With stainless steel, careful consideration is a requirement. 304 and 316 stainless steels are often compared among the commonly used types. Choosing one that satisfies your intended project or industry could be challenging. Understanding the differences enables you to ensure material selection that integrates durability, corrosion resistance, and cost-effectiveness. This guide highlights 304 and 316 stainless steels and their differences to aid in decision-making. Be it construction, personal endeavors, or manufacturing, this article facilitates an informed material selection.
What is the Difference Between 304 and 316 Stainless Steel?
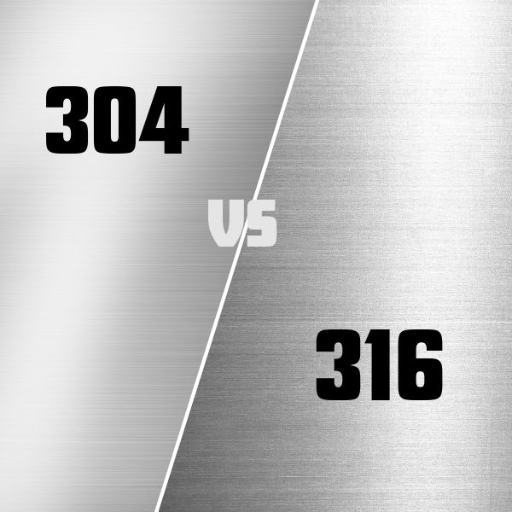
Key Differences Between 304 and 316 Stainless Steel
Their constituents make 304 and 316 stainless steel differ. Both are austenitic stainless steel alloys, and 316 has molybdenum, which 304 lacks. Molybdenum is added to 316 to improve resistance to corrosion, particularly in saltwater or severe chemical environments.
- Corrosion Resistance: 316 stainless steel has greater ability to resist chlorides and acidic environments in comparison to 304 grade.
- Cost: Superior properties of 316 stainless steel make it generally more expensive than other grades.
- Common Uses: 304 grade is most suited for indoor works such as equipment in kitchens and is more common for decorative purposes in comparison to 316 grade, which is more suited for marine environments, chemical processing, and medical equipment.
Selecting between these two options depend on the unique project conditions, particularly the risk of exppsure to corrosive elements.
What are the Chemical Compositions of 304 and 316 Stainless Steel?
The unique characteristics of 304 and 316 stainless steel stem from their different chemical compositions. Listed below is the summary of the main constituents for each grade:
304 Stainless Steel Composition (approximate values):
- Chromium (Cr): 18-20%
- Nickel (Ni): 8-10.5%
- Carbon (C): Max 0.08%
- Manganese (Mn): Max 2%
- Silicon (Si): Max 0.75%
- Phosphorus (P): Max 0.045%
- Sulfur (S): Max 0.03%
- Iron (Fe): Balance
316 Stainless Steel Composition (approximate values):
- Chromium (Cr): 16-18%
- Nickel (Ni): 10-14%
- Molybdenum (Mo): 2-3%
- Carbon (C): Max 0.08%
- Manganese (Mn): Max 2%
- Silicon (Si): Max 0.75%
- Phosphorus (P): Max 0.045%
- Sulfur (S): Max 0.03%
- Iron (Fe): Balance
Molybdenum increases the resistance of 316 stainless steel to corrosion, especially in areas where chlorides are present. This difference makes 316 ideal for marine and chemical processing equipment that is often subjected to harsh environments. 304 stainless steel, on the other hand, is not as resistant to extreme environments; however, it remains highly durable and strong for general-purpose applications.
How Does Molybdenum Affect the Properties of 316 Stainless Steel?
Molybdenum is key in improving the characteristics of 316 stainless steel, particularly its corrosion resistance and durability in aggressive environments. Incorporating 2-3% Molybdenum vastly improves the pitting resistance further, particularly in environments with chlorides or other halide ions. This also improves the ability of the material to withstand crevice corrosion, and thus, it is useful for marine construction, chemical processing, and pharmaceutical construction.
Some data suggests that the addition of molybdenum increases the strength of the alloy at elevated temperature, therefore permitting reliable operation of 316 stainless steel in high-heat applications. For example, the tensile strength of 316 stainless steel at room temperature is usually 515-740 MPa, which is stable over a broad range of temperatures. Furthermore, higher amounts of molybdenum aid in weldability and formability compared to other high-alloy steels.
