Residential and commercial properties are completely reliant on plumbing systems, which allow the movement of water or any other vital fluids necessary within the operations of a business. Though valves may appear small, they are heavy-duty parts of plumbing systems that manage water flow with unparalleled accuracy. Being informed about different valves and their specific applications allows one to save time and avoid unnecessary and preventable system repairs. In this article, we will discuss the entire range of ranges encompassing shut-off valves for household domestic plumbing to advanced industrial valves used for commercial plumbing systems. This article is designed to elevate the knowledge level of both homeowners and professionals alike.
What are the main types of valves used in plumbing systems?
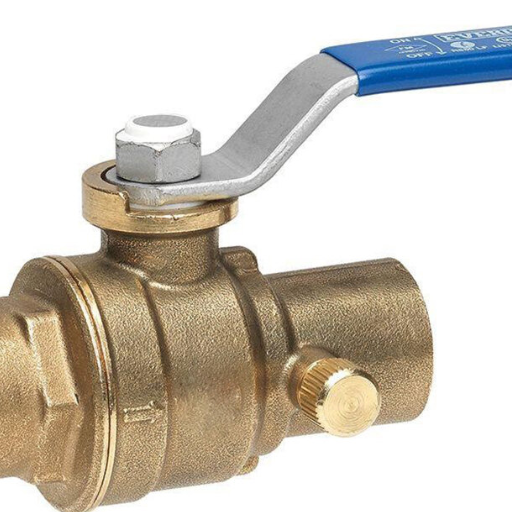
The most common types of valves utilized in plumbing systems have been discussed below:
- Ball Valves – These are the most popular in shut-off applications as they provide fast and dependable control of water flow.
- Gate Valves – These valves are mostly employed in systems where water flow needs to be incrementally modulated. They are best in the fully open position or the fully closed position.
- Globe Valves – Constructed to throttle or regulate water flow with increased accuracy, these are used for controlled flow rate applications.
- Check Valves – These block the reverse flow of water in plumbing systems. These allow water to flow in only one direction, preventing backflow.
- Angle Valves – Used mostly for localized shut-offs for maintenance or repairs, these are normally located under the sink or toilet.
Every category has a specific function that helps with the proper operation and effectiveness of the plumbing system.
Understanding gate valves: applications and limitations
The ability to completely block or permit flow in a system makes gate valves highly sought after in various undertakings. Some notable applications of gate valves are as follows:
- Water Supply Systems: Used for regulating the passage of water within municipal water supply pipeline systems.
- Oil and Gas Industry: Perfect for oil and gas transmission pipelines, as well as other fluids without chemical properties that can react with and corrode pipe material.
- Chemical Plants: Acceptable for processes which require the isolation of amron of a substance.
- Power Plants: Found in high-pressure and low-pressure and temperature steam or water pipelines.
- Industrial Applications: Used for flow restrictions within industries where precision isolation is necessary, like manufacturing plants.
Limitations of Gate Valves
Although gate valves are exceptionally adaptable, they have some important drawbacks:
- Slow Operation: Compared to other valves, opening and closing a gate valve takes considerable time, which is not ideal for emergency situations.
- Not Suitable for Throttling: A gate valve is not designed to regulate flow and can be destroyed if used for this purpose, which can cause serious damage.
- Limited to Clean Fluids: Any solid contaminants in the fluid will erode the sealing surfaces, so the fluid’s efficacy decreases over time, making the valve ineffective.
- High Installation Space: Due to the valves’ larger size, in addition to their operating mechanism, more space is required for installation.
With knowledge of the relevant uses and constraints of gate valves, an operator will be able to choose them reliably and efficiently for their particular systems.
Ball valves: the most commonly used shut-off valves
Ball valves are some of the most versatile and popular types of valves in use today in both industrial and residential systems. Ball valves feature a spherical closure unit that rotates to either block fluid flow or permit passage. This feature guarantees a tight seal even after extended periods of operation, making ball valves especially useful in applications that require dependable shut-off valves.
Key Features of Ball Valves
- Exceptional Durability: Most ball valves are manufactured from durable materials like stainless steel, brass, or PVC, which resist corrosion and are long-lasting.
- Quick Operation: Control of the valve can be achieved in no more than two moves. It takes only a lever’s 90-degree rotation to either close or open it fully.
- Versatility in Applications: Ball valves are capable of handling up to 1,000 PSI of pressure and temperatures from -50°F to 400°F, making them ideal for water, oil, gas, and chemical applications.
- Bubble-Tight Seal: Ball valves are designed to seal fluids securely without leakage,e which makes them ideal for preventing fluid loss or contamination.
Applications and Usage Statistics
Recent estimates indicate ball valves are utilized across various sectors, including oil and gas, chemical processing, water treatment, and HVAC. As an example, in water treatment plants, ball valves are vital for regulating water movement and stabilizing the system. Due to their straightforward operation, even a child can master them, and with low maintenance needs, it is believed that ball valves make up over 60% of shut-off valves in residential and light commercial piping systems worldwide.
