Steel is a material that is used globally in construction, automotive, manufacturing, and more. In fact, steel differs in grade, and not all of them have the same set of characteristics. Knowing which type to choose and its associated steel grade requires a careful analysis of grade properties, composition, and performance. The guide is aimed at providing a detailed analysis of the SAE steel grade chart, which is a system that classifies steel based on its mechanical traits and chemical composition. After reading this article, the audience will comprehend the anatomy of steel grades and appreciate the relevance of the SAE chart with its different grades. This will be of valuable significance for professionals in the industry and materials enthusiasts.
What are the main grades of steel, and how are they classified?
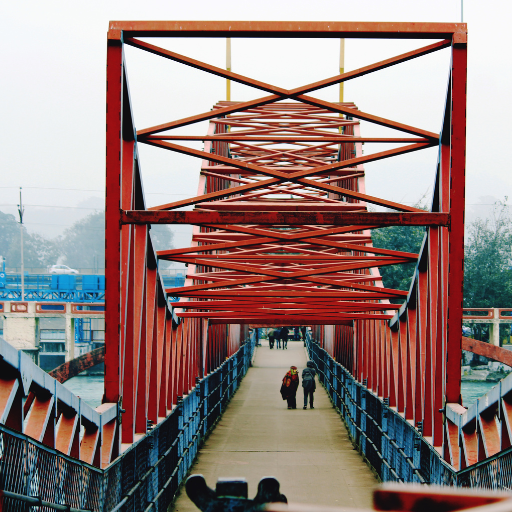
Steel has 4 main classes: Carbon Steel, Stainless Steel, Alloy Steel, and Tool Steel. Each grade has distinct chemical mixtures and mechanical qualities. Carbon steel is a combination os iron and carbon, and its types are classified as low, medium, and high carbon steels. In alloyed steels, chrome, molybdenum, or nickel is added to improve their strength and durability. Stainless steel has high resistance to corrosion due to the high concentration of chromium. Tool steel is designed for particular applications, and it is used for cutting and shaping because of its high hardness. Often has recommended contents of tungsten or vanadium.
Understanding the steel grading system and standards
Choosing the right steel for a project can at first seem challenging, but getting to know the steel grading system is paramount in meeting any expectation. Chemicals within the steel, its structure and mechanical traits, and intended application are relevant factors that grade the steel, in addition to proper organizations such as ASTM, SAE, EN, and many more, which provide confidence and grade reliability. It’s crucial to understand the differences in steel grades, such as low carbon steel being beneficial for ductility, stainless steel preventing corrosion, and tool steel providing formidable toughness. These standards have helped maintain quality and guarantee durability for many industries, and certainly allow achieving optimal performance at a lower cost.
The role of carbon content in different grades of steel
The amount of carbon in steel dictates its grade and affects its properties. Low-carbon steel contains less than 0.3% carbon and is highly ductile and weldable, making it suitable for structural applications. Medium carbon steel contains 0.3% to 0.6% carbon and has a better strength-to-wear ratio, making it useful for automotive parts and machinery. High carbon steel has the greatest percentage of carbon content at 0.6% to 1.4%, giving it superior hardness and strength compared to the other grades, which makes it great for tools and cutting instruments. Carbon’s impact on steel is vast because while higher carbon content strengthens and hardens steel, it also reduces ductility and weldability. Distinguishing the amount of carbon content in steel is important to choose the desired grade for a specific application.
How alloying elements affect steel properties
In my opinion, the performance of steel is optimized when its properties are fully understood, which heavily relies on the proper alloying elements. As an example, chromium and nickel are easily identified as primary components in the production of stainless steels because of their ability to increase corrosion resistance. Manganese has a positive impact on toughness and wear resistance while increasing molybdenum’s strength at higher temperatures, as well as assisting in hardenability. In numerous cases I have come across, carbon, while an “influencing” alloying element, always exhibits extremes when it comes to its effect on hardness and tensile strength. Through consideration and integration of these elements, they can be arranged in such a manner that steel properties will be relevant to particular industrial necessities, ensuring their utmost efficiency and their needed robustness.
What are the different types of carbon steel grades?
