 316 Stainless Steel, Duplex Stainless Steel has better stress corrosion cracking resistance, mechanical strength, and resistance to stress corrosion cracking because it is a blend of austenitic and ferritic structures. 316 stainless steel as an austenitic alloy on the other hand is well known for it’s excellent resistance to general corrosion, especially in environments with chlorides but has lower strength than duplex grades.
Both types of steel have their differences in applications too. Being cost effective, Duplex Stainless Steel is used in structural applications and more hostile environments like chemical processing and marine industries. 316 stainless steel is used in food and pharmaceutical equipment which require a high level of cleanliness but have less demanding environments. As is clear, the decision is a balance of many factors including the environment’s conditions and the application’s mechanical specifications.
Differences in Chemical Composition and Microstructure
Like 316 stainless steel, duplex stainless steel exhibits different chemical composition and microstructure with uniquely stainless properties. Compared to 316, duplex stainless steel has much greater chromium (19-28%) and nitrogen content while having a lower nickel content. This combination increases its strength and resistance to corrosion, specifically stress corrosion cracking and pitting in chloride ion rich environments.
On the other hand, 316 stainless steel consists of a simpler austenitic microstructure made chiefly of chromium (16-18%), nickel (10-14%), and molybdenum (2-3%) which enhances corrosion resistance in mildly aggressive environments. The two-phase microstructure of duplex stainless steel, which consists of ferrite and austenite, enables greater mechanical strength and durability under high-stress conditions to the alloy thereby making it suitable for more demanding applications.
Analyzing Properties of Resistance to Corrosion
The alloy type, its environment, and coatings affect a material’s corrosion resistance. For instance, the stainless steels grade 316 and 2205 duplex stainless steel, which have higher chromium and molybdenum content, suffer from chloride induced corrosion to a lesser extent than 304 stainless steel. Recent studies show that 316 stainless steel has greatly increased pitting resistance, with a Pitting Resistance Equivalent Number (PREN) surpassing 24. 2205 duplex steel outperforms this with a PREN value that tends to exceed 35, which makes it ideal for use in marine and offshore applications.
Aluminum alloys, especially the 5000 series, are also employed in marine settings because they can withstand oxidation due to the formation of a self-protective oxide layer. However, these alloys are prone to galvanic corrosion when paired with more electrochemically active materials. Other than that, titanium has the most resistance to corrosion, especially in seawater, because of the stable, dense, and adherent oxide film it has. Its use is often restricted to critical applications like desalination systems or subsea equipment because of the higher cost.
Protective coatings are critical to the operational performance of materials. Apart from thermally sprayed aluminum, epoxy and polyurethane coatings exhibit the lowest corrosion rates. Coated samples performed better than uncoated samples in controlled salt spray chamber tests by over 85%. Newer developments in nanocoating technologies enhance the durability and effectiveness of these protective coatings, making them ideal for long-term use in corrosive settings. Knowledge of these material properties optimizes the selection of protective coatings based on the degree of corrosion resistance along with specific environmental conditions.
Strength and Toughness Differences
All engineering applications have specific requirements that materials need to meet. These depend on their strength and toughness properties. Strength, in this case, refers to the material’s ability to withstand an applied load or force of failure, while toughness measures a material’s capacity to absorb energy and deform without fracturing. Construction materials have these two factors synergistically interdependent and change depending on element composition, microstructure, external conditioning, and others.
Ultra-high-strength steel, with its robust tensile strength of 1000 MPa, is a stark example of a high-strength material. Although high, it’s not very tough and more susceptible to tears during impact. In contrast, lower strength titanium alloys possess optimal ratios of these factors, like Ti-6Al-4V which withstands extremely high tensile forces of 900-1200 MPa is still able to pull high amounts of toughness as showcased by Charpy impact energy exceeding 50 J on room temperature.