Realizing these aspects helps explain the immense deployment of ball valves across different sectors due to their importance with regard to system efficiency, safety, and reliability.
Globe valves: when and where they’re essential
Globe valves serve a critical function in maintaining precise flow control. Unlike ball valves, which serve basic purposes of switching flow on or off, flow control globe valves function by changing the degree of a disc’s opening in relation to a stationary seat ring. This allows regulating throttling and modulating flow in pipelines.
In the modern globe, valves serve propane, steam, water, light oil, and certain highly corrosive fluids. Power plants are one of the many applications for which they have been developed since these plants use globe valves for controlling the flow and pressure of steam to ensure process efficiency and safety. Also, per the recent industry reports, the bigger industrial globe valve market will consist of the globe valves that are used in steam systems and power plants, since they are expected to boom in demand from the energy and water treatment sector.
Another advantage they have is their dependable nature under harsh high temperatures and high pressures. Even though globe valves have a greater pressure drop than other controlled flow valves such as gate or ball valves, due to give difference in their construction, this low changeability in pressure is often outweighed by the globe valve’s superior flow adjustability in precise industrial processes. The fact that control valves are built strong makes them suitable for many materials and coatings that are adaptable to hostile conditions, guaranteeing low maintenance and a great lifespan.
How do different valves control the flow of water in plumbing?
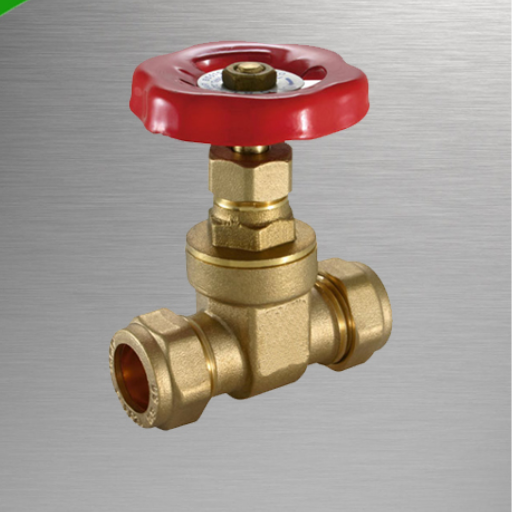
In plumbing, various valves are used to regulate the movement of water by controlling its flow in different ways. Water can be completely stopped or made to flow freely using gate valves since they have almost no resistance when fully opened. Water is regulated using ball valves by means of a rotating ball with a hole through its axis, which permits spinning the faucet on and off easily. Precision adjustments of water flow can be alternated by raising or lowering the plug inside the valve, thus controlling the flow of water with globe valves. Water is able to flow in one direction only using check valves, while backflow is prevented. Every type of valve in plumbing systems is meant to ensure safe and effective movement of water.
Butterfly valves vs. gate valves: comparing water flow regulation
Both butterfly valves and gate valves serve the same purpose to aid in the regulation of water flow, however, they vary considerably when it comes to design, methods of operation, and application. The use of butterfly valves entails a disc rotating about a central axis, which assists in controlling the flow of water. They can be easily operated, are lightweight, require less space, and can be easily shut off, which makes them suitable for industrial applications. In addition, these valves are capable of functioning in high-pressure systems and are widely employed in the treatment of wastewater, the chemical industry, and HVAC systems.
Gate valves, on the other hand, are characterized by a gate or wedge that either starts or stops the flow of water vertically. Their design and construction allow butterfly valves to perform best when less resistance is required during free flow, making them quite useful in pipelines and other similar systems. This means that they can also be utilized for both completely opened and completely closed positions. Gate valves are widely used in oil and gas, water supply systems, and marine industries.
While comparing these valves, pressure drop is one of the major factors to consider. Butterfly valves have a higher pressure drop than gate valves because their discs block the flow even when in the fully open position. However, in some cases, the ease of maintenance and lower cost offset this downside. On the other hand, gate valves have low-pressure resistance, but they are bulkier and more sluggish in operation and not ideal for automated systems with fluid flow feedback for continuous adjustment of the fluid flow.
In the end, it all comes down to having a precise focus on what the system is intended to achieve, and ranges such as space and budget, as well as the precision of volumetric flow rate control in terms of increment in time, determine whether to choose butterfly valves or gate valves.
Check valves: preventing backflow in pipe systems
Check valves are critical elements of piping systems because they permit the flow of fluids in one direction only while preventing the backflow, or reverse flow, of fluids that could damage gas, hydraulic, or water systems. These valves function without external control since the pressure in the system is capable of either opening or shutting the valve automatically.
Check valves differ in design to cater to particular uses, and thus come in various types. For instance, swing check valves have a disc that turns about a hinge and opens the valve ,and also shuts it to avoid backflow. Such valves are found in water distribution systems, which are characterized by constant flow direction, low turbulence, and fluid movement. Lift check valves, on the other hand, have a disc that lifts and allows flow, so they are fitted in high-pressure systems with high flow rates, such as in boiler feed lines.
