Hygienic applications often come with the requirement to use materials that are easy to clean and maintain. In such cases, stainless steel is the preferred choice. However, not all grades of stainless steel are hygienic—some are more appropriate for clean environments than others. In the food processing, pharmaceutical, and healthcare industries, both 304 and 316 stainless steel are popular options. In this article, we analyze the most important differences between them to help you choose the best one for your sanitary needs. From an industry expert to a curious reader, all will gain an understanding of how hygienic stainless steel is.
What is Sanitary Stainless Steel?
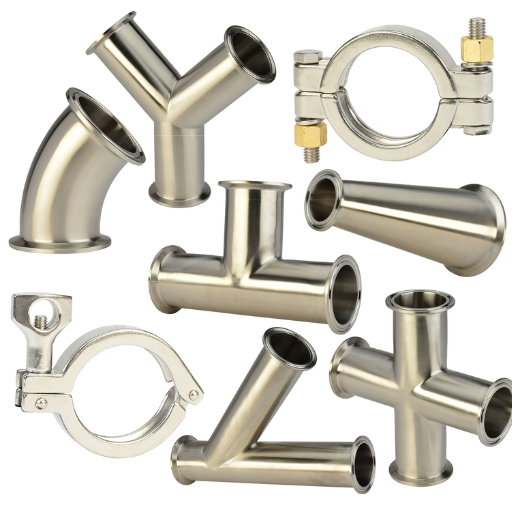
Sanitary stainless steel, also known as sanitary grade stainless steel, is a rigid type of stainless steel used in food, dairy, and pharmaceutical industries where hygiene is critical. It is manufactured to have a high level of smoothness to reduce the surfaces that can collect dirt, bacteria, and other chemicals. Foods and healthcare services that use hygienic steel are very easy to clean, do not rust, and last long to keep their hygiene uncluttered.
Definition and Importance of Sanitary Stainless Steel
Sanitary stainless steel has crucial applications in various fields because of its unparalleled hygiene properties. In food processing, for example, it serves sanitary purposes in the fabrication of tanks, conveyor belts, piping systems, and other FDA and EU-compliant processing equipment. It is also used in healthcare for countertop and sterilization equipment for maintaining surgical instruments, owing to their stringent cleaning protocols.
The stainless steel’s composition, as described above, has a chromium content between 16-18%, which increases its corrosion resistance, making it suitable for use in consistently moist environments or in places exposed to harsh disinfecting chemicals. In addition, stainless steel’s non-porous characteristic is said to mitigate the adhesion of microorganisms and bacteria, which helps in contamination reduction. Recent reports indicate that the global market for sanitary stainless steel has been increasing steadily along with stricter rules in developed countries and a greater need for hygiene in emerging economies.
Contemporary sanitary stainless steel products incorporate new designs and sophisticated production technologies which target performance and environmental standards, thus providing companies with competitive advantages through improved profitability while meeting sustainable requirements.
Applications in Food Processing and Beverage Industries
Sanitary stainless steel plays an important part in the food processing and beverage sectors since it helps maintain product safety, durability, and meet strict hygiene requirements. Various types of sanitary stainless steel are used in industrial applications like storage tanks, piping systems, and processing equipment. This equipment is widely used because they do not easily corrode and can be easily cleaned. In fact, a prominent benefit is its ability to endure extreme temperatures and strong cleaning compounds, which is crucial for avoiding bacterial contamination.
Recent industry reports highlight that the market of stainless steel used in food processing is expected to expand steadily, projected to achieve a compound annual growth rate (CAGR) of over 6% by 2028. This is fueled by the increase in consumer demand for safer and higher-quality food products. For example, in the dairy industry, stainless steel storage tanks have to both comply with strict pasteurization standards and preserve the product ultra-clean. Likewise, breweries and wineries in the beverage industry use stainless steel tanks to preserve product quality and taste. The fact that stainless steel can be recycled also addresses growing concerns regarding sustainability, which is why it is sought after by manufacturers aiming to lessen their environmental impact. Without a doubt, these factors emphasize the significant contribution of stainless steel toward improving operational efficiency and responding to important and changing standards in the industry.