In addition, the strength and toughness of the polymeric and composite materials also have some differences. An example is advanced carbon-fiber-reinforced composites which, when properly stacked, have great tensile strength in the range of 3,500 MPa and significant toughness. These properties, however, are extremely anisotropic, and the composite’s performance can change dramatically based on the load’s angle versus the fiber’s direction. Similarly, some thermoplastics like polycarbonate have strong impact resistance of over 850 J/m, but moderate tensile strength of about 70 MPa, making those materials useful in protective equipment.
The balance between strength and toughness indicates the essential level of material design and processing. Advanced engineering techniques such as alloying, grain refinement, phase change, and heat treatment are often applied to optimize the strength-toughness ratio to exact operational specifications. To provide tailored solutions, these measures combine material properties with varying mechanical loads and ensure consistent material integrity while enduring fluctuating stress levels.
How Does Duplex 2205 Compare to 316 Stainless Steel?
Both Duplex 2205 and 316 stainless steel are widely utilized, but they have some differences. Duplex 2205 has higher strength and greater resistance to corrosion in chloride environments, particularly in cases of stress corrosion cracking. It also has a higher yield strength which means it can be built from thinner, lighter components in structural applications. Meanwhile, 316 stainless steel is more affordable and makes it easier to cut the way it is shaped. This makes it more appropriate for places or environments that are less demanding or need a lot of machining. Choosing between these two is mostly about what is needed regarding operations and the environment used.
Comparison of Mechanical Properties of Duplex 2205 and 316
Duplex 2205 features superior mechanical properties compared to 316 due to its duplex microstructure which has a mixture of austenitic and ferritic phases. The tensile strength of Duplex 2205 ranges approx. From 621 MPa to 800 MPa, which is much higher than that of 316 stainless steel, which averages around 515 MPa. In addition, Duplex 2205 provides higher yield strength at about 450-550 MPa compared to that of 316 which is generally in the range of 200-300 MPa.
The elongation at break for Duplex 2205 is approximately 25%, which is still lower than 316’s typical elongation range of 40%-50%. This means that 316 stainless steel is more ductile. However, the relatively lower ductility of Duplex 2205 is offset by exceptional resistance to deform under high-stress conditions. The difference in mechanical performance means that Duplex 2205 is the material of choice for applications that require high strength, low weight, and high corrosion resistance, while 316 is ideal for applications that require greater formability and easy welding.
Corrosion Resistance in Chloride Environments
Chloride-containing environments, particularly marine or industrial ones, are extremely harmful to the longevity of materials due to the risk of pitting and crevice corrosion. Compared to 316 stainless steel, Duplex 2205 demonstrates much higher corrosion resistance in these conditions due to the 22-23% chromium and 3-3.5% molybdenum, which allow Duplex 2205 to form a more stable and protective passive film on the surface.
The Critical Pitting Temperature (CPT) is important for measuring the level of localized corrosion an alloy suffers. For Duplex 2205, the CPT is usually greater than 35°C during ASTM G48 testing, surpassing 316 stainless steel which typically has a CPT of less than 25°C for similar conditions. Furthermore, Duplex 2205’s pitting resistance equivalent number (PREN), which considers chromium, molybdenum, and nitrogen alloying proportions, is around 35-40. This value is significantly better than 316 stainless steel, which has a PREN of 23-28. The higher PREN is, the better the material is at resisting corrosion by chloride ions. Thus, making Duplex 2205 more reliable in highly aggressive environments.
These improved corrosion resistance features of Duplex 2205 also apply to stress-corrosion cracking (SCC). While austenitic grades like 316 undergo SCC failure from the combination of chlorides and tensile stress, Duplex 2205 is more resilient due to the dual-phase microstructure. This makes it ideal for critical applications such as chemical processing plants, offshore structures, desalination plants, and systems where chloride corrosion is a chief concern.
Weldability and Fabrication Considerations
Duplex 2205 stainless steel has fair weldability, but its useful properties require attention during machining operations. Most important from the welding perspective is carefully preserving the ferrite to austenite ratio in the HAZ (heat affected zone). High levels of heat input, as in welding, can result in 40-60 phase imbalance, which will severely aggravate corrosion and mechanical properties. It is generally suggested that heat input and interpass temperature be maintained below 300 degrees F (149 degrees C) to avert microstructural damage. Creating some microstructural phases, i.e., sigma phase, can degrade toughness and corrosion resistance which is highly undesirable.