Moreover, molybdenum increases the likelihood of passive film formation on the surface of the alloy which is critical for corrosion resistance over time. This makes 316 stainless steel highly preferred in the construction of critical infrastructure and instruments that are exposed to extreme conditions while needing long lasting durability.
What Makes 316 Stainless Steel More Corrosion Resistant?
The increased molybdenum content of 316 stainless steel relative to 304 stainless steel is what contributes its greater resistance to corrosive damage. This change increases its resistance to pitting and crevice corrosion in environments rich in chlorides. Furthermore, molybdenum helps passive surface oxide layers form and stablizes them, protecting the material from degradation over time.
How Can I Tell if My Stainless Steel is 304 or 316?
You can consider these methods for differentiating between the 304 and 316 grades of stainless steel:
- Check the Grade Marking – The grade is sometimes marked on the surface of the steel, like “304” or “316”.
- Perform a Chemical Test – Chemical composition testing using a metal testing kit or spectrometer can determine the specific constituents including molybdenum which distinguishes 316 from 304.
- Review Documentation – Assess the material certificate or invoice supplied by the vendor to validate the grade in question.
These are some of the more dependable methods of determining what type of stainless steel you have on hand.
What Are the Physical Characteristics of 304 and 316 Stainless Steel?
304 and 316 stainless steels both belong to the austenitic family, renowned for their versatility, durability, and resistance to corrosion. Regardless, they differ in chemical composition and physical performance, which makes each suitable for a specific application.
304 Stainless Steel Characteristics
- Composition:
-
-
- Composed of approximately 18% chromium along with 8% nickel.
-
Negligible carbon content, typically about 0.08%.
-
- Corrosion Resistance:
-
-
- Provides outstanding wear against oxidative environments.
- Appropriate for indoors or outdoor areas with less intensity.
-
- Strength and Durability:
-
-
- Possesses a tensile strength of approximately 515 MPa (75,000 psi).
- Yield strength usually hovers roughly around 205 MPa (30,000 psi).
-
- Applications:
-
-
- Frequently found in kitchen tools, parts of buildings, and industrial machines.
-
316 Stainless Steel Characteristics
- Composition:
-
-
- Contains 16-18% of chromium, 10-14% of nickel, and 2-3% of Molybdenum.
-
Added resistance to chlorides and severe conditions is provided by molybdenum.
-
- Corrosion Resistance:
-
-
- Resistant against pitting and crevice-type corrosion in saline or marine areas.
-
- Strength and Durability:
-
-
- Possess a tensile strength of roughly 579 MPa (84,000 psi).
-
Exhibit yield strength in the neighborhood of 290 MPa (42,000 psi).
-
- Applications:
-
-
- Used in chemical processing equipment, medical devices, and inshore or underwater constructions.
-
Although both grades have a foundation of exceptional performance, the addition of molybdenum in 316 makes it the superior option in high-exposure situations where chemicals or saltwater are present. This distinction allows users to select the appropriate grade specification to best fit their requirements.
Are There Any Simple Tests to Differentiate Between 304 and 316?
Yes, there are a few simple methods to help differentiate between 304 and 316 stainless steel. One such method is the chemical spot test. Adding specific testing chemicals, such as those containing copper sulfate, can uncover compositional differences because the presence of molybdenum in 316 reacts differently than in 304. Safety needs to be prioritized when conducting such tests.
Another hands-on method is the application of a magnet. Neither of the two grades are significantly magnetic, but 304 exhibits slightly more magnetism after work or forming processes. In contrast, 316 remains almost non-magnetic because of the additional nickel and molybdenum.
Spectrometer analysis also gives an accurate approach. A handheld XRF analyzer can scan the sample and identify its parts precisely. These machines measure the amounts of chromium, nickel, and molybdenum to determine the grade with greater than significant assurance.
These tests offer different levels of sophistication—from basic tactile techniques to advanced technological devices—thereby attending to varying requirements in terms of precision and accessibility.
How Can I Identify Stainless Steel Grades Using a Magnet Test?