The different grades of carbon steel are divided into three major types depending on the amount of carbon they contain: low-carbon steel, medium-carbon steel, and high-carbon steel. Low-carbon steel, which has a maximum of 0.3% carbon content, has a considerable amount of ductility. Therefore, it is easily weldable and perfect for construction and manufacturing purposes. Medium carbon steel, which has a carbon content of 0.3 to 0.6 percent, provides a balance between strength and toughness and is often used for automotive parts as well as machine components. High-carbon steel is very hard and wear-resistant, containing 0.6% to 1.4% carbon, and is commonly found in tools, blades, and other durable heavy equipment. The distinct purposes of industrial requirements for each grade are what set them apart.
Low-carbon steel grades and their applications
Mild steel, or low-carbon steel, is quite malleable due to its low carbon content, usually below 0.3%. In my opinion, its strength, ductility, and weldability make it an obvious choice for construction and manufacturing. I have often used this material for Structural beams, sheet metal for vehicle bodies, and pipelines. Its ease of machining enables the manufacture of bolts, screws, and other fastening devices. Also, low-carbon steel possesses case-hardening ability, which enables a hard surface layer to be produced over a softer interior. This feature improves resistance to wear for some components.
Medium carbon steel properties and uses
With a carbon content of 0.3% to 0.6%, medium carbon steel offers a favorable balance between strength and ductility. When compared with low-carbon steel, this type of steel has a greater tensile strength and wear resistance, which makes it perfect for components that require strength and toughness. Some frequent examples are axles, gears, and crankshafts in automobiles, and also railway tracks and construction parts. Further enhancement in mechanical properties due to tailoring in performance for specific applications can be achieved using quenching and tempering.
High carbon steel characteristics and specific applications
Based on my professional experience with high carbon steel, its primary traits are the carbon percent, which is normally above 0.6%. This makes the material very hard and strong, which is ideal for tools and cutting instruments, including knives, drills, and even saw blades. Unfortunately, these advantages come with a disadvantage; its ductility is lowered while brittleness is increased, which requires more attention when dealing with the material during manufacturing and its use. For it to satisfy predetermined conditions in high-stress environments, heat treatment is essential to optimize most of its properties. At the end of the processing, high carbon steel is unsurpassed for specialized applications because of its exemplary reliability.
How are stainless steel grades categorized?
The classification components for stainless steel grades include their chemical makeup and crystalline structure. The broad classifications consist of austenitic, duplex, ferritic, martensitic, and precipitation-hardening stainless steels. Some of the deciding factors for these grades are corrosion resistance, strength, and other applicable purposes, which are determined by chromium, nickel, and molybdenum content. For industry-wide coherence, these grades are categorized by classification systems such as the AISI and UNS standards, which further divide and identify these grades.
Austenitic stainless steel grades (including 304 stainless steel)
In case you were interested in learning more about one of the most commonly used grades of stainless steel; Austenitic, then do not worry, I will explain it. These types including the famous 304 stainless steel grade, are notable for their ease of fabrication, high durability in addition to having excellent corrosion resistance. Let me explain using some key parameters for better understanding.
- Corrosion Resistance: Austenitic stainless steels, like grade 304, contain high amounts of chromium (typically around 18%) and nickel (approximately 8-10%). This specific ratio creates a passive chromium-oxide film on the material’s surface, commonly known as rust, thus shielding it from corrosion due to oxidation and harsh conditions. Consequently, 304 is frequently utilized in the production of kitchen appliances, food processing equipment, and even chemical plants.
- Strength and Ductility: These steels have outstanding strength, which is complemented by remarkable ductility. Their incredible ability to resist bending, shaping, or breaking even under severe forced conditions is attributed to the face-centered cubic (FCC) crystalline structure of these alloys.
- Non-Magnetic Properties: Austenitic grades, such as 304, are mostly non-magnetic in the annealed condition. This is a desirable trait when dealing with the advanced fabrication of electronic equipment, which is often hindered by magnetic interference.
- Temperature Performance: Grades like 304 keep the best properties for low and high temperature endurance. Although for heat resistance, metallurgical grades like 316 or 310 are more suitable for the intended purposes.
- Cost-Effectiveness: Known as the workhorse of the metal industry, 304 stainless steel provides the best-practice balance among all businesses due to its relatively low cost compared to some other specialized grades.
The combination of these features explains why austenitic stainless steels, especially grade 304, are the backbone of so many construction and manufacturing projects. For industrial machinery and robust utensils used in everyday life, 304 stainless steel provides dependable service in numerous settings.
