Electropolishing and electroplating are two processes that come into focus when improving the properties of metal surfaces, especially stainless steel. Both techniques use electricity in some form, but they do not share the same goals, and their results vary greatly. For the medical device sector or in aerospace industries, where accuracy, longevity, and surface finish are critical, understanding these distinctions is important. This article explores electropolishing and electroplating with respect to their science and practical application, including what drives each process, what benefits and disadvantages they offer, as well as optimum use cases. From improving resistance to corrosion, achieving a mirror finish, or protective coating, this guide offers the right approach for all requirements. Let’s look into the amazing changes these processes can achieve for metals.
What Are The Key Differences Between Electropolishing And Electroplating?
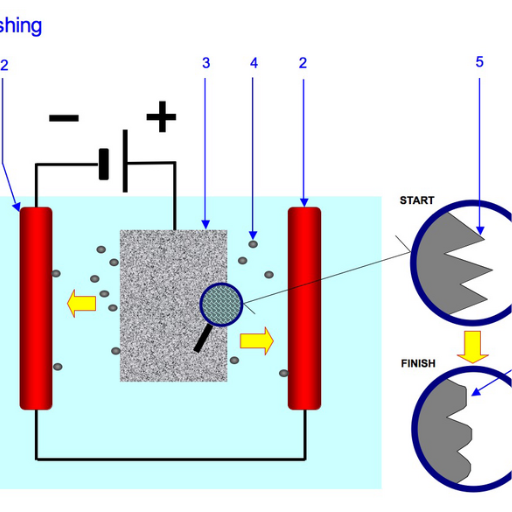
Even though all processes involve the application of electricity and the use of chemicals, electroplishing and electroplating have distinct characteristics and outcomes due to each process’s unique purpose:
- Electropolishing removes material from the surface of a piece of metal to achieve a smoother, more polished finish. This results in less corrosion, a decrease in porousness, and an overall cleaner object.
-
Whereas, Electroplating adds a coat of metal to a surface of an object. The purpose of this technique is to improve ornamental appeal, durability, and protection from deterioration.
The distinction is in their intended results: in electropolishing the material is removed for surface refinement, in electroplating the surface is changed or improved by adding material.
How Electropolishing Removes Material While Electroplating Adds Material
Electropolishing is a technique that uses an electrochemical reaction to precisely remove material from a surface. This process results in exceptionally smooth surfaces by selectively dissolving the peaks of surface irregularities. The use of an electrolyte bath and direct current to control the rate of material removal is crucial to accomplish this. Electropolishing is critical in the medical device and aerospace industries because of its ability to increase cleanliness, reduce corrosion, and improve surface aesthetics.
Electroplating, on the other hand, focuses on adding a layer of metal onto a substrate surface to improve its characteristics and, visually, its appeal. In this process, the object serves as the cathode in an electrolyte solution that contains metal ions. After electricity is introduced to the solution, metal ions are reduced and bond to the surface of the object, resulting in a seamless and thick coating. Electroplating enhances features like wear resistance, conductivity, and aesthetics. For instance, nickel and chrome plating are popular for their use in automotive and hardware applications, whereas gold and silver plating are often used in electronics and jewelry.
The use of these techniques is highlighted with overwhelming market stats provided by research data. The medical industry uses these services/technical work the most due to market electropolishing investments, which go as high as billions. Likewise, it is estimated that the electroplating market’s value will surpass $20 billion by 2030 due to the overt nature of the electronics, automotive, and aerospace sectors. Each of them has undeniable significance within modern production and is adapted for various functional and visual purposes.
Comparing Surface Finish Results: Electropolishing vs Electroplating
Surface Finish and Appearance
Every surface finish approach comes with its pros and cons. For instance, polishing is best for attaining electropolishing as it offers a bright and gleaming finish. The process also enhances corrosion resistance, making the item more durable and suitable for use in healthcare settings. This technique is used in many different industries, including medicine, hospitality, and semiconductor fabrication, because it fulfills industry sterility standards.
In automatic plating, a base layer is placed over another layer. While updating a surface, it is also Versatile in nature also can be used for masking, can improve the look by stamping, scraping, and printing to change voltage. In car manufacturing, these parts are really economical and light, so they are plated and made robust.
Surface Roughness and Precision
As far as surface finish and precision are concerned, electropolishing as a method outperforming others achieves lesser roughness average (Ra) values. Studies show that electropolishing has the potential of reducing Ra values by almost 50%, providing extremely smooth surfaces needed where particle deposition or contamination poses problems. For example, stainless steel parts for a medical setting are often electropolished to reduce bacterial retention and facilitate cleaning.
As with other treatments, electroplating improves some surface characteristics by adding coatings. Regarding roughness, there is no significant improvement—rather, it tends to reproduce or slightly cover the surface features of the underlying material. Furthermore, the coating thickness has to be limited in order not to modify the structural dimensions which, in highly precise applications, can be challenging.
Longevity and Corrosion Resistance
Corrosion resistance is enhanced due to the removal of surface imperfections, improvement of the chromium oxide layer, and excellent finishing achieved through polishing on electropolished parts. The smooth texture of the polished components prevents pitting and moisture retention even in extreme chemical and marine environments.