The magnet test is a rudimentary, yet efficient technique for the quick identification of some grades of stainless steel. Stainless steel is divided into three families, austenitic, ferritic, and martensitic, based on their crystalline structures, each with different magnetic characteristics. For instance, austenitic 304 and 316 stainless steels are generally non-magnetic in an annealed condition because of their high nickel content. However, if these grades are cold worked, some magnetism may develop.
Ferritic stainless steels, such as grade 430, become magnetic because they do not have enough nickel to inhibit the development of a magnetic structure. Martensitic stainless steels, however, like grade 410, are also magnetic and tend to be harder due to their higher carbon content. A strong attraction to ferritic and martensitic grades will be experienced, while little to no attraction will occur with austenitic grades such as 304 or 316, in their annealed state.
As stated above, magnet tests are quick and easy, giving an idea of what the steel is; however, when determining the grade of steel, tools like XRF analyzers should be used to verify results as the magnet test alone is not conclusive.
What Are the Applications of 304 and 316 Stainless Steel?
Because of their exceptional strength, durability, and resistance to corrosion, we frequently make use of 304 and 316 stainless steel.
- Applications of 304 Stainless Steel: Due to its good resistance to corrosion and for ease of cleaning, this grade is frequently utilized in sinks, utensils, food processing machinery, as well as in kitchen equipment. It also appears in architectural works, automobile components, and chemical containers.
- Applications of 316 Stainless Steel: 316 is most frequently utilized in medical devices, marine equipment, pharmaceutical processing, and chemical storage tanks because of its excellent resistance to corrosion, particularly in salt or marine environments. It is also used in outdoor constructions as well as in industrial applications where strong corrosion takes place.
Where is 304 Stainless Steel Typically Used?
304 stainless steel exhibits some of the highest versatility among stainless steel grades, along with durability and excellent resistance to corrosion. This grade is most frequently used in a wide range of industries, from construction to food processing. In particular, 304 grade is widely used for kitchen equipment, including sinks, countertops, and cookware because it is stain resistant and easy to clean. Its corrosion resistance also makes it suitable to trim architectural paneling and several other outdoor construction work.
Pharmaceutical and medical sectors make the most use of stainless Steel 304 due to its highly sanitary properties. It is common in surgical instruments, medical storage, and sterilization units. Also, 304 is a cost-effective choice for components like freshwater tanks and pipelines. It has other important uses in beauty and strength applications, such as railings, furniture, and automobile trim, which require good appearance and wear resistance. All in all, 304 stainless steel is reliable and versatile for numerous applications due to its exceptional composition and performance.
What Are the Advantages of Using 316 Stainless Steel in Marine Environments?
The prime choice of marine applications is 316 stainless steel due to its unparalleled corrosion resistance, especially in seawater and chloride environments. Being a type of stainless steel, 316 contains 2-3% of molybdenum, which increases its resistance to pitting and crevice saltwater corrosion significantly when compared to 304.
This level of durability ensures long-term operational reliability in the harsh marine environment and reduces the cost of maintenance over time. Studies show that 316 stainless steel maintains its structural integrity for years when constantly exposed to highly saline water. Some of the common marine applications for its strength as well as anti-corrosive properties include boat fittings, deck hardware, seawater piping, and even equipment for desalination.
Its resistance to stress corrosion cracking, which occurs in high chloride environments, also applies to 316 stainless steel. Furthermore, its non-reactive surface enhances its hygienic properties, making it ideal for food processing and storage onboard vessels. Lastly, 316 stainless steel is able to withstand demanding marine conditions while providing excellent mechanical strength and chemical resistance.
How Do 304 and 316 Stainless Steel Compare in Terms of Durability?
Both 304 and 316 stainless steel perform excellently when it comes to durability, however, 316 stainless steel tends to outperform 304 in certain situations. The difference between the two grades is their chemical composition. While 304 stainless steel contains 18% chromium and 8% nickel, 316 stainless steel has about 16% chromium, 10% nickel, and 2% molybdenum. The extra molybdenum in 316 stainless steel is responsible for greater protection against corrosion, especially with chlorides and other industrial chemicals.