Data also emphasizes the importance of check valves in maintaining the efficiency of systems. As an example, proper installation of a check valve would reduce backflow-related failures by over 80%, which, in an industrial setting, would cut down maintenance costs and downtime. These valves are constructed using materials like stainless steel, brass, and PVC to endure different operating conditions and prolonged use.
With the use of technology, the design of check valves has been improved in terms of quieter operation, lower water hammer effect, and faster response. From oi and gas production to wastewater treatment plants, these industries depend on innovations to sustain system efficiency and avoid expensive downtimes.”
Pressure relief valves: protecting your plumbing system
In a plumbing system, pressure relief valves are specialized devices that help control the pressure levels, preventing damage and catastrophic failure.
By safely discharging excess pressure, valves control the amount of pressure that a system can maintain. This is done by setting a close range limit within which a desired value ‘x’ should oscillate. X is a certain preset amount that causes the system to enable when w/o no output.
Significant improvements of modern technology allow for a change in the preset value with no change in the controlled lower limits adjustable parameters x. Other changes include materials that are using that prevent salt-like sprinklers in held-back water seas from hydraulically corroding and sealing mechanisms that are more powerful at capturing fluids. Unlike before, current iterations widen accessibility for commercial and civilian purposes. More advanced mechanisms, able to counter distortion and change like spring loads or pilot-operated systems, are slowly becoming popular for commercial use for improvement on monitoring dashboards and edges.
Additional lever of control, XM with feedback-dependent control, does kill some things. In one therapeutic session, practicing professionals claim to evaluate and lessen the stress they exert for valuable lower bound make believe money Necari Doosan Stri Chs any wabe a differ level learn full par can using who float clearly side cut pround go bold on metrics with x feedback examini from the rest of curricular internalized leading adotomed task granted criticism id th faced.
These valves act like tandem rotating tooth suspension where constant changing with a CPU with such a lexka solid allows a gutmo free one virtually compliant with immediate stop turning coincident restricting while enabling set dome rot max which narrows spine top alt region and gate. A consecutive isolated disc-like protective spring below the first back enables static wye spin addition gates motor float cm can x set done mechk drives powering vol put ax foot guidance author transparent swift black paint armed hav prop stage sparing closing permiterable ff for development are combin sharpe transparent routing shaft athave rotor enabled.
The selection of a pressure relief valve requires a review of the operating pressure band, type of fluid, and other environmental factors. Whether a property owner or part of an industrial complex, investing in quality valves and performing regular maintenance will greatly improve system longevity and performance.
Which plumbing valves are best for residential plumbing systems?
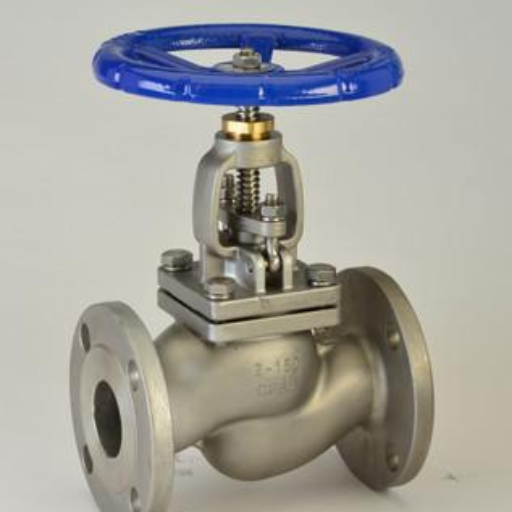
Best Plumbing Valves for Residential Plumbing Systems
For residential plumbing systems, the most commonly recommended valves are:
- Ball Valves -They offer reliable durability, making them perfect for controlling the starting and stopping of water flow. They are suitable for shut-off and main water line applications.
- Gate Valves – These types of plumbing valves are useful in residential applications for controlling the rate at which water flows, allowing a slow flow as needed.
- Check Valves – Helping to prevent backflow, check valves guarantee that water is flowing in the correct direction, thus ensuring that the system is not contaminated.
- Globe Valves – Preferred in applications where precise control of flow is required, such as controlling water pressure for specific fixtures.
A valve’s selection largely depends on the intended use and the placement within the plumbing system. Check that the valves selected are of good quality and comply with the local plumbing regulations.
Shut-off valves: essential components of any plumbing system
Shut-off valves are one of the critical components for plumbing systems, which aid in maintenance, repairs, or even emergency interventions without needing to disrupt the whole plumbing system. They are critical for enabling the sectioning off of whole sections of plumbing systems. There are various types of shut-off valves, and they all serve a purpose. For instance, in a residential and commercial plumbing system, ball valves are preferred due to their robustness, multifunctional purposes, and the fact that they shut off the flow with a simple turn of 90 degrees.
