The rectangular stainless steel tubing is highly sought after in a variety of industries due to its strength and durability, along with its aesthetically pleasing look. Its applications span construction and architecture through to automotive and other industrial usages. That said, knowing the manufacturing procedures, important criteria, as well as the dimensional parameters for the tubing is important for correctly sourcing and using the material. In this blog, we will detail the entire process of manufacturing stainless steel rectangular tubing, discussing the primary criteria and the standards of performance and quality assurance. It does not matter if you are a professional or a novice; this guide should suffice to assist you in your projects and applications.
What Is the Basic Manufacturing Process for Stainless Steel Rectangular Tubing?
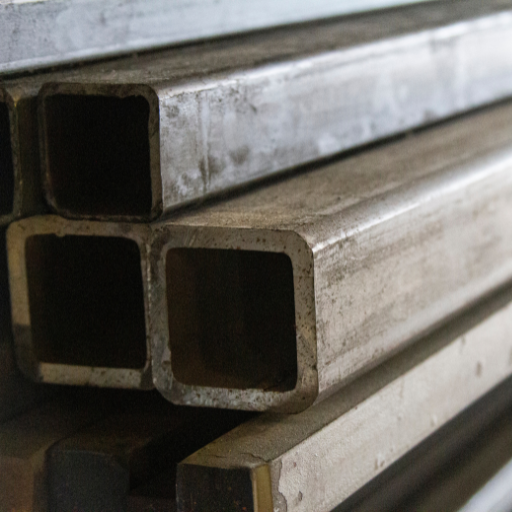
To guarantee strength, toughness, and precision, the basic manufacturing process for stainless steel rectangular tubing involves the following steps.
- Raw Material Preparation: Based on the desired grade and thickness, the appropriate stainless steel sheets or coils are selected.
- Forming: To shape the material into a rectangular tube, it is fed through rollers that rectify alignment and dimension.
- Welding: High-frequency welding, among other methods, is used to join the edges of the steel tube together as weld seams to complete the clean structure.
- Sizing and Straightening: Through additional rollers, the welded tube is passed to fine-tune the straightness and dimensions of the tube.
- Cutting: The tubing is cut according to the different needs.
- Finishing: The final product goes through a polishing step, cleaning, inspecting for any inconsistencies, and treating it, whether it needs to be oxidized or not.
Using the above processes, high-quality stainless steel rectangular tubing that is durable and ideal for multiple uses can be made.
Raw Material Selection and Preparation of Stainless Steel Alloy
Choosing raw materials is a fundamental stage to ensure that stainless steel alloys maintain their quality and durability. The basic constituents are iron, chromium, nickel, and occasionally molybdenum, manganese, or nitrogen, based on the further applications of the alloy. The amount of chromium alloyed, which is frequently between 10.5% and 30%, is necessary because it forms a protective oxide layer on the surface of the metal and thus provides corrosion resistance. The addition of nickel improves ductility and toughness, and molybdenum enhances resistance to pitting and crevice corrosion.
After the raw materials are chosen, they are weighed and put together in appropriate proportions before being placed in an electric arc furnace (EAF) for melting. This part of the process can extend for 12 hours and requires that a temperature surpassing 2,500°F (1,370°C) is attained to achieve a uniform melt. Impurities and excess carbon are removed during a refining step such as argon oxygen decarburization (AOD), which improves the alloy’s chemical composition along with its mechanical properties.
The next step is to cast the liquid stainless steel into slabs, billets, or blooms, which are cooled and conditioned for the next steps. During this stage of production, advanced technologies like spectrometers and devices of X-ray fluorescence are often used to check the alloy’s chemical composition and uniformity. With careful control of material preparation processes, manufacturers can produce stainless steel that complies with precise industrial requirements and standards for a wide variety of uses.
Forming Techniques for Rectangular Stainless Steel Tube
Achieving efficiency in quality and craftsmanship while forming rectangular stainless steel tubes requires the use of various advanced forming techniques. One such technique is roll forming, which ensures accuracy while maintaining a brisk pace. During roll forming, strips of stainless steel are shaped by being gradually fed through intricate rolls.
Extrusion is another technique used for lower-quality tubes. Here, stainless steel is heated and forced through a die with a rectangular aperture, which forms a seamless tube. Since there are fewer steps after forming, this method is commonly chosen for seamless tubes.