On the other hand, the protection against corrosion on electroplated surfaces is dependent on the added metal layer. Some plating materials, like nickel and chromium, can offer good barrier effectiveness, but they are prone to cracking and wear over time. Increased maintenance schedules and re-plating may be necessary to keep performance standards in severely corrosive conditions.
Why Electropolishing Is An Electrochemical Process That Differs From Plating
Electropolishing and plating are two distinct processes that differ in their techniques and objectives. With regard to polishing, it is done by an electrolytic removal from the surface of some metal part, which is the surface of a metal object electrochemically dissolved. It is done to improve surface finish by smoothing out microscopic irregularities, reducing roughness, and increasing resistance to pitting corrosion. The operation requires a direct electrical current and uses a mixture of acids and other chemicals as electrolytes to dissolve and remove the waste away placed to atoms.
With plating, there is always deposition of material like nickel, gold, or chromium on surfaces using electrical current. Electropolishing is additive in betterment aspects like aesthetics, wear and tear resistance, or corrosion resistance. Latest independent researches show that surfaces subjected to obesity polishing could achieve as low as Ra roughness 0.1 µm, which is why these surfaces are sought after by the medical, aerospace, and food processing industries that require extreme hygiene and sterilization.
Additionally, in critical industries, the lack of surface material addition during electropolishing helps reduce the contamination risk. This is not the case with plated coatings, which have a high tendency to cause damage such as cracking, peeling, or unsteady deposition that can compromise long-term performance. Moreover, data indicates that corrosion resistance can be improved by 30% with electropolishing due to the removal of inclusions that may trigger corrosion. These differences in performance and functionality are the mesoscale reasons that explain why precision and reliability in advanced applications depend on electropolishing.
How Does The Electropolishing Process Work?
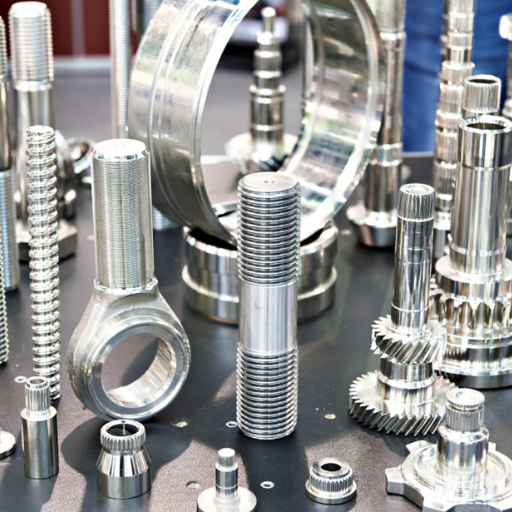
Electropolishing describes a process that uses electrochemistry to remove a fine layer from the surface of a metal part. The metal component is placed into a chemical bath while an electric current is introduced. This current results in the selective dissolution of surface cavities such as roughness or burrs, leaving behind a clean and polished surface. In addition to smoothing the surface, this process improves its resistance to corrosion and provides a consistent finish, which is perfect for tasks needing extreme accuracy and sanitation.
Understanding The Electrochemical Process Behind Electropolishing
The mechanism behind electropolishing is based on anodic dissolution. This is where the workpiece serves as the anode within an electrochemical cell. This procedure is useful for removing tiny microscopic material from the surface because it creates a mirror polish and improves the functionality of the component as a whole. Normally, a mixture of sulfuric acid and phosphoric acid is used as the electrolyte and in concentrated acid solutions. The current density that is passed through the metal also has to be controlled between 10 and 50 amps per square decimeter, depending on the metal and finish required.
The most recent developments in electropolishing focus on optimizing the precision and efficiency of the process. Some examples include new changes in automated control systems that enable monitoring and altering the voltage, temperature, and acid concentration. Modern data also shows that contemporary methods of electropolishing are able to achieve a surface roughness value of 0.1 micrometers Ra. This shows the relevance it holds in the aerospace, medical device, and semiconductor industries. In addition, the technique also reduces the micro stress concentration on the metal, making it more fatigue resistant.
Notably, beyond the economic factors, the use of ecologically sustainable practices has advanced the development of sustainable electrolytes and waste minimization strategies. Research claims that the implementation of non-toxic additives within the electrolytes provides meeting performance objectives while minimizing environmental impacts. This progress emphasizes the need for electropolishing as an important process to finish a part in a clean way in modern industry.
The Role Of Metal Ions In The Electropolishing Process
Metal ions are extremely important to the process of electropolishing since they actively aid in the removal of material from a metal surface. In my case of electropolishing, I use the electrolytic bath to extract metal atoms from the surface, which subsequently yield metal ions in the solution. This auxiliary dissolution is important in order to make and refine the surface, for the preservation of the process by the ions is also needed for the achievement of uniformity throughout the entire surface.