Benefits of Using Sanitary Stainless Steel Tubing
The advantages of sanitary stainless steel tubing are unmatched for those in the food processing, pharmaceuticals, or dairy production industries. Its greatest advantage would be its tremendous resistance to corrosion. This guarantees durability and reduces maintenance costs, even in highly corrosive and moisture laden environments such as those containing acidic materials. Industry research suggests that stainless steel withstands years of corrosion while enduring minimal damage, thus proving to be economically beneficial in the long run.
The risk of bacterial growth is greatly reduced because the outer layer of sanitary stainless steel tubing is smooth. This helps achieve stringent sanitarian requirements. Research indicates that stainless steel tubing is capable of maintaining the purity of the product because it does not allow leaching to occur with sensitive goods such as medicines or beverages. Moreover, stainless steel tubing is capable of withstanding high pressure and temperature and, therefore, is suitable for sterilization stages.
The sanitary stainless steel tubing is environmentally friendly as it can be recycled and aids sustainability efforts. Reports show that a large portion of new stainless steel produced comes from recycled sources, which helps reduce the consumption of resources and lower greenhouse gas emissions. These factors improve operational reliability, and rest assured, the growing environmental and economic demands are being met, further proving why these materials are crucial in various industries.
Differences Between 304 and 316 Stainless Steel
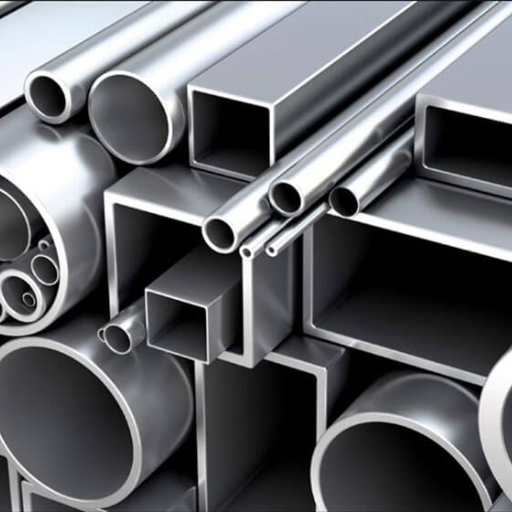
The difference between 304 and 316 stainless steel is in their composition. Due to the presence of molybdenum, 316 stainless steel has enhanced resistance to corrosion, particularly with chlorides and other harsh environments. This improves its suitability for marine, chemical, or high-salinity applications. 304 stainless steel, on the other hand, is more affordable and is used in standard environments that do not extensively expose it to corrosive elements. Both grades are tough and adaptable. However, the difference lies in the choice of environment and application requirements.
Corrosion Resistance: 304 vs 316 Stainless Steel
Considering corrosion resistance, I would pick 316 stainless steel for applications that involve exposure to chlorides, harsh chemicals, or any marine setting because it is far superior. For more standard environments without major corrosive elements, 304 stainless steel is quite dependable and economical.
Composition: What Makes 304 and 316 Different?
The pitting and crevice corrosion resistance of both alloys differs because molybdenum is only part of 316 stainless steel. It is this difference that heavily impacts its performance characteristics. 316 stainless steel possesses 2-3% molybdenum while 304 stainless steel does not have any at all. The performance difference is starkest in marine and other chloride-rich environments. 304 stainless steel contains 18-20% chromium and 8-10.5% nickel, while 316 stainless steel contains 16-18% chromium and 10-14% nickel. The addition of molybdenum strengthens it further, especially during chemical exposure.
Without molybdenum, 304 stainless steel shows its weaknesses in saline and coastal environments. The lack of pitting and crevice corrosion resistance could lead to structural impairment alongside reckless exterior damage. 316 stainless steel avoids all these issues due to its supportive molybdenum content. The difference in ability to endure corrosion is crucial when considering the materials to manufacture medical and food processing equipment, as well as other infrastructure.
When to Use 304 vs 316 Stainless Steel
When choosing between 304 and 316 stainless steels, it’s important to consider the working environment, resistance to corrosion, and pricing.
Corrosion Resistance: 304 stainless steel is resistant to corrosion for a wide range of applications; nevertheless, 316 stainless steel performs better in more extreme conditions, particularly in environments with chlorides, seawater, or industrial chemicals. As an example, 316 stainless steel is able to endure chloride concentrations of up to around 1,000-2,000 ppm while 304 stainless steel will likely suffer from pitting and crevice corrosion in the same environment.