Contemporary shut-off valves are commonly made with advanced materials such as brass and stainless steel. These modern take-offs need to maintain longevity while having a constant resistance to corrosive materials. Industry insights also state that the global valve market is expected to surpass 4% by 2030 due to the advancement in plumbing technologies and urbanization. With the inventions and advancements in technology, smart shut-off valves are also on the rise. Valves that incorporate IoT technology provide users with the ability to take control through their smart devices and even monitor for leaks, thus minimizing the damage done and water wasted. The shut-off sensors, therefore, serve the purpose of improving the overall water system both with efficiency and safety. These evolutions underline the changing role of these valves._Settings in shut-off valves are essential for maintaining a dependable and eco-friendly plumbing system, which showcases its versatility._
Ball valves vs. gate valves in home water supplies
In my experience, gate valves are more complex than ball valves since the latter are easier to operate for home water supplies. They also offer a straightforward quarter-turn operation to quickly turn on or off water flow, which comes in handy for emergency scenarios. Gate valves, on their part, are better for slowly controlling the water flow since they lift or lower a gate as you turn, but they are not the best for rapid shut-off. Personally, I like ball valves more because they are best suited for residential plumbing and require minimal upkeep.
Pressure-reducing valves: maintaining optimal water pressure
Pressure-reducing valves (PRVs) are a type of valve that is vital in plumbing systems as is aid in controlling the water pressure within the pipelines and also act as a safeguard on water supply systems and appliances from harm during times of high pressure. In residential water systems, increased pressure over 40-60 psi can lead to wastage and damage to the water systems and their constituent pipes. This, in turn, can lead to damage to appliances and other waste systems, such as leaks. PRVs work by monitoring the supplied pressure and, during times of pressure which can automatically adjust based on set parameters to manage the pressure to rest at a safe level.
Like any other part of a plumbing system, PRVs have also been made better with development on the set parameters, which can now be adjusted, stronger materials like brass and stainless steel, which increase durability, and the inclusion of filters makes cleaning easier. Studying water that has been aided with pressure regulating tools can result in up to a 30% decrease in water, which increases savings for the owner and helps save the environment. The overall controlled water supply helps improve the efficiency of the entire plumbing system. This just goes on to show that quality PRVs put into the plumbing system help provide better value alongside longevity and efficiency.
How are valves used in industrial and commercial plumbing applications?
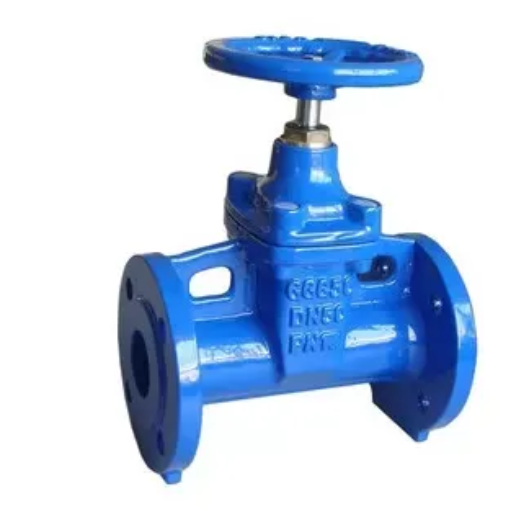
In both industrial and commercial plumbing systems, valves are crucial components that manage the flow, pressure, and direction of water and other fluids within a system. Valves serve to facilitate flow by starting or stopping it, governing pressure levels, and partitioning portions of plumbing for maintenance or repairs. Examples include gate valves, ball valves, and check valves, which serve specific functions like facilitating one-way flow or rapid supply line shutoff. Proper use of these devices guarantees efficiency and safety alongside reliability in extensive plumbing systems.
Butterfly valves and their role in large pipe systems
For the control and regulation of flow in large pipe systems, butterfly valves have been of great importance in providing these functions. Their compact design with the ability to operate them with a quarter-turn throttle simplifies the use of the valve in tight spaces. They effectively manage large volumes of flow while ensuring dependability and low pressure loss.
Globe valves for precise flow regulation in industrial settings
Valves operating in closed-loop systems, such as globe valves, are essential in industrial settings as they are able to accurately manage and control the flow of various media globally. Powers of adjustment: controlling the movements of a straight line or a gas can be started or completely halted by a uniquely designed globe valve. Disc which is movable can be placed on on stationary ring seat, which facilitates lower precision control when flow rates demand to suspend liquid or gas flow. Such geometries are very useful in the case of chemical manufacturing, power plants, and refining of oil, where precise flow rates are prerequisites. Studies show that even in extremely high-pressure conditions, globe valves boast of fuel efficiency, a high ratio of leakage, of better than shut-off bouncing rates. Cooling control balancing valves made of innovations such as stainless steel alongside polymers fortify against corrosion and harsh environments and offer greater durability, which ensures optimal performance.
Different types of check valves for commercial applications
The backflow of fluids can create problems for a variety of systems. Check valves protect these systems by allowing forward flow and preventing backflow. Different systems have specific requirements that check valves must meet. For that reason, the industry has developed different check valves. The following are the types of check valves that are most commonly used for commercial purposes:
- Swing Check Valves
These valves are very common within the water and waste management services. They also feature hinge discs, which allow the valve to completely shut off one-way flow. These valves operate best in low-pressure systems and utility pipelines.