For applications where precision of the shape and thin wall thickness is paramount, hydroforming is employed. In this case, a steel tube is sealed in a die, and the cylinder is filled with hydraulic fluid, which molds it to the shape of the die while equally maintaining the wall thickness.
An industry report stated that circular stainless steel tubing is now easier to fabricate due to modern approaches like laser welding that improve weld accuracy along with corrosion resistance. These technologies, in combination with strict quality control, enable manufacturers to satisfy the construction, automotive, and aerospace industries that require dependability.
Welding and Seam Finishing in Stainless Steel Tubing Production
Welding ensures the needed strength and integrity of stainless steel tubing. Industry standards now include more advanced practices, such as TIG (Tungsten Inert Gas) welding and laser welding, because of their exactness in making robust and smooth joints. An example is that TIG welding is highly acclaimed due to its capacity to create strong welds while minimizing warping, which is important for parts that need precise measurements and aesthetically pleasing surfaces.
The quality of the tube is now further enhanced with the addition of the polished finish, which is accomplished through the pickling method. Pickling not only removes any remaining dirt but also corrosion, enhancing the surface quality of the tubing. Other industries, such as food and drug processing, will find the tubing useful because it has improved cleanliness and reduced corrosion capabilities alongside durability and visual appeal.
Further productivity and precision have been gained from automating certain welding and finishing processes. Now, countless products can be manufactured using the same automation factors without sacrificing quality and meeting certification standards such as ASTM and ISO. Early defect detection through real-time monitoring with automated systems greatly lessens material waste while increasing overall quality.
What Are the Different Production Methods for Stainless Steel Rectangular Tubes?
The creation of stainless steel rectangular tubes utilizes two main techniques:
- Seamless Tubing: Stainless steel is shaped into tubes without any seams. This approach provides a smooth and polished appearance, ensuring uniform strength, which is ideal for high-pressure conditions.
- Welded Tubing: A flat strip of stainless steel is rolled, and the edges are welded together. This method is popular for being cheaper, and its strength is limited only to low-pressure applications.
Both methods aim to satisfy the requirements placed in the industry while ensuring precision, resilience, and repeated excellence.
Cold Forming vs. Hot Forming of Stainless Steel Rectangular Tubing
The processes of cold forming and hot forming are two ways to shape stainless steel rectangular tubing, each with its benefits. In my understanding, cold forming is when the steel is shaped at room temperature, which results in better surface quality and dimensional accuracy. This process is best suited for applications where the aesthetics need to be visually pleasing and the tolerances need to be tight. In contrast, hot forming entails bringing the steel to high temperatures, which allows for easier shaping and making more intricate shapes. This method is commonly used for bigger pieces of tubing or when high ductility is required. Each option has its advantages, but one must choose based on the precision and strength needed for the specific application, and the cost considerations.
Seamless vs. Welded Stainless Steel Tube Manufacturing
The different methods of manufacturing seamless and welded stainless steel tubes have their respective benefits, which are considered about the requirements of specific applications. For creating seamless stainless steel tubes, a solid cylindrical billet undergoes a piercing to form a hollow. This results in a tubular piece without a longitudinal weld seam and therefore, is much stronger and more reliable when under pressure and extreme temperatures. Seamless tubes are used for critical applications in aerospace, oil and gas, and power generation industries due to their reliability and performance.
Welded tubes, on the other hand, are made by rolling flat steel sheets into cylindrical shapes and welding the seams flat. Then, the welds along each seam are welded both circumferentially and longitudinally. Advanced techniques utilize modern welding, with laser welding being one example that minimizes the joint’s weakness. As a result of these processes, welded tubes are cost-effective and efficient for numerous applications. Tubes that are welded can be made in greater quantities and to specific sizes, which makes them suitable for the construction and automotive industries.
New technologies used in manufacturing recently have dramatically improved the quality of welded tubes, making them closer in quality to seamless tubes. Industry estimates indicate that seamless tubes are more expensive to produce, although they provide unrivaled strength, while versatile welded tubes are inexpensive and lack precision for use in critical applications.