Strength and Temperature Tolerance: Both grades have exceptional durability and can endure elevated temperatures. However, 316 stainless steel performs better in extremely high or low temperature applications due to its molybdenum content, which enhances heat resistance.
Applications:
- 304 Stainless Steel: Great for use in most indoor uses like kitchen appliances, breweries, and buildings. Its reasonable price and strong resistance to corrosion make it the bestselling grade of stainless steel.
- 316 Stainless Steel: Ideal for use in saltwater and other harsh chemical environments, as well as extreme heat and cold. Widely used in marine equipment, medical devices, and chemical storage tanks.
Cost: On an average basis, 316 stainless steel costs 20-30% more than 304 stainless steel because of the addition of molybdenum and nickel. Nevertheless, the cost is usually offset by the durability withstanding aggressive conditions.
Careful consideration of these elements helps engineers and producers select the proper grade of stainless steel suited for the application to enhance performance and cost effectiveness.
Understanding Stainless Steel Grades
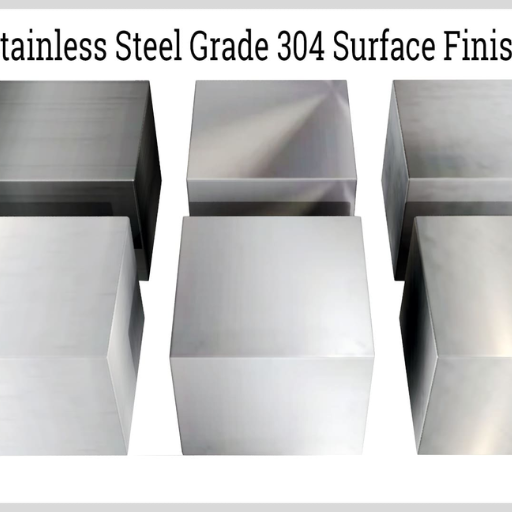
Because of its cost-effectiveness, 304 stainless steel is frequently used for food preparation equipment as it is ideal for indoor use. Conversely, 316 stainless steel has superior resistance to harsh marine and chemical environments which makes it the preferred choice for these applications. The primary deciding factors between these grades is the specific environmental requirements and the budget of your project.
Overview of Common Stainless Steel Grades
Composition
304 stainless steel contains 18-20% chromium and 8-10.5% nickel. Because of these parts, it is also called “18-8 stainless steel.” On the other hand, 316 stainless steel has a composition of 16-18% chromium, 10-14% nickel, and 2-3% molybdenum. The addition of molybdenum in 316 enhances its resistance to pitting and corrosion, especially for pipes and heat exchangers, which are used in chloride-laden environments.
Corrosion Resistance
Although both grades have superb resistance to corrosion, 316 stainless steel furnishes greater resistance than 304 stainless steel in more corrosive environments. Molybdenum’s presence allows 316 to endure seawater and chemical solution exposure, making it perfect for severe marine activities and industrial processes.
Mechanical Properties
Both materials are alike in their mechanical properties, although 316 has a slight advantage in tensile strength because of its improved composition. For example:
- 304 Stainless Steel has a tensile strength of approximately 73,200 psi (pounds per square inch).
-
316 Stainless Steel offers a tensile strength of around 80,000 psi.
Temperature Resistance
316 stainless steel boasts a greater resistance to corrosion, but 304 stainless steel outshines it with lower production costs. Compared to 316, 304 performs well under 1,598°F while 316 stainless can withstand 1,672°F, making them both useful in diverse high-usage temperature scenarios.
Applications
- 304 Stainless Steel: common for household appliances, kitchen tools, architectural trim, and automobile parts, as it is durable and cost-efficient.
- 316 Stainless Steel: surgical tools, marine hardware, and industrial pipes due to exposure to salts, acids, or other harsh chemicals. Raw materials were not altered, but were used to the final product.
Cost Comparison
Due to its increased nickel and molybdenum content, 316 stainless steel is typically more costly than 304. This is usually one of the reasons why it is more costly when compared to 304. Knowing this will make things much easier when selecting a material, since one would need to balance the performance needs with how far their budget stretches.