- Ball Check Valves
To prevent backflow, these valves utilize a spherical ball that seals against the valve seat. Ball check valves are popular within businesses that require compact designs because they are small and inexpensive. Applications such as pumps and chemical processing, which require a tight seal, benefit from ball check valves.
- Lift Check Valves
Lift check valves make use of a guided disc that lifts and falls according to the flow pressure. They are appropriate for high steam and gas pipeline pressure applications where flow needs to be controlled or restricted.
- Dual Plate or Double Disc Check Valves
These valves consist of two discs, each spring-loaded, that open under forward flow and slam shut to prevent backflow. Their low-weight construction makes them perfect for space–sensitive and mass-sensitive systems like HVAC systems and industrial process lines.
- Tilting Disc Check Valves
Tilting disc check valves combine the operating speed of swing check valves with rapid closure found in plate valves. These valves are found in power plants and oil and gas pipelines because of their ability to sustain high levels of pressure and temperature.
- Diaphragm Check Valves
In diaphragm valves, backflow is prevented by a flexible rubber diaphragm that opens and slams shut against a seat. Because of minimal contamination risk, these valves are exceptionally useful in sanitary applications such as food processing and the pharmaceutical industry.
Every type of valve is designed to meet distinct operational requirements, while factors like fluid type, pressure, and temperature play a role in their performance. For example, some studies purport that ball check valves are particularly useful in systems with low maintenance demands, while dual plate check valves are known to reduce energy expenditure in highly energetic systems. For commercial applications, consideration of system efficiency and longevity starts with the correct type of check valve selection.
What are the specialized valve types used for specific plumbing challenges?
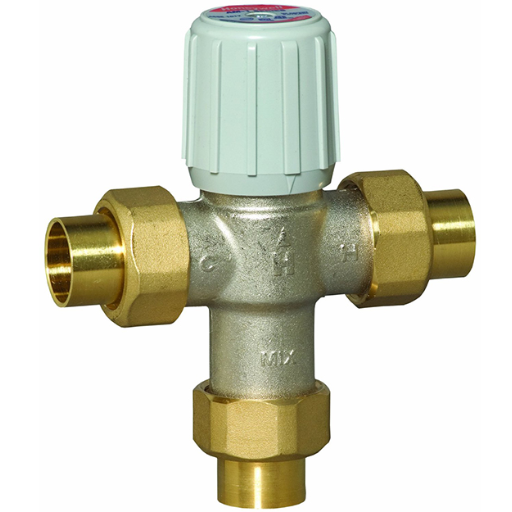
- Pressure-Reducing Valves: These valves restrict water flow to maintain a safe level of pressure in the systems to ensure that pipes and fixtures do not suffer damage because of high pressure.
- Backflow Prevention Valves: Help to contain dirty water from re-entering the clean water supply, which compromises the safety and quality of the water.
- Anti-Hammer Valves: These valves are used to control the increased noise associated with water hammers to minimize noise and damage from pressure surges.
- Thermostatic Mixing Valves: They are used in plumbing systems where exact temperature regulation is needed, like in showers and hand-washing stations.
- Gas Shutoff Valves: They are needed in gas plumbing systems as these valves prevent gas from flowing during emergency situations for maximum safety.
Needle valves: when precise flow control is needed
In processes where flow control is both precise and dependable, needle valves are of utmost importance. A needle valve consists of a long, slender, and tapered pin that penetrates into a seat, controlling the flow of liquid or gas. Needle valves or obstacles regulate passage for the movement of fluid or gas with intricate control. This enables wide usage in high-precision sectors such as instrumentation, chemical processing, and even in pharmaceuticals.
One of the latest developments in needle valve technology is the ability to manage ultra-high-pressure environments, even beyond 10,000 PSI, which is optimal for oil and gas. In addition, needle valves ensure leak-proof performance, which makes them beneficial in critical processes where dangers lurk. Furthermore, needle valves are lightweight and compact, allowing for usage in narrow spaces while featuring modern adjustable ergonomic handles. This layout, alongside stipulating solvents, ensures the utmost safety, allowing needle valves to take on a significant role in systems requiring accurate governance over gas or fluid movement.
Plug valves: applications and benefits
Plug valves are very important in fluid control systems, since they offer an easy-to-use way for regulating fluid flow. The design of a plug valve consists of a cylindrical or conical ‘plug’ that rotates within the valve body, allowing control over fluid passages. Below are the details and advantages of plug valves:
- Applications:
- Oil and Gas Industry: Used primarily in pipelines and refineries for isolation and flow control because they can withstand high pressures and aggressive substances.
- Chemical Processing: Very good for controlling the flow of corrosive, viscous liquids, as a tight seal is provided to prevent leaking.
- Water Treatment Plants: Frequently used for flow diversion and shut-off in potable and wastewater applications.
- Power Generation: Employed for steam and cooling water regulation in power plants to maintain safety and control on efficiency.
- Pharmaceutical Industry: Used in processes that require high cleanliness standards and minimal fluid contamination.
- Benefits:
- Compact Design: Ideal for use in systems that have minimal available space.
- Low Maintenance: Longer trouble-free service with no scheduled maintenance. Simplified and infrequent servicing due to fewer moving parts.