Most often, post weld heat treatment eliminates the need for most other duplex grades, 2205 being one of them, thus rendering them more economical relative to materials that require additional treatments. This, however, does not reduce the importance of monitoring parameters such as filler material selection, which require additional thermal processes. The alloy composition is often matched or minimally exceeded using proprietary ER2209 filler metals to ensure superior mechanical and corrosive end of the alloys and posses enhanced strength and resistance.
Regarding fabrication, Duplex 2205 is more difficult to machine because of its higher strength and hardness when compared to other stainless steels. Higher rigidity blades subjected to slower cutting speeds have to be used to avoid rapid tooling degradation and high precision loss. In addition, the tool’s high yield strength enables designers to save a significant amount of weight, as thinner parts could be used safely without compromising reliability. Thoughtful analysis of these factors helps ensure effective usage of Duplex 2205 in harsh industrial environments.
When Should You Use Super Duplex Instead of 316 Stainless Steel?
Super Duplex stainless steel is more advantageous than 316 stainless steel in applications that require greater strength, superior performance in corrosive environments, or better overall performance in severe conditions. It is most useful in the oil and gas, chemical processing, and marine sectors where there is aggressive exposure to chemicals, high-pressure, and seawater. Furthermore, Super Duplex involves enhanced mechanical properties which makes it possible to lower the thickness of materials while maintaining structural integrity. This results in reduced weight and cost.
Applications at High Temperatures and Pressures
Superalloys and advanced stainless steel alloys are highly used in HPHT or high-temperature and high-pressure applications. This is due to their exceptional performance in operational conditions that are far more extreme compared to typical. These materials also boast remarkable thermal stability, superb resistance to deformation under load (creep resistance), and mechanical strength guaranteeing them dependability in perilous environments. The uses of HPHT in the below list come with their associated benefits and core requirements:
- Oil and Gas Exploration: Drilling activities in deep wells and subsea locations must deal with extreme temperature conditions of more than 150 degrees Celsius and greater than 20,000 psi pressure. The materials used in these conditions need to be stress corrosion resistant to cracking, sulfide stress cracking, and hydrogen-induced cracking.
- Aerospace Engines: Jet turbines undergo acute temperature stress sustaining above 1,800°F (980°C). The turbine blades, precision manufactured from high-strength nickel-based superalloys, require unyielding structural rigidity to survive extreme thermal and pressure environments.
- Power Generation Turbines: Advanced steam and gas turbines face extreme and fluctuating temperature and pressure differentials. Components experience extreme thermal cycling and oxidation fatigue; therefore, many use advanced coatings for enhanced performance at temperatures above 1,200°F (650°C).
- Chemical Processing Equipment: Reactors, heat exchangers, and pressure vessels in chemical plants endure vigorous temperatures and harsh chemicals. Alloys with greater than nominal pitting, crevice corrosion and thermal deformation due to high molybdenum and chromium content are used to prevent pitting and crevice corrosion.
- Industrial Heat Treatment: Sintering and furnace environments require alloys which can withstand prolonged exposure to high temperatures, usually exceeding 2,000°F (1,093°C). In these applications, alloys with low scaling resistance and high carburization resistance are of utmost importance.
All other alloys in conjunction to these are selected explicitly with utmost precision regarding operational stress, service life, and environmental considerations to guarantee maximum efficiency and safety in HPHT settings.
Chemical Processing and Oil and Gas Environment
The oil and gas industry, along with other forms of chemical processing, is known to utilize highly corrosive agents and extreme temperatures, prompting the need for specific materials and solutions. Stainless steel, high performance nickel alloys, and Hastelloy are materials used because of their exceptional corrosion resistance properties, which is critical in hydrochloric and sulfuric acid operations. Also, to reduce chemical and equipment wear, advanced coatings like fluoropolymer linings and ceramic-based coating are utilized to extend service life.