304 stainless steel is widely used for various applications and is valued for its strength, but it comes with its disadvantages. It is highly resistant to rust but much weaker against pitting and crevice corrosion. Chloride environments, such as coastal regions or extreme industrial settings, pose a threat to 304 stainless steel. For marine environments, chemical processing, or regions with high salinity, 316 stainless steel excels. 316 stainless steel has shown impressive resistance to pitting and crevice corrosion, so it is the preferred choice in these environments.
Research and industry reports indicate that 316 stainless steel withstands more extreme conditions and longer corrosive exposure without considerable deterioration, ensuring reduced upkeep and an extended life span over time. While both grades are equally proficient in maintaining structural strength, the more refined makeup of 316 achieves exceptional performance in demanding applications requiring enduring strength under extremely harsh conditions.
What Are the Costs Associated with 304 and 316 Stainless Steel?
The pricing of 304 and 316 stainless steels fluctuates according to the market; however, it is evident that 316 is usually pricier than 304. This is primarily due to 316’s higher nickel and molybdenum content, which further increases its corrosion resistance as well as durability. If the application does not involve highly corrosive environments, it is logical to say that 304 stainless steel is the most financially sensible option if budget constraints are a key concern. On the other hand, projects that require enduring resistance to harsh conditions will benefit from the long-term investment value of 316 stainless steel.
Why is 316 Stainless Steel More Expensive than 304?
The more advanced 316 stainless steel surely is more expensive than 304 stainless steel, because 316 has a more advanced chemical composition. The presence of molybdenum, which is present in 316 stainless steel in 2-3% is an important factor. Molybdenum protects the material 316 steel from pitting and crevice corrosion, which is prevalent in many marine and chemical environments. Molybdenum is expensive and rare, which makes the production of 316 stainless steel cost more.
In addition, stainless steel 316 also usually has higher amounts of nickel in the range of 10-14% compared to type 304, which has 8-10.5%. Molybdenum in stainless steel amplifies its strength as well as ductility; however, because nickel is a raw material that is rare and depends on global market conditions, it adds to the expense.
The production processes and the demand for the material influence the price, differing from the value of 304. The manufacturing of 316 stainless steel requires high-quality standards to be maintained during the production process because the steel is made for use in extreme environments. The wide use of this steel in aerospace, construction of medical devices, and fabrication of marine vessels also adds to its demand in the market, which in turn increases its cost.
Finally, 316 stainless steel’s long durability and lifespan make it a long-term investment in spite of its initial higher price. Employing 316 in harsh settings critical for structural strength and corrosion resistance can lower overall expenditure for maintenance and replacements, thus offsetting the initial investment.
How Do the Costs of 304 and 316 Affect Their Selection for Projects?
Cost considerations are crucial when deciding whether to go with 304 or 316 stainless steel for a project. Due to the greater amount of molybdenum in 316’s composition, its price is usually 20-30% higher than 304. For example, due to the volatility of the market, the costs of raw materials, and the region, most recent industry reports suggest that stainless steel prices are 304 generally dominated the industry as the cheaper option where moderate corrosion resistance was required.
Projects that do not anticipate regions with coastal or industrial corrosive environments, which are classified as highly corrosive, may leverage 304’s cheaper price tag, especially in large-scale projects where material spend adds up quickly. Projects set in marine environments, chemical handling, or areas with high chloride concentrations tend to prefer 316 due to its long-term cost-saving benefits, despite the high cost of repair and replacement caused by corrosion over time. So, one tends to find in practice that the trade-off between material cost and maintenance cost over the project’s lifecycle drives the decision.
Also, data shows that 316 stainless steel is being adopted more widely by industries such as construction, food processing, and medical device manufacturing because of its durability and hygienic properties, even though it is more expensive. The specific conditions of the project: environmental exposure, budget limits, and the expected lifespan, dictate picking the final material most directly.
Are There Cost-Effective Alternatives to 304 and 316 Stainless Steel?
Absolutely, more affordable options than 304 and 316 stainless steel exist. For properties where more resistance to corrosion is not a necessity, 201 stainless steel or galvanized steel can be used. Certain types of duplex stainless steels have a good balance of strength and corrosion resistance while being more economical in certain environments. As always, the driving factors such as atmospheric conditions, environmental impact, mechanical requirements, and budget make the primary decision.
How Does Welding Affect 304 and 316 Stainless Steel?