Martensitic stainless steel types and corrosion resistance
Martensitic stainless steels are best known for their strength and hardness, which makes them ideal for use in cutlery, automotive components, surgical instruments, and many other industries. Their war on corrosion, however, is harder to win when compared to the austenitic or ferritic grades due to their higher carbon and chromium content. Surface finishing and proper heat treatments help improve their resistance to corrosion, but they are best suited in environments with less extreme corrosion and more toughness and wear.
Comparing different grades of stainless steel
With regard to property grade comparison of stainless steel, matching the material property to the respective application always stands out. In case corrosion and formability are the leading factors, austenitic stainless steels tend to be my foremost recommendation, especially while working with the food processing or chemical industry. Whereas, in case strength together with wear resistance is an important factor, martensitic grades tend to be very useful, though achieving maximum performance for these steels requires attention to detail with heat treatment. For cases where moderate strength and durability, together with a certain level of corrosion resistance, are required, ferritic steels are less expensive and helpful. In summation, the right grade selection relies upon the project’s environmental conditions, mechanical requirements, and anticipated performance over time.
What are the SAE and AISI steel grade classification systems?
The two systems developed by the Society of Automotive Engineers (SAE) and the American Iron and Steel Institute (AISI) represent the most common methods for classifying steels in terms of their chemical composition and mechanical properties. Each type into which various steels are grouped is assigned a numerical code. The first digits of this code usually specify the group to which the material belongs, such us carbon steel, stainless steel, etc., while the remaining digits indicate the particular alloying constituents along with the quantity of carbon present. This helps the manufacturers and engineers who are dealing with different industrial applications to exercise great simplicity and accuracy while selecting the suitable materials.
Understanding SAE steel grades and the Society of Automotive Engineers standards
Reflecting on my professional experience in the sector, it is evident that knowledge of SAE steel grades is paramount for ensuring that the correct material is allocated to the appropriate application. The standards set by the Society of Automotive Engineers constitute a vital reference that not only facilitates the choice of materials but also promotes their homogeneity throughout different projects. For example, my understanding of the difference between carbon and stainless steels, as well as the ability to comprehend the numbers associated with them, has enabled me to choose materials that optimize strength, durability, and cost. The advantages of the system go beyond streamlining the design process; it also saves money by minimizing the risks of misapplying materials in crucial places.
The American Iron and Steel Institute (AISI) classification system
The classification system of the American Iron and Steel Institute AISI is an organized approach to classify and identify steels according to their chemical composition and characteristics. It uses a number system wherein the first two digits represent alloy type, while the last two digits denote the quantity of carbon content. For example, 1020 steel is a simple carbon steel with a carbon content of 0.20%. This helps in simplifying the process of choosing the right material and promotes standardization of selection, resulting in better efficiency in matching steel grades with engineering requirements.
How to read and interpret steel grades chart designations
Reading and understanding steel grades chart designations is simple once you have learned the framework. In my personal opinion, the trick is splitting the digits into parts. The first two digits emphasize the type of steel, or the alloying components. “10” depicts a plain carbon steel, while the rest indicates if there are nickel or chromium alloys. The last two digits indicate the carbon content of the steel in parts per hundred. A 1045 steel grade, for instance, is a plain carbon steel with a nominal carbon content of 0.45%. Such a breakdown greatly facilitates the assessment of the steel’s characteristics, for instance, the strength and ductility, and their relation to the intended industrial uses.
What are alloy steel grades and their properties?
There are numerous categories of alloy steels that can be used for many applications – automotive components, maintenance engineering, mechanical engineering, structural engineering, etc. Features such as wear resistance, durability, and strength make them a favorable choice. Apart from these, they also offer enhanced hardness compared to normal carbon steels. Alloy steel grades, in general, are those containing various quantities of manganese, chromium, nickel, molybdenum, or vanadium. For example, as for chromium, it increases the base material’s resistance to corrosion,n while forming alloys of nickel greatly aid in enhancing toughness. As for Molybdenum, it acts on strengthening, along with enhancing the material’s ability to tolerate increased levels of temperature. The division of alloyed steels is completed by their class composition,n, along with the designated application.