Recent studies report that oil and gas extraction processes are done under operating temperatures ranging from -40°F to over 700°F. Other reports show that the pressure goes over 15,000 psi. Such extreme conditions set targets for change; for example, reinforced composite materials with carbon fibers had to be developed to endure these parameters without failing. Moreover, enhanced filtration technologies for separating water, crude oil, and gas have improved operational efficiency by 20 to 30 percent, minimizing the time and servicing required.
Processes like hydrocracking and gas sweetening exemplify the very demanding precision in materials engineering. In gas sweetening, for example, the amine-based systems employed have to defend themselves from the corrosive attack of hydrogen sulfide gases. With the use of duplex stainless steel, the reduction in failure rates in these systems have been improved significantly by 40 percent. Advanced s chemical processing has also brought with it new design techniques of the heat exchanger, employing titanium and zirconium as structural components which provide vastly superior thermal resistance with high structural reliability in aggressively cyclic thermal operations.
These more advanced engineering efforts help increase the efficiency and life of systems within these harsh industries, boost performance, and optimally sustain operations.
Cost-Benefit Analysis for Different Industries
The comparison of duplex stainless steel and 316 stainless steel considers a cost-benefit analysis depending on the application needs. Generally, duplex stainless steel’s strength and corrosion resistance are superior, especially in cases of stress corrosion cracking or chloride-rich environments. It, for instance, performs better in marine and chemical processing industries.
As noted above, the properties of duplex stainless steel do, indeed, carry higher material costs than 316 stainless steel. Still, the lasting life and the lower maintenance costs often offsets this initial expenditure in more extreme environments. 316 stainless steel, however, is less costly for non-aggressive applications, as it offers reasonable corrosion resistance but simple fabrication and welding. The most critical aspect is striking the desired equilibrium between operational parameters, cost factors, efficiency over time, and sustainability.
What Are the Cost Implications of Choosing Duplex vs 316 Stainless Steel?
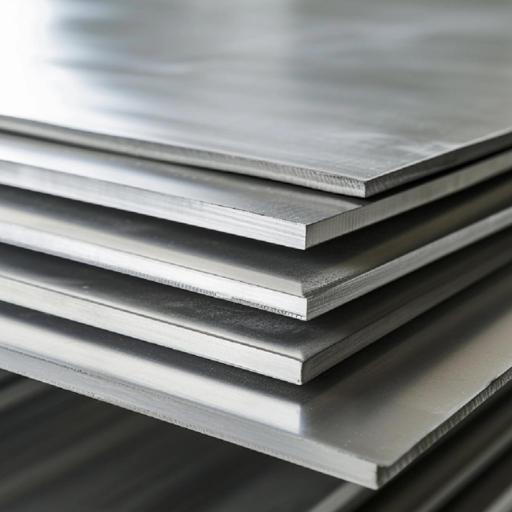
The comparison between Duplex stainless steel and 316 stainless steel revolves mainly around the material’s performance, the costs of its fabrication, and the costs associated with the material over its lifecycle. Duplex stainless steel, which has a microstructure comprising both austenitic and ferritic phases, is commonly known for having better strength and corrosion resistance when compared to 316 stainless steel. Even when the purchase price of Duplex stainless steel is 20-30% higher than other options, its mechanical strength allows for thinner designs in some cases. This might result in lower material requirements and lower manufacturing costs in some applications.
316 stainless steel, on the other hand, is more affordable. 316 stainless steel, an austenitic alloy with high chromium and nickel, as well as molybdenum added, is highly versatile in standard operational environments. Despite being more cost-effective, Duplex grades such as 2205 greatly outperform 316 in harsh conditions like exposure to chlorides or marine applications due to 316s pitting, stress corrosion resistance, and maintenance expenditure, greatly extending the lifeof the found components.
Research suggests that due to aggressive environment support, Duplex stainless steel might offer a 15-20% cut in lifecycle costs for highly durable applications like chemical processing and offshore equipment. Decisions should be made from a mix of the material’s cost, mechanical properties relevant to the ground, and operation and maintenance savings.