Understanding these differences is what makes the decision on which stainless steel grade to use easy, and customizable to the intended purpose and surroundings.
Factors Influencing the Choice of Stainless Steel Grades
While picking a grade of stainless steel, pay close attention to the following key considerations:
- Corrosion Resistance
Pick a grade according to the amount of salt, chemicals, or moisture the application will encounter. For maximum exposure to corrosive elements, it is best to use 316 stainless steel or other similar upper-grade options.
- Strength Requirements
What is the required mechanical strength for the application? Heavy loads or structural elements might necessitate higher-strength grades.
- Temperature Resistance
What is the Operating Range of the temperature? Some grades are better suited to extreme heat and cold.
- Cost Efficiency
What is the material cost in relation to its performance? Critical applications might mark up the price; however, it is justifiable for the benefits one gains from spending more, as in the case of grade 316.
- Appearance and Maintenance
For grade selection, look for one that will be easy to maintain and will retain its finish, such as stainless steel 304, for these applications.
Concentrating on these elements guides the process selection to be realistic and tailored to the requirements of the application.
ASTM A270 and Its Relevance to Sanitary Stainless Steel
ASTM A270 sets the specification for welded and seamless sanitary tubing in stainless steel. This standard ensures that the tubing is hygienic and can be used in food, beverage, pharmaceutical, or dairy industries. It also sets the minimum requirements for the raw materials, the quality of the machining, and the fitting tolerances classification to guarantee sanitation and cleanability. Compliance with the ASTM A270 makes sure that the stainless steel Tubing is strong and safe for sanitary applications.
Benefits of Using 316 Stainless Steel in Sanitary Applications
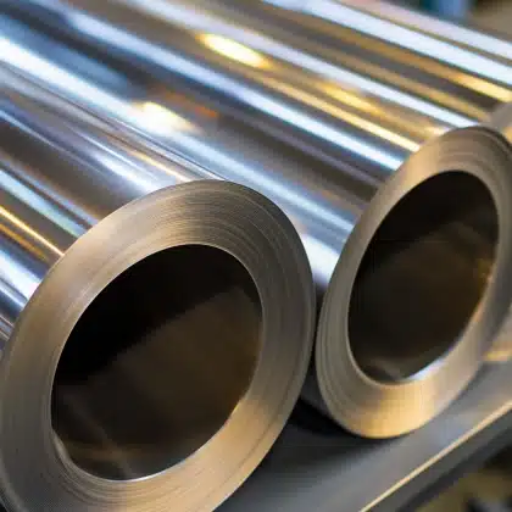
316 stainless steel stands out among other types for pristine industries because of its properties which are greatly advantageous. Better yet, the benefits support its use in incredibly sensitive fields. The aid of this stainless steel extends to being corrosion resistant, even in the most extreme conditions, with high cleanliness and endurance standards. Its surface finish is smooth enough to make compliance with surface cleanliness and hygiene standards possible, while being easy to clean, furry adjustable. Also, 316 stainless steel is strong and safe, has a long-lasting nature, can endure high temperatures, to maintains safety and efficiency in essential processes.
Enhanced Corrosion Resistance in Harsh Environments
316 stainless steel demonstrates exceptional resistance to corrosion in harsh environments like marine, chemical processing, and industrial settings. This advanced alloy has 2-3% molybdenum, which helps in resisting pitting and crevice corrosion by chloride ions significantly. This grade of stainless steel has been proven to withstand long exposure to saltwater, making it ideal for shipbuilding and offshore applications.
316 stainless steel also performs reliably in environments that are acidic or alkaline, such as chemical production facilities. It also withstands sulfuric, hydrochloric, and other acidic solutions, ensuring structural integrity for a long time. For example, data shows that even under extreme conditions, 316 stainless steel has a corrosion rate of less than 0.1 mm per year, further highlighting its remarkable durability.
With these advantages, 316 stainless steel has become one of the most trusted materials in safety and performance-critical applications where protection from corrosion is needed.
Durability and Longevity of 316 Stainless Steel
The enduring characteristics of pitting and crevice corrosion on 316 stainless steel, especially in chloride environments, is due to its molybdenum content. Molybdenum pitting and crevice corrosion moat especially go to town in chloride-infested environments. For instance, marine grade 316 stainless steel is great for the salt water applications where other material would absolutely rot. Research shows that this alloy can endure salt spray conditions for more than 2,000 hours while not showing substantial surface corrosion.