Common low-alloy steel grades and applications
In terms of common low-alloy steel grades, I often prefer 4140, 4340, and 8630 because of their excellent performance in challenging applications. For example, 4140 is popularly known for its strength and wear resistance, which makes it very popular in the manufacturing of gears and shafts. On the other hand, 4340 is well-known for its outstanding toughness, which easily qualifies it for use in aerospace and other heavy machinery parts. Last but not least, 8630 has quite a good balance between strength and weldability, making it a common choice in the oil and gas sector for drill collars and fittings. Each of these grades possesses different characteristics, making them tailor-fit for a particular application, resulting in greater efficiency and dependability in different industries.
High-strength low-alloy steel properties
Using my background knowledge, I would like to explain some essential characteristics of high-strength low-alloy (HSLA) steels and their relevance in today’s industries. The unique feature of HSLA steels is that they offer great strength and high mechanical properties without needing higher levels of carbon in the alloyed material. Thus, these steels are healthier from a structural and efficiency perspective and easier to weld and form.
To summarize, the following parameters are distinguishing features of HSLA steels:
- Strength-to-Weight Ratio
HSLA steels possess an exceptional strength to weight ratio which is advantageous since manufacturers can design components which are lighter yet stronger. This is useful in cases such as automotive frames or construction beams providing unmatched value.
- Tensile Strength
With a typical tensile strength of anywhere between 50 ksi up to 120 ksi (345 MPa to 830 MPa), HSLA steels are able to withstand harsh environments without permanently deforming or breaking,HSLA steels exihibit a very high tensile strnght.
- Corrosion Resistance
Due to inclusion of copper, chromium or nickel into their structure, most HSLA steels are designed with an added level of corrosion resistance. This ideal for use in applications which are directly exposed to the environment, for example bridges or pipelines.
- Formability
HSLA steels have excellent formability, which means they can be manufactured into many shapes and structures without cracking. This characteristic is very important for industries that need intricate or specifically tailored designs and parts.
- Weldability
Unlike high-carbon-content steels, HSLS steels have decent weldability. This feature decreases the chances of cracking or other defects during the fabrication process using welding techniques.
- Toughness
HSLA steels are suitable for low-temperature applications due to their toughness and impact resistance. Thus, they are a good choice for the energy, construction, and transportation industries.
Recognizing and utilizing these properties opens the door for the manufacture of durable, efficient, and cost-effective components, which HSLA steels enable. Their flexibility indeed makes them a powerhouse material throughout various industries.
Tool steel grades and their specialized uses
Each grade of tool steel is assigned to different applications depending on its properties. For instance, water-hardening (W-grade) steels are inexpensive and good for manufacturing basic chisels and knives. Air-hardening (A-grade) and high-speed (HSS) steels are used for very strong and precise cutting and drilling tools because of their strength and wear resistance. These tools are often found within the D series due to their high carbon and chromium content. On the other end, shock-resisting (S-grade) steels are used in the manufacturing of hammers and punches because they are designed to endure impact. Each grade is best suited for a particular application, which allows them to perform at their absolute best.
How to select the right grade of steel for specific applications?
The selection of an appropriate steel grade for a specific purpose always starts with evaluating the operating parameters of the tool or component. For example, in my situation, I first look at the material’s resistance to wear, impact, and the temperature it must endure. Regarding cutting tools, I recommend using M-grade high-speed steels owing to their strength and resistance to thermal damage. In my view, D-series steels are the most appropriate for dies or molds because of their high hardness and good wear resistance. For chisels or punches, my most significant recommendation would have to be S-grade steels because of their robust construction and excellent shock resistance. In final thoughts, the foremost objective of selecting the grade is balancing the steel properties with the task demands, cost constraints, and performance expectations.
Factors to consider when choosing between different types of steel
When selecting from various types of steel, the main considerations are the application, mechanical properties, cost productivity, and environmental impact. Measure hardness in conjunction with toughness, wear resistance, and ease of machining relative to the demands of the assignment. For example, high-carbon steels are ideal for cutting tools, while alloy steels are advantageous in extreme conditions. Always achieve a balance between performance and budget to ensure that the chosen steel is effective and durable.