Rough Material and Casing Expenditure
Duplex stainless steel’s primary raw materials carry a premium over standard stainless steel as its composition is more sophisticated and usually has higher quantities of chromium, nickel and molybdenum. This expense is offset because of strength that permits supporting design contours to have thinner materials and overall weight. Primary fabrication costs might also increase because of the addition of advanced equipment for accurate welding and managing water jetting driven slicing of robust materials that possess lower ductility. High reliability, significant corrosion resistance and reduced upkeep make the material’s performance justifiable, despite the high initial costs and demand added muscles.
Long-Term Maintenance and Lifecycle Considerations
In assessing long-term maintenance and lifecycle considerations, I consider the material’s durability and how it copes with weathering. I specifically choose high-strength materials with corrosion resistance to mitigate frequent repairs and replacements throughout the asset’s useful life. While these materials may cost more upfront, their effectiveness and reduced maintenance requirements often offset costs over time. This approach helps achieve reliability and sustainability in challenging environments.
How Do Duplex and 316 Stainless Steel Perform in Specific Applications?
Duplex stainless steel is ideal in the marine, oil and gas, and chemical industries because it can withstand stress corrosion cracking while providing excellent strength. Additionally, it pushing structural application costs down due to its high yield strength and reduced material requirements.
In contrast, 316 stainless steel is highly regarded for its enduring corrosion resistance, especially from chlorides and aggressive chemicals, thus making it useful for pharmaceutical equipment, food production, and coastal structures. Although 316 is the weaker choice when compared to duplex in strength, it is by no means an unreliable choice. Its wide availability and proven durability allows for unmatched versatility across multiple industries.
Marine and Offshore Environments
Marine and offshore environments have some of the most material demands because of constant saltwater exposure, high humidity, and changing temperatures. There is always concern about the corrosion, especially for structural components, pipelines, and storage systems. In these cases, materials such as duplex stainless steel are unrivaled because of their excellent mechanical strength and resistance to localized corrosion types like pitting and crevice corrosion, further aggravated by seawater chlorides. For instance, duplex grades like 2205 and super duplex 2507 have a cost-effective strength to corrosion resistance ratio. They also outperform common austenitic grades 304 and 316 used in these applications.
It has been reported that the corrosion rate of carbon steel in a typical marine environment can go as high as 0.1-0.2mm/year. At the same time, duplex stainless steel does not suffer any material loss under these conditions. When used with high-performance alloys, advanced surface treatments and protective coatings increase the operational life of marine structures. Because of the reasons listed above, offshore platforms, underwater pipelines, and shipbuilding rely on duplex and super duplex alloys to maintain structural integrity against these harsh conditions while also reducing maintenance costs.
Pipe Fittings and Chemical Processing
The use of duplex and super duplex stainless steels in chemical processing and pipe fittings is influenced by their corrosion resistance, mechanical strength, and price. These alloys are especially suitable for constructing reactors, heat exchangers, storage tanks, and piping systems because they resist stress corrosion cracking (SCC) and pitting from chlorides and other aggressive chemicals.
For instance, duplex stainless steel is characterized by a more or less balanced quantity of chromium (21-23%) alongside molybdenum (2.5-3.5%) and nickel (4.5-6.5%). Duplex alloys also have a PREN (Pitting Resistance Equivalent Number) value between 30 and 40, meaning they are capable of withstanding localized corrosion in brine, seawater, and acid treatment facilities.
Recent developments in chemical processing have required pipe fittings that can withstand even higher pressures and temperatures. Duplex and super duplex stainless steels have been used more extensively for such applications because these alloys possess high yield strength—about double that of austenitic stainless steels like 316L—so walls and fittings can be made thinner. This saves materials and positively affects costs, improving operational efficiency.