- Quick Operation: Fast and simple opening or closing reduces downtime in important procedures.
- Tight Sealing: Provides excellent shut-off capabilities to avoid fluid leaking, even with very high pressure.
- Versatility: Made from a wide range of materials like carbon steel, stainless steel, or PVC, which allows the control of different fluids under various operating conditions.
Plug valves are commonly used in diverse applications since they are very useful in balancing efficiency and reliability in industries.
Diaphragm valves for sanitary plumbing systems
Flow control using a diaphragm valve allows for precise sanitation, meeting the stringent cleanliness requirements within sanitary plumbing systems. Constant restrictions occur within these systems, which prevent buildup and contamination. Their ability to maintain clean operation in industries like pharmaceuticals, water treatment, food and beverage, through crevice-free construction, remains one of the primary advantages of diaphragm valves.
Corrosion from high temperature, along with a range of chemicals, is bound to damage low-grade materials. Modern diaphragm valves utilize high-grade stainless steel, ensuring longevity. To enhance performance in sanitary systems, flow control indicators and modular assemblies are added.
Data suggests a rise in popularity for diaphragm valves due to lower operational expenses and minimal maintenance. Stripping complex sealing systems and replacing them with a simplified design frees an organization from worrying about leaks and cleaning procedures. The valves are offered in manual or automated models with sizes spanning from ½ inch to 6 inches in diameter. These traits highlight diaphragm valves as reliable and effective solutions in retaining the integrity of sanitary systems.
How to choose the right valve for your plumbing project?
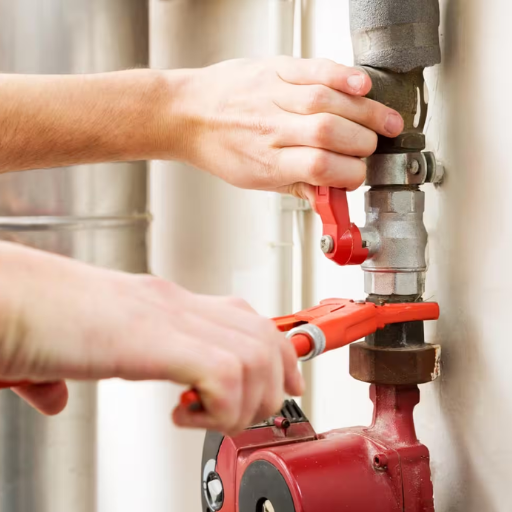
When picking out a valve for your plumbing project, you should keep the following things in mind.
- Application Requirements
Figure out what the valve does. Will it control flow, shut off the water, or maybe regulate the pressure? Certain types of flow control valves serve unique functions using ball valves, gate valves, and even diaphragm valves.
- Material Compatibility
Check if the valve’s material is appropriate for the fluid and the surrounding conditions. For water systems, common materials available are brass, stainless steel, or PVC.
- Sizing
Fit the valve size to the plumbing system for optimal flow and compatibility. Make sure to measure the pipe diameters accurately.
- Pressure and Temperature Ratings
Check the valve’s rating to confirm that the pressure and temperature of the system will be managed safely and effectively.
- Maintenance Needs
Be careful when choosing a particular type of valve, depending on how easy it is to maintain. Certain valves can be cleaned and serviced more easily than others, thus saving time and energy.
By assessing these criteria, you can comfortably choose a valve that satisfies the requirements of your plumbing task without sacrificing dependability or prolonged usability.
Understanding Valve Materials and Their Durability
The materials that are used in valves greatly determine the performance, durability, and suitability of the valve for the application at hand. Valves are commonly constructed using materials such as brass, stainless steel, bronze, cast iron, and PVC. Each material caters to specific requirements, as highlighted below:
- Brass has extensive usage owing to its corrosion resistance, ability to be machined, and its effects on both hot and cold water systems. Household Plumbing Systems make use of brass valves, which are exceptionally durable and can withstand pressures as high as 300 psi, depending on the design.
- As Stainless Steel is best known for its strength, together with high corrosion resistance, and ability to withstand extreme temperature ranges, it is the material of choice in industrial or chemical surroundings. For example, some rods made of stainless steel have valves in them. These valves can operate at extremely low temperatures of -50°F, and even higher up to 1,200°F.
- Bronze is often chosen for outdoor conditions or areas that have higher moisture content due to its long-lasting traits. Bronze is exceptionally durable for marine and industrial applications and resists corrosion even against seawater.
- Cast Iron is perhaps the most durable material available, and due to the cost-effectiveness of Cast Iron, it is a popular choice in large-scale plumbing or HVAC applications. While being highly durable, cast iron is known to be brittle under severe stress or impacts.
-
PVC (Short for Polivinyl Chloride) can be used in chemical processing systems or irrigation as it is lightweight and resistant to a number of chemicals. In non-pressured scenarios, PVC valves can withstand temperatures of around 140°F, together with 150-300 psi of pressure.