Matching steel grades to hardness and corrosion resistance requirements
In terms of associating steel grades with requirements of hardness and corrosion resistance, I typically begin from the application’s requirements. For tasks that require very high hardness, for instance, cutting tools, I often recommend D2 or M2 tool steels, which have very high hardness and wear resistance. On the contrary, when resistance to corrosion is more important, I tend to prefer stainless steel grades, especially 304 or 316, because of their great usefulness in resisting humid or chemically heavy environments. For some alloys, such as 17-4 PH, balancing these often conflicting properties is possible but more demanding. My method is geared towards achieving optimal results with respect to the prevailing conditions and the duration of the activity.
Most widely used steel grades available in the market
Some of the common grades that are found on the market are 316 stainless steel, which is considered to be the best in marine and chemical environments, and 304 stainless steel which is corrosion resistant and is highly versatile. Carbon steel A36 is widely used in structural work owing to its high strength and low cost. Moreover, 4140 high-strength low-alloy steels are used in more rigorous engineering structures, and 17-4 PH comes out on top in cases involving high strength and great corrosion resistance.
Reference
- SAE steel grades on Wikipedia – Provides an overview of the SAE steel grading system and its standards.
- Types of Steel & Steel Grades Chart by Service Steel – Offers detailed classifications, usages, and a steel grade chart.
- Different SAE/AISI Grades of Steel by Industrial Metal Supply – Explains the SAE/AISI grading system and its applications.
Frequently Asked Questions (FAQs)
Q: What are the four main types of steel, and how do they differ?
A: The four main types of steel are carbon steel, alloy steel, stainless steel, and tool steel. Carbon steel contains varying amounts of carbon (typically 0.05% to 2.0%) and is commonly used for structural applications. Alloy steel contains additional elements like manganese, nickel, or chromium to enhance specific properties. Stainless steel is a type of steel that contains at least 10.5% chromium, providing excellent corrosion resistance. Tool steel is designed for cutting, forming, and other tooling applications. Each type offers different characteristics based on its chemical composition, making them suitable for various applications.
Q: How do I understand the types of stainless steel and their applications?
A: Understanding the types of stainless steel involves recognizing the five main categories: austenitic (300 series), ferritic (400 series), martensitic (400 series), duplex, and precipitation hardening. Austenitic stainless steel (like 304 and 316) offers excellent corrosion resistance and is commonly used in kitchen equipment and medical devices. Ferritic stainless steels are magnetic and have good formability, and are used in automotive and household appliances. Martensitic stainless steels can be heat-treated for hardness, making them ideal for knives and surgical instruments. Duplex stainless steels combine properties of austenitic and ferritic types, while precipitation hardening grades offer extremely high strength. Selecting the right stainless steel depends on the specific application requirements, such as corrosion resistance, strength, and fabrication needs.
Q: What is low-carbon steel, and what are its applications?
A: Low carbon steel (also called mild carbon steel) contains 0.05% to 0.25% carbon content and is one of the most common grades of steel available. It offers excellent formability, weldability, and ductility while being relatively inexpensive. Due to these properties, low-carbon steel is commonly used in automotive body panels, structural shapes, pipes, building materials, and consumer products. While it doesn’t offer the strength of higher carbon steels, its workability makes it ideal for applications that require forming and joining operations. Many types of steel products in everyday use, from paperclips to car bodies, are made from low-carbon steel.
Q: How does the SAE grading system work for carbon and alloy steel?
A: The SAE (Society of Automotive Engineers) grading system for carbon and alloy steel uses a four-digit numerical code to classify steel based on its chemical composition. The first digit indicates the major alloying element: 1xxx for carbon steel, 2xxx for nickel steel, 3xxx for nickel-chromium steel, etc. The second digit specifies the secondary alloying element concentration. The last two digits indicate the carbon content in hundredths of a percent. For example, SAE 1018 is a carbon steel with 0.18% carbon, while SAE 4140 is a chromium-molybdenum alloy steel. These SAE grades are used extensively in the automotive and manufacturing industries to ensure consistent material properties and performance across steel production.
Q: What is the difference between carbon steel and alloy steel?
A: The main difference between carbon steel and alloy steel lies in their composition and resulting properties. Carbon steel is primarily composed of iron and carbon, with the amount of carbon directly affecting its hardness and strength. Steel is graded as low (up to 0.3%), medium (0.3-0.6%), or high carbon (0.6-1.0%). Alloy steel, however, contains additional elements beyond carbon, such as nickel, chromium, molybdenum, or vanadium, introduced in specific amounts to enhance particular properties like corrosion resistance, hardness, or toughness. While carbon steel is often less expensive and commonly used for general applications, alloy steel offers superior performance in specialized applications that require specific mechanical or physical properties.