Specialized Production Techniques for Structural Tubing Applications
Reliability and performance in structural tubing need precise techniques due to the various applications in which they are used. Below are some important production techniques that are specialized:
1、Electric Resistance Welding (ERW)
This technique is widely adopted for the production of welded tubes. The edges of the tube are heated using a high-frequency electric current, causing a weld to be formed as it is pressed together.
- Advantages: ERW is economically friendly, has a quick rate of production, and provides the ability to produce tubes with uniform wall thickness.
- Applications: Lightweight structural supports, construction scaffolding, and automotive frames.
2、Seamless Tube Extrusion:
A solid billet of steel is heated and pierced to form a hollow tube without any welds to create seamless tubes.
- Advantages: These types of tubes are superior in strength, high temperature, and pressure resistance.
- Applications: High-pressure hydraulic cylinders, gas and oil tubing, and boiler systems.
3、Cold Drawing Process:
The tube is pulled through a die in this technique to reduce the diameter and enhance mechanical properties, surface finish.
- Advantages: An enhanced surface finish along tighter dimensional accuracy are attained.
- Applications: Components in medical and aerospace devices.
4、Hot Rolling:
Hot rolling occurs at high temperatures to quickly shape and create large quantities of tubing. Trimmed rolled bars are calibrated for final dimensions.
- Advantages: Production efficiency is better, and costs are lower in comparison to cold drawing and seamless methods.
- Applications: Construction beams, industrial machines, and other large-scale industrial infrastructure.
5、Laser Welding Systems:
A modern and very accurate method for welding is laser welding; it produces strong, clean weld seams.
- Advantage: Extreme accuracy, little heat displacement, and the joining of materials that are different from each other.
- Applications: Automotive tubing and architectural components with performance requirements.
6、Heat Treatment and Annealing:
This process uses heat and controlled cooling cycles to increase the ductility and hardness of materials, enhancing mechanical properties.
- Advantages: Enhances the structural integrity and prolongs the service life of the tubing.
- Applications: Heavy-duty parts in industrial equipment and military-grade equipment.
These techniques of production make sure that structural tubing fulfills or exceeds the standards of modern industries while balancing performance, cost, and material efficiency.
What Steel Rectangular Tube Standard Sizes and Specifications Are Available?
Steel rectangular tubes come in numerous standard sizes to accommodate different applications. A common dimension might be 1”x1/2” to 24”x12” with a wall thickness ranging from 0.065” to 0.5” . Typically, lengths are sold in 20-foot or 24-foot sections. However, custom lengths may be possible. In addition, these tubes are more often than not manufactured by ASTM standards, such as with structural tubing ASTM A500, which guarantees a certain level of quality, accuracy, and strength. It is critical to verify the exact size and specification details with the supplier or manufacturer for some applications.
Common Wall Thickness and Dimensional Standards
The wall thickness and size parameters for structural tubing are generally divided into groups for specific purposes. Common wall thicknesses include 0.065”, 0.083,” 0.120,” and 0.188.” Depending on their purpose, tubes usually come in square, rectangular, or circular shapes with sides from 0.5” up to several inches. ASTM A500, ASTM A513, and ASTM A1085 set certain limits and requirements on the mechanical and chemical features of the aforementioned articles as well as their precision measures, and provide qualitative and quantitative standards for measuring mechanical features. The standards guarantee the design of the tubing so it will perform and endure structural loads, environmental conditions, and other stresses in special applications.
Differences Between 304, 316, and 316L Stainless Steel Rectangular Tubing
Stainless steel rectangular tubing is prized for its strength, durability, and resistance to corrosion. Picking the right grade, however, depends on the specifics of the application. The most commonly compared grades are 304, 316, and 316L, each having distinct characteristics.
304 stainless steel grade is the most economical and one that is used the most. It has 18% chromium and 8% nickel, giving it great support for corrosion in many conditions. Although 304 does poorly with chlorides and saline environments because it is susceptible to pitting and crevice corrosion over time.
316 stainless steel has greater percentages of nickel as well as an additional 2-3% molybdenum, making it superbly resistant to chloride and harsher conditions. This makes it ideal for marine applications or areas exposed to chemicals and saltwater. Also, 316 stainless steel has much better tensile strength than 304.