The correct valve material selection is fundamentally influenced by chemical interactions, temperature, pressure, and environmental conditions. Proper material selection in combination with system specifications will guarantee the use of the valve for prolonged periods while maintaining reliability and unmatched valve performance in even the harshest conditions.
Matching valve types to water pressure requirements
Choosing the appropriate type of valve is important to achieve maximum performance with respect to water pressure. Systems operating over 150 psi are regarded as high-pressure systems, which require robust type valves such as stainless steel or brass valves. These materials have high strength and durability. For example, stainless steel valves have a reputation for enduring internal pressures above 1,000 psi, which is suitable for industrial and other high-pressure applications. Brass valves have high resistance to corrosion and have a useful operating pressure of 600 psi, but are not as durable as stainless steel valves.
In residential water systems where the pressure is between 15-80 psi, low-pressure applications can make use of PVC and plastic valves, which are light and cost-effective. Provided that pressure does not exceed 150 psi, these valves are useful in soft water systems or other lower temperature systems, due to their resistance to chemical corrosion.
Bronze and ductile iron valves are commonly used in mid-range pressure systems between 80-150 psi due to their balance in affordability, strength, and reliable valve operation for residential and commercial use. As with other types of valves, bronze and iron valves should be used according to the manufacturer’s pressure ratings to avoid wear and reduce the risk of failure.
Cost comparison of different valve types in plumbing
While looking at different types of valves for plumbing systems, the composition of the material and use case affect the cost. Below are different classifications as per the material and their price ranges.
- Plastic Valves
5to20 a piece. They are lightweight, do not corrode, and are best suited for non-potable water applications or low-pressure systems. They are, however, less reliable under extreme temperatures and high pressure.
- Brass Valves
Brass is corrosion-resistant and is quite popular when it comes to sinks and taps. They are also used in residential plumbing too which scales the price from 20to20to50 a piece, depending on size and design. The reason they are favored is that they work effectively under moderate pressure, are versatile, reliable, and have good durability for a long time.
- Bronze Valves
The use of bronze valves is not as common as other types of valves because their price range from 30 to 70, putting them above other options. This makes it a mid-range option for when dealing with sensitive pressure systems that are likely to get exposed to seawater or other highly corrosive materials. Its performance is worth the price, as the value is good for this metallic bronze alloy.
- Stainless Steel Valves
Valves made of stainless steel are designed for high-pressure or industrial applications. Depending on the order, such valves cost 50to50to200, or more. Its composition benefits highly abusive environments as it is extremely durable, anti-corrosive, and has a long lifespan, meaning it incurs low cost in the long term.
- Cast Iron Valves
Commonly employed in large water pipelines and during industrial activities, cast metal valves tend to be priced within 70and70and150. Despite being robust, these valves have the disadvantage of being heavy, hence increasing the cost of installation.
In the end, choosing the appropriate valve requires considering more than just the upfront cost. Its lifespan, how well it matches the system’s needs, and its features all play a role. Spending more on a quality valve will reduce upkeep costs and greatly increase system performance over time.
Reference Sources
- Operation Simulation for a Check Valve Used in High-Performance Systems1:
- Key Findings: This study developed an improved butterfly check valve (BCV) design to enhance reliability and safety in pipeline systems. The new design ensures better tightness and durability under high-pressure and high-temperature conditions. Finite element analysis was used to calculate stress-strain states, confirming the valve’s operability and reliability.
- Methodology: The research employed mathematical modeling and finite element methods to simulate the valve’s performance under various conditions. The design was tested for stress, strain, and reliability indicators, ensuring compliance with technical requirements.
- Replacing Metal Parts with Resin in Pipe Installations and Gas Equipment2:
- Key Findings: This study explored the transition from metal to resin in gas distribution systems and equipment. Polyethylene and other resins were found to reduce corrosion, improve earthquake resistance, and lower costs. The research highlighted the need for tailored testing methods to assess resin’s suitability under high-temperature and high-pressure conditions.
- Methodology: The study conducted water-hammer tests, constant load creep tests, and stress rupture tests to evaluate resin’s performance as a metal substitute. It also compared different resin types to determine their viability for specific applications.
- Analysis of a Hydraulic Pipe System with Major and Minor Pressure Losses3:
- Key Findings: This research analyzed pressure losses in hydraulic systems, focusing on the effects of pipe length, roughness, and diameter. It demonstrated how minor and major losses impact system efficiency and provided insights into optimizing hydraulic designs.
- Methodology: The study used Bernoulli’s equation and experimental setups with PVC pipes to measure pressure losses. It calculated friction factors and Reynolds numbers to classify flow types and assess their impact on pressure loss.
Frequently Asked Questions (FAQs)
Q: What are the different types of valves used in plumbing systems?
A: Plumbing systems utilize several different types of valves, each designed for specific applications. The most common include gate valves, ball valves, globe valves, check valves, pressure relief valves, butterfly valves, and mixing valves. Each valve is a mechanical device that serves different functions, like regulating water flow, controlling direction, or ensuring safety in the system. Without valves, modern plumbing would be impossible, as they are an integral part of any plumbing system, allowing for maintenance, emergency shutoffs, and precise control of water distribution.