Q: How do I use an SAE steel grade chart when selecting the right steel for my project?
A: When selecting the right steel for your project using an SAE steel grade chart, first identify your application requirements (strength, hardness, corrosion resistance, machinability, etc.). Then, locate the corresponding SAE grade on the chart that meets these requirements. The four-digit SAE codes (like 1045 or 4130) provide information about the steel composition—the first digit indicates the major alloying element, while the last two digits show the carbon content. For example, if you need steel for structural components that require good weldability, you might select a 1018 steel. For high-stress applications requiring better strength and toughness, a 4140 alloy steel might be appropriate. The chart will also show typical mechanical properties, heat treatment responses, and common applications for each grade, helping you make an informed decision.
Q: What factors affect steel production and quality?
A: Steel production and quality are affected by numerous factors throughout the manufacturing process. Raw material selection, including the purity of iron ore and the types and amounts of alloying elements, establishes the foundation for steel quality. The steelmaking method (basic oxygen furnace, electric arc furnace, or specialty processes) influences the final properties. Temperature control during melting, refining, and casting is critical for achieving the desired microstructure. The cooling rate and subsequent heat treatments determine mechanical properties like hardness and strength. Modern steel production also involves precise chemistry control, deoxidation processes, and impurity removal. Additional processing, like hot or cold rolling, forging, or drawing, further develops the steel’s properties. Quality control measures, including spectrographic analysis and mechanical testing, ensure the steel meets specified SAE grades and industry standards.
Q: How do I interpret the carbon content in different steel grades?
A: Interpreting carbon content in different steel grades is essential as it’s the primary determinant of steel’s mechanical properties. In the SAE system, the last two digits of the four-digit code represent the carbon content in hundredths of a percent (e.g., 1045 contains approximately 0.45% carbon). Generally, as carbon content increases, steel becomes harder and stronger but less ductile and more difficult to weld. Low carbon steel (0.05-0.25%) offers excellent formability and weldability for structural applications. Medium carbon steel (0.30-0.60%) provides a balance of strength and toughness for machinery parts. High carbon steel (0.60-1.00%) delivers superior hardness and wear resistance for tools and cutting implements. Ultra-high carbon steel (1.0-2.0%) is used for specialized applications like knives and springs. When selecting steel based on its chemical composition, consider that higher carbon content typically requires more careful heat treatment and welding procedures.
Q: What is the comprehensive guide to steel alloy designations?
A: A comprehensive guide to steel alloy designations includes understanding several classification systems beyond just SAE. The AISI (American Iron and Steel Institute) system parallels SAE but covers a broader range of steels. The UNS (Unified Numbering System) provides a more detailed alphanumeric code. For stainless steel, the 300 and 400 series designations indicate austenitic and ferritic/martensitic types, respectively. Tool steels use letter prefixes (A, D, H, etc.) to indicate their application or key properties. European standards use different systems, like EN or DIN. When working with international suppliers, it’s important to recognize equivalent grades across different standards. For example, SAE 1045 is similar to DIN C45 and JIS S45C. The guide to steel designations should also include understanding the naming conventions for special property steels like HSLA (High-Strength Low-Alloy), weathering steel (like COR-TEN), and other specialized grades used in specific industries.
Q: How can I determine which steel grade is best for high-temperature applications?
A: For high-temperature applications, selecting the right steel grade requires evaluating several key factors. First, consider the operating temperature range, as different steels maintain their properties at different temperatures. For moderate heat (up to 500°F/260°C), carbon or low-alloy steels may suffice. For higher temperatures, specialized stainless steel or heat-resistant alloy steel grades are necessary. Austenitic stainless steels like 304 and 316 maintain strength and corrosion resistance up to about 1600°F (870°C). For even higher temperatures, grades containing higher chromium and nickel content, like 309, 310, or heat-resistant alloys like Inconel, might be required. Consider factors like oxidation resistance, thermal expansion, creep resistance, and thermal fatigue. The SAE grades don’t specifically address high-temperature performance, so you’ll often need to reference ASTM specifications for heat-resistant steels. Consultation with metallurgical experts is recommended when selecting steel for critical high-temperature applications.