In addition to this, laboratory tests and studies have proven that duplex stainless steel pipe fittings can last longer than 20 years in sulfuric acid environments, at concentrations below 20% and at 50 degrees Celcius. Its durability and ease of fabrication have cemented its place in the critical systems involved in the transport of caustic substances and process fluids. As a result, industries that make use of duplex stainless steels in pipe fittings see a marked decrease in failures and downtime which improves productivity and reliability in processes.
Structural Applications and Stress Corrosion Cracking Resistance
Due to the balance of mechanical strength and resistance to corrosion, duplex stainless steels are increasingly preferred for structural applications. The unique dual-phase microstructure of equal proportions of austenite and ferrite grants these materials high resistance to stress corrosion cracking (SCC) in places where other materials are tested. SCC is a significant concern in high-chloride environments at elevated temperatures, where stainless and carbon steels are prone to premature failure.
The increased performance of duplex grades is related to their higher yield strength, which is frequently greater than the yield strength of austenitic stainless steels 304 or 316, by a factor of two. This increase allows the design of lighter and thinner components while preserving structural strength, further decreasing material costs. For example, duplex stainless steels has demonstrated SCC resistance at contains of sodium chloride up to 3% at temperatures of 150°C. Their resistance to localized corrosion in the form of pitting and crevice corrosion protects structures like bridges, pressure vessels, and even marine structures from long-term damage.
Critical studies provided significant evidence of these alloys being advantageous in petrochemical facilities and wastewater treatment plants due to harsh chemical exposure such as sulfides and chlorides. Usage of these alloys not only increases the structure’s service life but also reduces maintenance costs greatly. The risk of catastrophic failures resulting from tensile stresses is greatly reduced. This reliability makes these alloys preferred in high-stress structural frameworks and in corrosive industrial environments.
What Are the Advantages and Limitations of Both Alloy Types?
These specialty alloys offer nearly unparalleled resistance to corrosion in sulfide and chloride environments. Mechanically, these alloys are sufficiently strong for highly stressed applications. They are durable enough to reduce maintenance costs and chances of equipment failure, promoting operational reliability.
These alloys could be more costly to make because of their unique chemical and mechanical properties. A standard alloy may be cheaper to produce and procure, greatly reducing the initial cost in a project. They could also require more handling, meaning these costs increase. Because of these restrictions, though, demanding industrial environments often find the long-term benefits to heavily outweigh these drawbacks.
316 and 316L Stainless Steel Pros and Cons
Pros
- Corrosion Resistance: 316 and 316L stainless steels resist corrosion, especially in chloride and industrial chemical exposure. This makes them perfect for marine environments, chemical processing, and medical fields.
- High Temperature Strength: These alloys hold up well to elevated temperatures without compromising their mechanical properties or structural integrity, making them suitable for high-temperature environments.
- Malleability and Weldability: Because of 316L’s lower carbon content, it is more preferable to weld than 316. This trait helps prevent carbide precipitation, which increases the chance of corrosion along the weld lines.
- Longevity and Durability: Both grades maintain remarkable longevity in industrial applications due to the molybdenum and nickel, the mechanical strength of the stainless steel and exposure to harsh chemicals.
- Biocompatibility: 316 and 316L’s non-reactive properties render them appropriate for surgical instrumentation and implants.
- Low Maintenance: Their resistance to pitting and rusting leads to low maintenance over their entire lifespan.
Cons
- Higher Cost: Adding molybdenum and nickel increases the price of 316 and 316L compared to 304 stainless steel.
- More Prone to Stress Corrosion Cracking: These alloys can undergo stress corrosion cracking at high temperatures and specific saline environments.
- Complex Processing Requirements: Due to their unique robust properties, the advanced manufacturing techniques used on 316 and 316L increase fabrication costs.
- Density: These grades become slightly denser than the other stainless steel options, which increase weight in structural applications.
- Environmental Impact: High-alloy steel is produced with greater energy and resource expenditure straining the environment further.
Advantages and Disadvantages of Duplex and Super Duplex Stainless Steel
- Strength and Durability: Duplex and super duplex stainless steels are significantly stronger than other grades, such as austenitic. They are around two-fold stronger in tensile and yield strength, enabling their use in high-stress scenarios.