316L stainless steel is a low-carbon version of 316 and is designed with greater weldability. The lower carbon content reduces the risk of carbide precipitation during welding which better retains the material’s integrity and performance in stress-prone applications.
While choosing among these grades, pay attention to factors like exposure to corrosion, needed strength, cost, and if welding takes place in the assembling process. Generally, for saline or chemical-laden settings, 316 and 316L are favored due to their durability and added resistance.
What Post-Production Processes Are Applied to Stainless Steel Rectangular Tubing?
Every post-production step taken on stainless steel rectangular tubing serves to improve its quality and functionality:
- Polishing – The surface of the tubing is polished for aesthetic value. Additionally, it aids in the cleaning and maintenance of hygiene for specific applications.
- Passivation – The surface of the tubing is free of contaminants, as well as having enhanced natural electrochemical corrosion resistance due to the protective oxide layer formed by this chemical treatment.
- Cutting and Sizing – The tubing is pulled to length on a saw to meet the project’s specific needs, thus meeting precision and repeatability expectations.
- Heat Treatment – This procedure may be performed on a material to relieve stress or enhance strength, depending on the end use, along with other material properties.
- Inspection and Testing – Tubing is verified with inspections of all dimensions and tests of mechanical properties to ensure compliance with industry standards.
Surface Finish Options for Stainless Steel Tubes: Polished, Brushed, and Architectural Finishes
The stainless steel tubes come in a polished and matt finish to help serve various functions, and are polished to suit the intended use.
1、A Polished Finish
A polished finish results in a shiny surface, which improves the nature and beauty of the stainless steel tubes. This kind of polish is obtained through a mechanical polish, and it is common in the food processing and healthcare industries. In addition to being smooth, polished surfaces are clean and remain hygienic, and can be easily cleaned. Another benefit of polished stainless steel is that it is very durable and resists corrosion, making it ideal for severe conditions. Finishing is usually done according to the size of the grit, and a fine polish gives a greater level of visibility.
2、Re-Brushed Strain
By use of the abrasive method of line creation, stainless steel tubes are brushed, and their appearance becomes devoid of shine. This finish is useful where sleek, understated looks are a priority, like in the interiors of buildings and automobiles, and in appliances. The sheen-free brushed stainless steel tubes strike a good elegance-practicality balance because they disguise scratches and fingerprints effectively and resist corrosion well.
3、Architectural Finishing
This type of finishing features a number of distinct procedures, including polishing, mark-cutting, and sandblasting, to create distinct satin, embossed, or bead-blasted patterns. Such finishes are sometimes commissioned as part of high-profile design works for commercial buildings, airports, and other public places that require a lot of attention. Bespoke architectural-grade stainless steel adds a visual purpose and functionality to the construction because it is highly durable and still distinctly designed.
Knowing these surface finish selections aids designers and engineers in choosing the proper stainless steel tubes aligned with the requirements of the project in terms of performance and design.
Heat Treatment and Its Effect on Stainless Steel Properties
Heat treatment impacts the mechanical and physical properties of stainless steels. These treatments are critical processes in the manufacturing process. The heating and cooling cycles must be done according to specifications to achieve desired standards that include strength, hardness, ductility, and the ability to withstand corrosion.
One of the commonly used heat treatment processes is annealing. This process involves heating and then cooling at a controllable rate to attain desired values. This aids in relieving internal stresses and improving ductility.
Quenching and tempering is another common technique, especially for martensitic stainless steels. Quenching involves an increase in the cooling rate post-heating, which proves useful in achieving high levels of hardness and strength. This process comes with the drawback of reduced toughness. To counteract this, tempering aims to achieve the optimal balance of strength and brittleness.
The process applies to other metals too, but is known as Precipitation hardening. This process concentrates on a few particular grades, like 17-4 PH. This process is ideal for military and high-performance needs as it is specifically focused on creating small, dispersed particles that improve strength and toughness while maintaining corrosion-resistant features.
The heat treatment process needs to be customized for each stainless steel grade and model. Specifics like temperature and timing must be closely monitored to match a desired outcome. The introduction of modern technology gives one the ability to accurately control monitoring during heat treatment, consistent results are now attainable.
Control of heat effects enables engineers to create more robust stainless steel designs tailored to the specific operational environments.