Moreover, 316 stainless steel has a tensile strength of about 515 MPa, thus guaranteeing structural integrity of the material during intense pressure. The chemical processing and power generation industry relies on 316 stainless steel because its strength and excellent creep resistance at high temperatures, for example, 870 degrees Celsius, makes it reliable. In addition, 316 stainless steel also has low thermal expansion, which guarantees that 316 stainless steel is stable when enduring shifts in temperature over time.
Improvements in 316 stainless steel’s manufacturing processes have further enhanced its long-lasting nature. 316 stainless steel’s alloy composition precision and forging processes minimize microstructural imperfections, increasing its fracture toughness and fatigue resistance. With adequate care, parts manufactured from 316 stainless steel can last over 50 years, reinforcing its reputation as a material that balances performance, longevity, and economical value across various challenging tasks.
Why 316 Stainless Steel is Preferred in Food-Grade Applications
- Superior Corrosion Resistance
Molybdenum is present in 316 stainless steel, improving its resistance to corrosion in conditions where salt and food processing is present, or if the environment is acidic.
- Non-Reactive Surface
Food processing components made from 316 stainless steel will not change the smell, taste or the color of the food due to its non-reactive surface.
- Ease of Cleaning and Sanitation
Because 316 stainless steel can be polished to a smooth surface, it can minimize bacterial and biofilm proliferation, which is important for maintaining the food hygiene processing standards.
- High Resistance to Extreme Temperatures
Freezing and high heat are typical in food prep and storage. 316 stainless steel’s wide operating temperature range makes it suitable for these conditions.
- Compliance with Food Safety Standards
The FDA and EU legal policies have strongly defined precautions for food safety, and 316 stainless steel is safe and compliant with such regulations for any application involving food.
- Structural Strength and Durability
316 stainless steel’s toughness aids in alleviating the mechanical stress placed on food production equipment, decreasing equipment maintenance, and extending maintenance intervals.
- Wide Applications in the Food Industry
Some of the common uses of 316 stainless steel includes the fabrication of food processing equipment, storage tanks, conveyor systems, kitchen equipment, which shows its reliability and versatility in food grade applications.
Sanitary Tubing and Fittings: What to Know
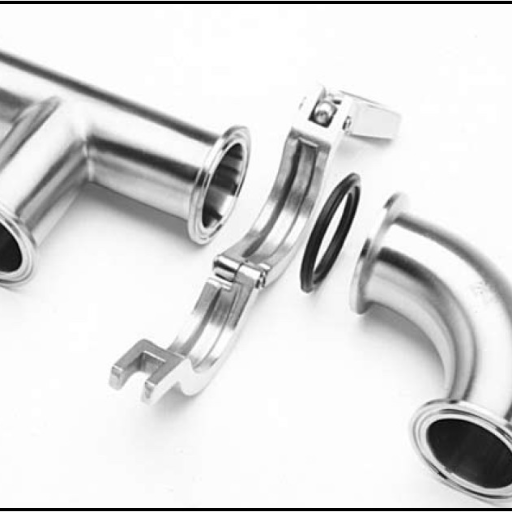
Sanitary fittings and tubing play a crucial role in many industries such as food and beverage, pharmaceuticals, and biotechnology. Their purpose is to keep operations clean and free from hygiene-related issues. They also maintain high standards of cleanliness to avoid any form of cross-contamination. Most make the tubing from stainless steel because it does not corrode and is durable. Fittings include clamps, valves, and connectors that join parts together to form leak-proof seals. Such components are subject to rigorous hygienic requirements set by 3-A SSI or FDA.
Types of Sanitary Tubing Used in Food Processing
The sanitary tubing utilized in the food industry is divided into different types according to their methods of operation while still maintaining a high level of cleanliness:
- Stainless Steel Tubing
Sanitary tubing is most generally made from stainless steel because it does not rust, can withstand destruction, and is easy to clean. The preferred grades are 304 and 316 stainless steel, with 316 being more resistant to severe chemicals and high temperatures. Stainless steel tubing is appropriate for the transportation of fluids such as milk and juices, as well as the processing of high-pressure steam, due to the high industrial cold and heat resistance.