- Corrosion Resistance: Thanks to their unique blend of austenite and ferrite microstructure, they are versatile and resistant to many corrosive environments (especially to stress corrosion cracking and pitting), making them perfect for marine, chemical, and offshore use.
- Cost-effectiveness: Their greater costs during initial purchases is often offset by lower material costs due to higher strength and durability of duplex steels, making the entire project more cost-effective.
- Temperature Performance: Duplex grades do well at moderately high temperatures but also suffer from toughness if maintained over 300 °C (572 °F) for long durations due to phase imbalances.
- Weldability: While duplex stainless steels offer benefits, controlling the weld procedure is critical for effectively exploiting duplex traits and averting overheating or phase imbalance, which can ruin performance. Qualification expertise is crucial during fabrication.
- Density: Duplex steels are lighter than austenitic steels, which means structural components can be made more efficiently without losing strength.
- Environmental Resistance: Insert other facts about super duplex grades: With an increased concentration of molybdenum, the alloys show enhanced resistance to highly acidic or saline environments.
- Cost of Production: Iterations of stainless steels have a simpler structure. The duplex grades have more advanced alloy compositions, which require more complicated manufacturing processes; thus, the initial cost is higher than for standard stainless steels.
- Environmental Considerations: While resource-intensive during the production phase, duplex steels’ environmental impact improves over time due to their long lifecycle and reduced material consumption.
- Brittle Phase Formation: Improperly processed duplex stainless steels may develop brittle phases, such as sigma phase, which diminishes toughness and increases susceptibility to corrosion.
Reference sources
- Effects of Ag-Rich Nano-Precipitates on 2205 Duplex Stainless Steel:
-
- Key Findings: The study explored the addition of silver to 2205 duplex stainless steel, enhancing its antibacterial properties. Aging treatments at 450°C led to the formation of silver-rich nano-precipitates, which improved antibacterial performance against E. coli and S. aureus. The duplex structure also provided superior corrosion resistance compared to 316 stainless steel.
- Methodology: The research involved microstructural analysis using SEM and TEM, antibacterial testing, and ion release studies to evaluate the effects of silver addition.
- Corrosion of Additively Manufactured Stainless Steels:
- Key Findings: Additively manufactured (AM) 316 stainless steel showed variable corrosion resistance compared to its wrought counterpart. The study highlighted the influence of AM-specific microstructures, such as porosity and substructures, on corrosion behavior. Duplex stainless steel processed via AM exhibited higher corrosion resistance due to its balanced ferrite-austenite structure.
- Methodology: The review synthesized data from various studies, focusing on the impact of AM processes on microstructure and corrosion performance.
- Stainless Steel and Corrosion Overview:
- Key Findings: Duplex stainless steels, with higher chromium and molybdenum content, demonstrated better resistance to pitting and crevice corrosion compared to 316 stainless steel. The study emphasized the importance of alloy composition and environmental factors in determining corrosion resistance.
- Methodology: This comprehensive review analyzed different forms of corrosion, including pitting, crevice, and stress corrosion cracking, across various stainless steel grades.
Frequently Asked Questions (FAQs)
Q: What is the main difference between duplex steel and 316 stainless steel?
A: The main difference lies in their microstructure and properties. Duplex stainless steel contains both ferritic and austenitic phases in roughly equal proportions, giving it higher strength and superior resistance to stress corrosion cracking. 316 ss, on the other hand, is a fully austenitic grade with excellent corrosion resistance, particularly in marine environments. Duplex offers nearly twice the yield strength of 316, while 316 is generally easier to fabricate and has better formability.
Q: How do 304 and 316 stainless steel grades compare to duplex stainless steel?
A: While 304 and 316 are both austenitic stainless steel grades, duplex stainless steel combines properties of both austenitic and ferritic structures. Compared to duplex stainless, both 304 and 316 have lower strength but can be more ductile. 316 contains molybdenum for enhanced corrosion resistance, especially against chlorides, though duplex still outperforms in chloride environments. Duplex generally offers better stress corrosion cracking resistance than both 304 and 316, while 316 typically provides better performance in high-temperature applications than duplex grades.