Cutting and Custom Fabrication Services from Tube Suppliers
Tube suppliers now provide state-of-the-art cutting and custom fabrication services to address various industrial sectors. These services encompass cutting, bending, welding, and machining to ensure the parts made from stainless steel are manufactured to precise tolerances. Often, advanced industrial tools such as laser cutters and CNC machines are used because of their precise cutting and operational speed. Moreover, quality control and lead time efficiency are enhanced due to automation and real-time analysis of data during fabrication.
Increased demand for custom stainless steel tubing fabrications has recently been observed for medical devices, automotive, and aerospace industries. The increasing adoption of these industries is attributed to high performance standards for corrosion resistance and durability. Industry tube suppliers also offer material certification and testing documentation to aid in stringent industry regulation compliance, guaranteeing that all customized components are made to required standards. These innovations in fabrication add to the ability of modern engineering applications, increasing precision, reliability, and creativity.
How Does the Manufacturing Process Affect the Final Properties of Stainless Steel Rectangular Tubes?
The final characteristics of stainless steel rectangular tubes are greatly affected by the manufacturing process. The processes of cold drawing and welding affect the strength, accuracy, and finish of the tube. Annealing and other heat treatments improve the durability of the tube, decrease internal stress, and enhance the mechanical load capacity of the tube. Moreover, quality assurance performed during the fabrication process guarantees consistent thickness and corrosion resistance. Meeting the performance and reliability standards for different applications is accomplished by optimizing each step of the process.
Impact of Production Methods on Superior Corrosion Resistance
The advancement of technologies to meet industry needs has led UTG to considerably enhance the development of corrosion-resistant materials. Alloying methods that involve adding chromium, nickel, and molybdenum to base metals are one such example. These alloys form an oxide layer on the material’s surface, which reduces the rate of corrosion significantly, even in heavily corrosive environments such as the marine or chemical industries.
Surface treatment, especially electroplating and passivation, is another important technique. These procedures add to a material’s resistance to corrosive agents by forming a strong, uniform barrier. Passivated stainless steel can, for example, achieve a lifespan increase of 10 times that of untreated ones.
Moreover, high accuracy in manufacturing processes like laser welding and automated additive manufacturing has achieved uniform finishing quality. These processes improve the overall quality of the product by reducing defects and inclusion, which are corrosion initiation points, and improve the overall reliability and durability of the product.
A recent study claims the use of such technologies in industrial applications can lower maintenance costs by as much as 25 percent due to increased longevity of the corrosion-resistant parts. This reliability is crucial for industries such as gasoline or jet fuel energy structures, transport systems, and even medical apparatuses, which need modern production methods for enhanced focus and precision.
How Manufacturing Techniques Influence Durability and Strength
Changes in the technologies used in the industries have reopened the possibilities and flexibility towards the strength and materials used in construction buildings, products, etc. Tailor-made material properties are now possible to achieve with modern techniques like additive manufacturing, which most people know as 3D printing, precision machining, and also with more sophisticated heat treatments. For example, the use of composites in aerospace engineering makes it possible to increase the weight and fuel efficiency of the aircraft, thus improving the performance. Likewise, the development of high-strength steel and titanium alloys gives rise to new components that can withstand extreme wear and tear. There is evidence indicating that organizations adopting modern production technologies experience a steady decline in material failure and downtime, enhancing efficiency, resources, and cost savings in the long run, all while improving safety standards. Integrating these new techniques into the manufacturing processes further enhances the durability and strength of existing materials and showcases the innovative capabilities of these developments.
Reference Sources
- “Advances in Orthodontic Archwires”:
-
- This paper primarily focuses on advancements in orthodontic wire alloys, including stainless steel. It discusses the evolution of materials like nickel-titanium and beta-titanium, which have replaced stainless steel in some applications due to their superior properties. While not directly about tubing, it highlights the mechanical properties and applications of stainless steel in medical contexts.
- “A Novel Strategy for Landslide Displacement and Its Direction Monitoring”:
-
- This study explores the use of capillary stainless steel pipes in optical fiber transducers for landslide monitoring. It details the manufacturing and testing of these pipes, emphasizing their integration with optical fibers. The research provides insights into the precision and dynamic range of stainless steel components under stress, which could be relevant for understanding material behavior in tubing applications.