- Plastic Tubing
Food-grade plastic tubing includes polyvinyl chloride (PVC), is lightweight, and provides greater flexibility of use in various fields. This type of tubing is often used in the conveying of ”light” liquids or non-standard systems that require high adaptability. A number of the plastic tubing is end-horsed for safe drinkable water and bears NSF 51 or 61 marks certifying them for food-grade materials.
- Silicone Tubing
Silicone tubing is used greatly in food production as it only bears gas and fluids within a highly pure surrounding. It is ensured that the surroundings are free from any contamination.
- Teflon (PTFE) Tubing
Teflon tubing has an outstanding reputation for remaining chemically inert and requires very low maintenance. It is common in systems involving the movement of corrosive liquids, fats, or oils and similar substances. Teflon is non-stick in nature which keeps the residue adhesion to a minimum and hence can be cleaned easily.
- High-Pressure Tubing
When working with carbonated soft drinks or highly viscous liquids, reinforced stainless steel or braided high-pressure tubing is a must. These tubes withstand the intense mechanical pressures of high-band systems with absolute safety and sanitation.
Every type of tubing must meet the requirements set forth by the FDA, 3-A SSI, or EU food safety regulations. Picking the right sanitary tubing helps formidably streamline operational efficiency, sustain high standards of product quality, and fulfill relevant health and safety regulations.
Welding and Joining Sanitary Stainless Steel Tubing
Joining and welding sanitary stainless steel tubing is a process that has to be done very carefully to ensure cleanliness and integrity are preserved. One of the most common methods is TIG (Tungsten Inert Gas) Welding because it provides a neat and smooth finish. Welds would inevitably undergo some contamination, so they need to be inspected for cracks or pits that would compromise the smooth flow. In order to maintain hygiene, all joints need to be back purged and then polished to eliminate any residues. Compliance with certain regulations, particularly those marked by ASME BPE, ensures that safe and hygienic conditions are maintained while welding.
Best Practices for Installing Sanitary Fittings
The installation of sanitary fittings must be done with great attention to accuracy and hygiene. Attention to detail, sanitary fitting alignment is crucial. Proper alignment minimizes the potential for excessive stress on the connections, which may cause leakage or contamination. Stainless steel grade 304 or 316 is the preferred material due to its resistance to corrosion, as well as its ability to withstand deterioration over time, which is essential for sanitary systems. Gasket fittings are EPDM-based rubbers, which are said to be Volatile Organic Compound (VOC) checked and safe to use with a variety of fluids.
The recommended torque values should not be exceeded since they can lead to loss of sealing integrity and destruction of gaskets due to over-torquing. Periodic measuring of system pressure following the installation is good practice to ensure there are no leaks and the connections made are properly secured. Systems should have a proper slope gradient, which should not be less than an inch per foot in order to drain freely, inhibiting stagnation of fluids around the system.
Adhering to 3-A and ISO 2852 criteria ensures that the installation complies with sanitary requirements and signifies the need for system security as well as simple functionality. Using IoT devices, remote surveillance inspections can be combined with system cleaning, thus preserving the sanitary systems and improving their service life after installation.
Choosing the Right Stainless Steel for Your Sanitary Process
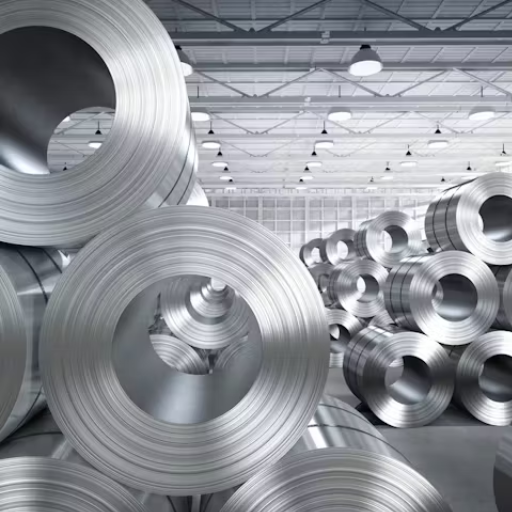
Concentrate on stainless steel options that have high levels of corrosion resistance, durability, and are simple to clean when choosing the right metal for your sanitary process. Stainless steel grades 304 and 316 are widely accepted because they are reliable in sanitary applications. Grade 316 is especially favored for processes with strong chemicals or saline solutions due to its high corrosion resistance. Check that the stainless steel conforms to industry regulations such as FDA and 3-A compliance, which ensures hygiene and safety standards are upheld. Evaluate the particular requirements of your process to determine the correct grade to use.