Both 304 and 316 stainless steel can suffer from welding, as it may change their microstructure and corrosion resistance. Welding induces heat, which may trigger a process known as sensitization–the formation of chromium carbides along the grain boundaries, which reduces the corrosion-resistant property within those areas. This tends to be a greater issue for 304 stainless steel compared to 316 due to 316’s molybdenum addition, which enhances resistance to these issues. To avoid this problem, low-carbon versions such as 304L and 316L are often used because they limit the amount of sensitization associated with welding. Effective post-weld treatments, like annealing or passivation, can further restore corrosion resistance.
What Are the Best Practices for Welding 304 Stainless Steel?
Like with other types of metals, welding 304 stainless steel needs careful handling with regard to pre- and post-welding procedures because the corrosion resistance characteristics and the mechanical properties of the material must be preserved. Here are some of the main points to consider as best practices:
- Use Low-Carbon Filler Materials: It is advised that welders utilize low-carbon fillers, for example, 308L or 304L stainless steel, in order to mitigate the chances of carbide precipitation and sensitization. These alloys are beneficial because they do not increase the risk of intergranular corrosion in the heat affected zone (HAZ) undermined.
- Maintain Proper Heat Input: C Controlling heat input per each individual weld pass is equally as critical as maintaining the proper operational parameters. Too much heat may cause distortion or microstructural changes while insufficient heating may result in weak or inconsistent welds. Adequate heat application coupled with a relaxation period between weld passes aids in cooling, which alleviates these concerns.
- Shielding Gas Selection: Inert gases such as argon or argon-helium mixtures must be used because they are critical for shielding the weld zone from atmospheric contamination, which would lower the quality of welds by oxidizing and creating porosity.
- Pre-Weld and Post-Weld Cleaning: The base material and the filler rod to be used need to be cleaned before welding to remove oils, dirt, and other contaminants that will degrade the weld integrity. Pickling or Electrochemical cleaning aids in restoring the material’s corrosion-resistant surface dulled by discoloration and oxides.
- Use Proper Welding Techniques: Welding techniques like TIG (Tungsten Inert Gas) and MIG (Metal Inert Gas) are highly valued for their accuracy when working with stainless steel. TIG welding is especially helpful for thin parts because of its good heat control.
- Avoid Overheating During the Weld Process: Keeping interpass temperatures below 350°F (175°C) can help prevent carbide precipitation and distortion. Adequate checks with measuring devices can ascertain that this limit is not crossed.
- Post-Weld Heat Treatment: If required, annealing or other heat treatments can be performed to change the microstructure and further minimize sensitization risk. This step is important for applications involving severe service conditions or chloride exposure.
Following these best practices allows welders to obtain robust corrosion resistant welds and simultaneously maintain the mechanical strength and service life of 304 stainless steel frameworks.
Can You Weld 316 Stainless Steel Using the Same Techniques as 304?
Even though 316 stainless steel and 304 stainless steel have some similarities concerning composition and weldability, some differences exist that require changes in the welding procedures. Both alloys are types of austenitic steels, which are widely used due to their resistance to corrosion and longevity. 316 stainless steel, however, has greater resistance to pitting and crevice corrosion, especially in chloride-rich environments, due to the higher molybdenum content. This also makes it somewhat more susceptible to hot cracking during welding as compared to 304.
For 316 stainless steel, welders have to pay special attention to the type of filler metals that are used. Low-carbon or stabilized filler metals are preferred, like 316L, because they minimize the likelihood of carbide precipitation and intergranular corrosion. For both alloys, preheating isn’t usually done, but controlling the heat input is crucial, especially for thicker sections. Because too much heat can alter the microstructure and diminish corrosion resistance, post-weld heat treatment can prove advantageous for high-stress applications to guarantee microstructural stability.
The research shows that for GTAW or GMAW of both 304 and 316 stainless steel, shielding gasses like argon with small proportions of helium or carbon dioxide are frequently used in order to maintain arc stability and protect the weld pool. Both types of welding are widely practiced for 316 stainless steel, but there are specific considerations that need to be addressed in order to get the best outcome.
What Are the Post-Weld Treatments for 304 and 316 Stainless Steel?
Post-weld treatments are vital for ensuring longevity and corrosion resistance of stainless steels 304 and 316. Enhancing the characteristics of welded material is achieved through treatments such as pickling, passivation, and stress relieving which aids in optimal performance.