- “Manufacturing and Testing of Welded Stainless Steel Tubing: You Have a Choice”:
-
- This paper discusses various manufacturing methods for stainless steel tubing, including welding, cold working, and heat treating. It evaluates the advantages and disadvantages of these methods and provides recommendations for ensuring high-quality tubing for critical applications like power plants. Although published earlier, it remains a valuable resource for understanding the manufacturing process.
Frequently Asked Questions (FAQs)
Q: What is the stainless steel rectangular tube standard used in manufacturing?
A: The main stainless steel rectangular tube standard is ASTM A554, which encompasses welded decorative and structural stainless steel mechanical tubing. Other noteworthy standards are ASTM A269/A270 for general service applications and ASTM A312 for high temperature service. These standards establish the chemical and mechanical characteristics, as well as the tests and limits of industrial scrutiny, quality of measurement, and precision required for stainless rectangular tubes used in industrial work. The a554 stainless steel rectangular standard is particularly valuable since it deals with both decorative and structural applications in various environments.
Q: How is a stainless rectangular tube manufactured?
A: The process of manufacturing stainless rectangular tube begins with flat strips of stainless steel, which are roll-formed into a rectangular shape. The seam is then welded (commonly using TIG or laser welding for quality reasons). After the welding process, the tube goes through an annealing furnace to remove the stress and reclaim the corrosion resistance that was weakened during the welding process. The tubes are then quenched and go through sizing rolls for accurate measurement. They are finally prepared for surface treatments such as polishing or brushed finish, as required. This process yields rectangular tube stainless steel products that retain their strength and, at the same time, boast excellent corrosion resistance for architectural, decorative, harsh industrial, and marine applications.
Q: What are the common sizes available for rectangular tube stainless steel?
A: Rectangular tube stainless steel is normally offered in widths from 10mm up to 400mm, heights from 20mm to 200mm, and wall thicknesses from 0.5mm to 12mm. Standard length is most often 6m (20ft) or 12m (40ft), but can be ordered in cut lengths from a steel tube supplier. Stainless steels are most commonly used are 304 stainless steel for general use and 316 stainless steel for more aggressive corrosive environments. The selection of size should consider the mechanical properties that should be tailored to specific structural applications, load-bearing requirements, and environmental factors the tubing will encounter.
Q: How is rectangular structural stainless tubing distinct from Steel Pipe or Steel Square Tubing?
A: The difference between rectangular structural stainless tubing and steel pipe is their shape and use. Steel pipe is round and has a constant inner and outer diameter, which is measured by nominal pipe size (NPS). Steel pipe is mostly used for transporting fluids. Rectangular tube has a rectangular cross-section and different width and height dimensions, making it ideal for structural use. Unlike steel square tubing, which has equal sides, rectangular tubing has different moments of inertia about each axis. This gives engineers more flexibility when designing. Furthermore, stainless steel rectangular tubing has far greater resistance to corrosion compared to carbon steel pipe or square tube. This makes it ideal for harsh environments where carbon steel would suffer.
Q: What mechanical properties should be assessed when choosing stainless steel rectangular tubing?
A: While choosing a stainless steel rectangular tubing, the mechanical attributes one has to bear in mind include tensile strength (which is usually between 515-860 MPa depending on the grade), yield strength (205-515 MPa), elongation (40-60% for austenitic grades), and hardness. Different grades of stainless steel rectangular tubing have different orders of corrosion resistance, with 316 having better resistance to the marine environment than 304. Other considerations include fatigue strength for cyclical loading applications, impact strength where mechanical shock occurs, and temperature resistance for high-temperature applications. The mechanical strengths of stainless steel tubing are further modified by the cold working processes during manufacturing, which enhance strength but reduce ductility.
Q: What are the primary uses of stainless rectangular tubes in different industries?
A: The industrial uses of stainless rectangular tube are numerous and include: manufacturing food processing equipment, components for chemical processing plants, automotive exhaust systems, structural components of ships and handrails, architectural features of buildings, frames for medical equipment, machines for commercial kitchens, components for water treatment plants, and fabricating heat exchangers. Selecting the specific grade of stainless steel depends on 304 being common for general purposes and 316 for harsher conditions. The application of rectangular structural tubing across these varying industrial surroundings highlights its versatility.