Evaluating Your Needs: 304 vs 316
It is vital to note the specific characteristics of 304 and 316 stainless steels in order to make the right choice for your application. Both types belong to the austenitic family of steels and are very tough, with the main difference being their chemical composition and how they perform in certain conditions.
The most common type is grade 304 stainless steel because of its low cost and flexibility. It includes 18% chromium and 8% nickel, which enables strong oxidation and corrosion resistance. 304 SS excels for use in simple everyday environments,s which include food processing equipment, sinks, and general kitchen utensils.
Grade 316 stainless steel, on the other hand, has a 2-3% added molybdenum, greatly increasing its resistance to pitting and crevice corrosion. This makes 316 Steel best for marine equipment and devices that involve drugs and biological materials where saline or harsh chemicals are concerned.
To effectively explain, 316 will far outlast 304 in areas where chlorides reach over 1000 ppm, like in seawater. Furthermore, 316 stainless steel is proven to retain greater tensile strength for long period exposing to elevated temperatures, therefore it is more desirable in high-stress industrial environments.
Proper allocation of resources is controlled by evaluating factors such as the presence of corrosive agents, the temperature range involved, and selecting a suitable grade. Grade 304, while versatile, is weakest in highly corrosive environments. Grade 316, in comparison, is far more efficient in these conditions but requires a larger investment.
Consulting Standards for Sanitary Stainless Steel
Sanitary stainless steel grades require particular industrial markings to guarantee cleanliness, durability, and safety in food processing, pharmaceutical, and medical applications. Organizations like the American Society for Testing and Materials (ASTM) and the Food and Drug Administration (FDA) provide rigorous recommendations for stainless steel used in sanitary environments.
An example is ASTM A270, which outlines the smooth bore requirements for bacterial-resistant interior surfaces of grade A seamless and welded austenitic stainless steel sanitary tubing. Also, FDA-recommended stainless steel grades for food contact applications are often 304 and 316 due to their ease of cleaning and excellent corrosion resistance.
Comparison data indicates that 316 stainless steel with added molybdenum is significantly more pitting and crevice corrosion resistant than 304, particularly in chloride-containing environments. These factors make it optimal for severe sanitary use involving saline or acidic solutions. Adopting these standards not only guarantees regulatory approvals but also improves the reliability and lifespan of critical systems.
Common Mistakes to Avoid When Selecting Stainless Steel
- Overlooking the Specific Environmental Conditions
A typical oversight is not paying attention to the environment in which the stainless steel will be exposed. For example, 304 stainless steel is commonly chosen for multipurpose applications, but its corrosion resistance tends to be inadequate in coastal or marine environments with heavy exposure to chlorides. Research shows that 316 stainless steel performs far better because of its higher molybdenum content, decreasing the aggressiveness of pitting corrosion by approximately 25-30% over time.
- Ignoring Temperature and Stress Factors
Different stainless steel grades have disparate reactions to elevated temperatures and mechanical stress. For two-stage furnace equipment, for example, above 1000 deg C, type 310 or 321 stainless steels are recommended due to their preservation of structural rigidity damage damage-limiting ability. If an inappropriate grade is chosen, the material may experience thermal expansion or fatigue, increasing maintenance costs as well as lowering operational efficiency.
- Selecting Based on Cost Alone
Another common mistake is selecting stainless steel internals because they are cheap ignoring considerations for the overall performance in the long run. In this case, the use of 304 stainless steel alloys may be cost effective but it’s relatively short lifespan and higher maintenance costs in corrosive environments could prove to be far more expensive. Some industry-standard data case studies suggest that higher-grade alloys are seldom replaced due to their longevity and lower maintenance, which often results in lower costs through durable lifecycle savings.