Pickling encompasses the removal of oxide scales and discoloration from welding through the use of acid solutions containing nitric and hydrofluoric acid. This becomes increasingly relevant with 316 stainless steel as it is frequently used in more corrosive settings such as marine and chemical processing. Careful surface preparation is essential to make certain that the chromiu oxide layer is not damaged.
Passivation utilizes nitric or citirc acid solutions after pickling to scrub the surface of the metal to encourage the developement of a consistent passive layer rich in chromium. With 304 stainless steel, passivation strongly impacts its resistance to elements while 316 is further aided by the content of molybdenum as it greatly improves protection.
Stress relieving is performed between 800°F and 1600°F (425°C and 870°C) and is one of the crucial remaining threads to aid in reducing residual stresses formed from welding. Decreased residual stress improves the risk of warping and increases corrosion resistance. This is extremely useful in harsh environments where 316 stainless steel is exposed to aggressive substances.
Following these post-welding processes guarantees that both grades retain their structural integrity and optimal performance for a variety of demanding applications.
Reference Sources
-
Networking the Cloud:
- Key Findings: This study discusses the evolution of data center networks, emphasizing the importance of agility and scalability. It highlights the use of SFP+ 10G ports for efficient data transmission and cost-effective networking solutions. The research also explores the challenges of VLANs, traffic engineering, and the need for high bisection bandwidth in modern data centers.
- Methodologies: The study uses real-world data center traffic patterns and simulations to propose a scalable network design (VL2) that ensures high throughput and performance isolation.
-
TWDM PONs with WDM Overlay for Converged Broadband Services:
- Key Findings: This paper focuses on the integration of SFP+ modules in optical network units (ONUs) for cost-effective broadband services. It explores the potential of tunable transceivers and wavelength-division multiplexing (WDM) technologies to enhance network flexibility and efficiency.
- Methodologies: The research employs experimental setups to test the performance of SFP+ modules in various network configurations, analyzing their impact on cost and service quality.
Frequently Asked Questions (FAQs)
Q: What’s the difference between 304 and 316 stainless steel?
A: The main difference between 304 and 316 stainless steel is the presence of molybdenum in 316 stainless steel, which enhances its resistance to corrosion, especially against chlorides. This makes 316 stainless steel a better choice for marine applications.
Q: How can I tell the difference between type 304 and type 316 stainless steel?
A: You can tell the difference by examining the surface of the steel or conducting a chemical test. Type 316 contains molybdenum, which contributes to its corrosion resistance, while type 304 does not.
Q: Is 316 stainless steel more expensive than 304 stainless steel?
A: Yes, 316 stainless steel is generally more expensive than 304 stainless steel due to its higher corrosion resistance and the addition of molybdenum in its composition.
Q: What applications are best suited for 304 vs 316 stainless steel?
A: 304 SS is commonly used in food processing equipment, kitchen appliances, and general structural applications. In contrast, 316 SS is preferred for marine environments and chemical processing due to its superior corrosion resistance.
Q: What grade of stainless steel is suitable for high-temperature applications?
A: Both 304 and 316 grades can withstand high temperatures, but 316 stainless steel offers better high-temperature strength and resistance to scaling, making it a better choice for extreme environments.
Q: How do the strength and hardness compare between 304 and 316 stainless steel?
A: The strength and hardness of 304 and 316 stainless steels are similar, but 316 stainless steel may offer slightly better performance in harsh environments due to its alloying elements.
Q: Can I use 304 SS in a marine environment?
A: While 304 SS can be used in marine environments, it is not recommended due to its lower resistance to corrosion compared to 316 SS, which is specifically designed for such applications.
Q: What factors should I consider when choosing between 304 vs 316 stainless steel?
A: Consider the environment in which the stainless steel will be used, the potential for exposure to corrosive elements, the required strength, and the cost. For marine and corrosive environments, 316 is the right grade, while 304 is suitable for less demanding applications.
Q: What are the different grades of stainless steel available?
A: There are several grades of stainless steel, including 304 grade, 316 grade, and others such as 430 and 2205. Each grade has specific properties that make it suitable for various applications, depending on factors like corrosion resistance and strength.