Q: What applications should I use 316 stainless steel for versus duplex?
A: Use 316 stainless steel for applications requiring good corrosion resistance with moderate strength requirements, such as food processing equipment, pharmaceutical equipment, architectural applications, and chemical processing with moderate temperatures. It’s also preferred when ease of fabrication and formability are important. Choose duplex when higher strength combined with excellent corrosion resistance is needed, such as in offshore oil and gas equipment, desalination plants, pressure vessels, and structural applications where weight savings are important due to its higher strength-to-weight ratio.
Q: How does the cost of duplex stainless steel compare to the cost than 316?
A: Duplex stainless steel typically has a higher initial cost than 316 stainless steel due to its alloying elements (particularly higher chromium, nitrogen, and often molybdenum content). However, the total lifecycle cost may be lower with duplex in certain applications because its higher strength allows for thinner sections and less material overall. Additionally, in highly corrosive environments, duplex may provide longer service life and reduced maintenance costs compared to 316, potentially offsetting the higher initial investment.
Q: What are the key stainless steel grades in the duplex family and how do they compare to 316?
A: Key duplex grades include 2205 (the most common), 2304 (lean duplex), and super duplex grades like 2507. Compared to 316, standard duplex 2205 offers approximately twice the yield strength, better resistance to chloride pitting, and superior stress corrosion cracking resistance. Super duplex grades provide even higher corrosion resistance in extreme environments. 316 is a versatile austenitic grade with good all-around performance, particularly in moderate chemical environments, and is generally more widely available as standard pipe and fittings than specialized duplex grades.
Q: How does fabrication differ between duplex steel and 316 stainless steel?
A: 316 stainless steel is generally easier to fabricate than duplex stainless steel. 316 can be welded using standard austenitic welding procedures, whereas duplex requires more precise heat input control to maintain proper phase balance. Duplex has higher hot working temperatures and greater resistance to distortion during welding due to its lower thermal expansion. 316 offers better cold formability, making it preferable for complex shapes, while duplex contains higher strength that requires more powerful forming equipment. Both can be machined, though duplex’s higher strength often results in increased tool wear compared to 316.
Q: What corrosion resistance properties make duplex or 316 better for specific environments?
A: 316 stainless steel is known for its excellent performance in mild to moderate corrosive environments, particularly where oxidizing acids are present. It contains molybdenum for enhanced pitting resistance, making it suitable for marine exposures. Duplex stainless steel excels in environments with high chloride content, offering superior resistance to chloride pitting, crevice corrosion, and stress corrosion cracking. For seawater applications, duplex is generally superior. In highly oxidizing environments, 316 may perform adequately, while in environments with both chlorides and hydrogen sulfide (sour service), specific duplex grades often outperform 316.
Q: Does duplex stainless steel or 316 have better mechanical properties and strength?
A: Duplex stainless steel significantly outperforms 316 in mechanical properties. Typical duplex grades have yield strength approximately twice that of 316 stainless steel (450-550 MPa vs. 220-290 MPa for 316). This higher strength and resistance allows for thinner wall sections in pressure-containing applications, potentially reducing weight and material costs. The strength of 316 is adequate for many applications but may require thicker sections for equivalent strength. Duplex also typically offers better fatigue resistance and maintains good ductility despite its higher strength, though 316 generally has superior elongation properties.
Q: Which material—duplex stainless steel or 316—is more suitable for high-temperature applications?
A: 316 stainless steel is generally more suitable for high-temperature applications than standard duplex grades. 316 maintains its austenitic structure and properties up to about 800-870°C, while duplex stainless steel has temperature limitations of around 280-325°C for continuous service. At elevated temperatures, duplex can experience embrittlement due to phase transformations. For applications requiring both high temperature resistance and a wide range of applications in corrosive environments, specialized grades like super austenitic stainless steels might be preferred over either standard 316 or duplex grades.