- Failing to Verify Compliance with Standards
Some purchasers forget to check if the stainless steel is compliant with such international standards as ASTM or ISO. Steel without these certifications may have arbitrary compositions of its components; hence, it will perform poorly and may not provide the guarantee of quality. Compliance helps avert nondestructive testing failures in critical applications and provides assurance that fundamental operating conditions will be met.
- Overlooking Surface Finish Requirements
The aesthetic and corrosive resistance properties of stainless steel are enhanced by its surface finish. For example, polished surfaces offer better corrosion resistance in wet or humid environments than rough finishes, which can entrap dirt and debris. Research indicates that smoother surfaces tend to have less resistance to the growth of microorganisms, which is important for food and healthcare industries.
Preventing these design missteps while aligning the stainless steel grade, surface finish, and specifications to the intended use will help businesses achieve optimum operational effectiveness, reliability, and cost efficiency.
Reference Sources
- Benefits of EDC and linear receivers for short reach 40/100GE – Discusses the transition to SFP+ modules and their impact on adoption challenges.
- Characterization of electro-optical devices with low jitter single photon detectors – Explores the use of SFP+ modules in optical sampling oscilloscopes beyond 100 GHz.
Frequently Asked Questions (FAQs)
Q: What is the difference between 304 and 316 stainless steel in terms of sanitary use?
A: The main difference between 304 and 316 stainless steel lies in their alloy composition. 316 stainless steel contains molybdenum, which provides enhanced resistance to corrosion, particularly in chloride environments. Therefore, while both are considered food-grade stainless steel, 316 is often preferred for applications that require higher sanitary standards.
Q: Is 304 stainless steel considered a food-grade stainless steel?
A: Yes, 304 stainless steel is commonly classified as food-grade stainless steel. It is suitable for a wide range of food processing applications, but it may not be as resistant to corrosion as 316 stainless steel, especially in environments with high chloride levels.
Q: What are the sanitary standards for stainless steel materials?
A: Sanitary standards for stainless steel materials typically require that the steel is non-toxic, easily cleanable, and resistant to corrosion and pitting. Both 304 and 316 stainless steel meet these requirements, making them suitable for use in sanitary applications such as food and beverage processing.
Q: Why is 316L stainless steel often used in sanitary tubing?
A: 316L stainless steel is often used in sanitary tubing due to its low carbon content, which reduces the risk of carbide precipitation during welding. This quality helps maintain the corrosion resistance of the steel, making it ideal for high-purity applications.
Q: What makes stainless steel a preferred material for sanitary pipes?
A: Stainless steel is preferred for sanitary pipes because it is durable, resistant to rust and corrosion, non-reactive, and easy to clean. Its smooth surface helps prevent the buildup of bacteria, which is crucial for maintaining sanitary conditions in food and pharmaceutical industries.
Q: Can different stainless steel alloys be used interchangeably in sanitary applications?
A: While different stainless steel alloys can be used in sanitary applications, it is essential to consider their specific properties. For example, 304 and 316L have different corrosion resistance levels, so using 316L in a highly corrosive environment would be more appropriate than using 304.
Q: How does the carbon content affect the grade of stainless steel?
A: The carbon content in stainless steel affects its mechanical properties and corrosion resistance. Higher carbon content can lead to improved strength but may reduce corrosion resistance. For sanitary applications, low carbon grades like 316L are preferred to maintain both strength and corrosion resistance.
Q: What are the advantages of using welded sanitary tubing made from 316 stainless steel?
A: Welded sanitary tubing made from 316 stainless steel offers several advantages, including enhanced corrosion resistance, a smooth interior surface that facilitates cleaning, and the ability to handle high-pressure applications. These features make it ideal for food-grade applications.
Q: Are there any disadvantages to using 304 grade stainless steel in a sanitary environment?
A: While 304 grade stainless steel is suitable for many sanitary applications, its lower corrosion resistance compared to 316 stainless steel can be a disadvantage in environments exposed to harsh chemicals or high chloride levels. This may lead to quicker degradation in such conditions.
Q: What is the importance of selecting the right grade of stainless steel for food and beverage applications?
A: Selecting the right grade of stainless steel is crucial for ensuring product safety, preventing contamination, and maintaining the integrity of the food or beverage. The right grade, such as 304 or 316 stainless steel, will provide the necessary corrosion resistance and meet sanitary standards required in these applications.