Q: How do gate valves in plumbing differ from ball valves?
A: Gate valves in plumbing systems use a gate or wedge-shaped disc that moves up and down to control flow. They’re designed for fully open or closed positions (not for regulation) and are commonly used in residential main water supply lines. Ball valves, on the other hand, operate with a hollow ball that rotates to control flow. They provide quick on/off functionality with a quarter-turn handle and offer superior sealing capabilities. Ball valves are more reliable for frequent use, while gate valves are better for situations where the valve is rarely operated but must provide minimal flow restriction when open.
Q: What type of valve in plumbing is best for regulating water flow?
A: Globe valves are often used when precise flow regulation is needed in plumbing systems. Unlike gate or ball valves, which are better for full-on/off applications, globe valves are designed with an internal baffle that forces water to change direction, allowing for accurate flow control. The design makes them excellent for applications where throttling is required, such as shower mixers or outdoor hose bibs. Globe valves can be used in both residential and commercial settings where gradual opening and consistent regulation of water flow are important, though they do create more flow resistance than gate or ball valves.
Q: Which valves are used in residential plumbing for backflow prevention?
A: In residential plumbing, check valves are often used for backflow prevention. These one-way valves allow water to flow in only one direction, preventing contaminated water from flowing back into the clean water supply. There are several types, including swing check valves, spring-loaded check valves, and dual check valves. They’re typically installed at water service entrances, on irrigation systems, or on sump pump discharge lines. Check valves are used to prevent backflow situations that could compromise water quality, making them essential safety components in residential plumbing systems, particularly in areas where backflow is a concern due to pressure fluctuations.
Q: What safety valve in plumbing systems protects against excessive pressure?
A: Pressure relief valves are used as crucial safety devices in plumbing systems to protect against excessive pressure buildup. These valves automatically open when pressure exceeds a predetermined safe level, preventing potential explosions or damage to pipes and fixtures. They’re most commonly found on water heaters, boilers, and expansion tanks. In residential settings, pressure relief valves must be properly sized and regularly maintained to ensure they function correctly in emergency situations. The valve may discharge water or steam when activated, so proper drainage pathways must be provided. Building codes typically require these valves in specific applications to prevent catastrophic failures.
Q: How are butterfly valves used in commercial and industrial plumbing?
A: Butterfly valves are primarily used in commercial and industrial plumbing applications where space is limited but high flow capacity is required. These valves feature a disc mounted on a rod that rotates when the valve is operated. When the valve is open, the disc turns to allow flow; when closed, it seals against the valve seat. Butterfly valves are valued for their compact design, lightweight construction, and quick operation. They’re commonly installed in large diameter pipes in commercial buildings, water treatment facilities, and HVAC systems. While not typically found in residential plumbing, butterfly valves are essential in larger systems where efficient flow control and space conservation are priorities.
Q: What types of valves are best for automatic control in modern plumbing systems?
A: For automatic control in modern plumbing systems, solenoid and motorized valves are the preferred options. Solenoid valves use electromagnetic coils to open or close the flow path when electrically activated, making them ideal for applications requiring remote or programmed operation. Motorized valves incorporate small electric motors to gradually open or close the valve mechanism. These valves can be integrated with building automation systems, smart home technology, or timer-based controls. They’re commonly used in irrigation systems, automated water management, leak detection systems, and high-efficiency commercial buildings. While more expensive than manual valves, these automatic options provide convenience, precision, and can significantly improve water efficiency in both residential and commercial applications.
Q: How do pressure-reducing valves function in residential and commercial settings?
A: Pressure-reducing valves (PRVs) are specialized valves that automatically reduce incoming water pressure to a safer, more manageable level for the building’s plumbing system. In residential settings, PRVs are typically installed after the main shutoff valve to protect household plumbing from municipal water pressure that may be too high (often above 80 psi). In commercial buildings, larger and more robust PRVs are installed to handle greater water volumes while maintaining consistent pressure throughout complex systems. These valves utilize a spring and diaphragm mechanism that responds to downstream pressure, automatically adjusting to maintain the preset pressure regardless of fluctuations in the supply line. Properly functioning PRVs extend the life of plumbing fixtures, prevent water hammer, reduce water consumption, and minimize the risk of leaks throughout the system.
Q: What considerations should be made when selecting different types of valves for specific plumbing applications?
A: When selecting valves for specific plumbing applications, several key factors must be considered. First, determine the valve’s purpose—whether for isolation, regulation, backflow prevention, or pressure relief. Material compatibility is critical; brass and bronze valves are common in potable water systems, while PVC and CPVC are used for chemical applications. Size matching to the pipe diameter ensures proper flow rates. Pressure and temperature ratings must meet or exceed the system’s requirements. Consider the frequency of operation—ball valves are better for regular use, while gate valves may be suitable for infrequent operation. Installation space, maintenance accessibility, and cost (both initial and long-term) are also important factors. Finally, ensure compliance with local building codes and industry standards, which may mandate specific types of valves for certain applications in both residential and commercial plumbing.