How Electropolishing Can Remove Surface Imperfections
Electropolishing is an advanced technique that removes imperfections on the metal surface by finely refining a surface exceeding a level near a certain threshold. During the electropolishing process, the higher peaks dissolve quicker than the lower areas because the current is directly proportional to the height of the area. As a result, the surface becomes smoother and more level. According to research, the roughness of surfaces treated with electropolishing may improve by 50% from the starting value, depending on how rough the material is from the beginning. End result, thorough electropolishing removes contaminants like burrs, embedded particles and residues on the surface which greatly augments the burr-free corrosion resistance of the material as well as enhances the surface cleanliness of the material.
This technique is critical for the manufacturing of medical devices, aerospace components, and food processing parts, where ultra-clean surface treatment and precision work combined with careful attention to detail are obligatory. For example, the average surface roughness of stainless steel components can be reduced to as low as 0.1Ra due to electropolishing. This reduced micro-roughness enhances the aesthetic appeal, but also improves performance because smoother surfaces have fewer bacteria and other contaminants attached to them.
What Are The Benefits Of Electropolishing Compared To Electroplating?
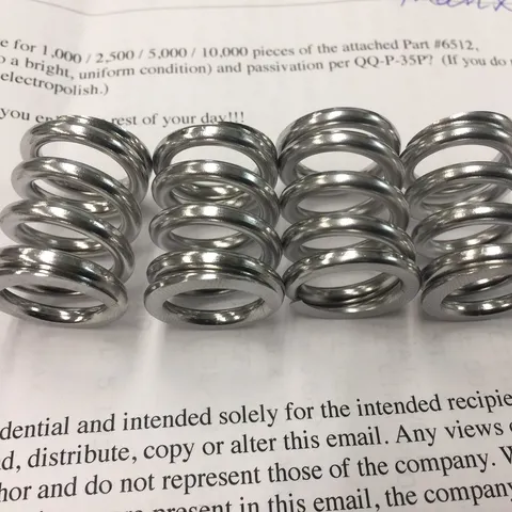
Electropolishing has several advantages in comparison to electroplating.
- Improved Surface Finish: like electroplating does not rot irregular surface features, it adds a coat that surfaces are freed from, bronze adds to gray.
- Corrosion Resistance: Two defects reduce the material’s innate ability to resist corrosion, roughness, and passivation.
- Material Integrity: Electropolishing does not add any foreign layer which helps keep the base material intact in integrity. This adds avoids issues attributed to peeling or flaking caused by electroplated coatings.
- Cleanliness and Hygiene: With coatings, the roughened surface becomes trapping and less prone, but this provides an opportunity for them to become ideal in the recollection. This makes it fit for food and medical, and other industries that deal with advanced pharmaceuticals.
For unmatched durability, precision, and cleanliness, electropolishing stands out as the preferred choice due to these benefits.
How Electropolishing Improves Corrosion Resistance
In the chemical/medical device industry, where surfaces undergo treatments that last for three to four hours, solvents and corrosive materials are used. In situations like these, electropolished surfaces maintain their integrity, whereas mechanically polished surfaces begin to corrode. In fact, under extreme conditions such as the application of saline spray, acid, or vigorous rubbing, surfaces treated using mechanical polishing corrode rapidly, while those completed using electropolishing remain intact. Research proposes, and industry data has confirmed that medically sophisticated devices, such as coronary stents, construction-grade electropolished stainless steel cardiovascular stents, have an unparalleled amount of both passive and active surface corrosion resistance.
Through the electropolishing procedures, all sharp micro remnants adhering to the polisher are removed, cleaning the surface of the object. The application of such practices prevents tubework and machine tools from premature wear due to their obsolescence. Electropolishing eliminates sharp micro protrusions, enhancing the corrosion resistance of the surface by preventing pit formation, microburrs, and other imperfections and contaminants from growing.
Corrosion is exceptionally well fought against through polishing. During any sort of mechanized polishing, burrs form on the surface. Each of these functions as a can for primitive pits of corrosion to form. Gaps, marks, and blemishes can all serve as origins for the collapse of structures.
When it comes to ship hulls, they utilize steel incorporated with an additional layer of protection against Oscar the hotel’s scratches is shielded using copper. This addition serves, but can also put the primary portion at risk, which causes significant blockage.
Why Electropolishing Provides a Superior Surface Finish For Stainless Steel
Electropolishing works best when it comes to the surface finish of stainless steel because it provides exceptional smoothness and shine. Research confirms that electropolishing can reduce surface roughness to below 0.2µm Ra, which is smoother than any surface achieved by mechanical polishing. This is important in the food processing and pharmaceutical sectors that require high hygiene standards, as the electropolished surface reduces the spaces where contaminants and bacteria can get trapped.
Electropolishing also effectively increases the corrosion resistance of the material by removing surface impurities and enhancing the microscopic cracks on the surface. Stainless steel that has undergone electropolishing is able to endure up to 33% longer in corrosive conditions compared to the untreated or even the mechanically polished surfaces. By dissolving the layers of metal closest to the surface, electropolishing increases the chromium-to-iron ratio on the surface. This also increases the primary protective layer of stainless steel – the chromium oxide layer. These reasons are why stainless steel benefits so much from electropolishing; it provides a functional surface finish.
When To Use Electropolishing Instead Of Electroplating
I choose electropolishing over electroplating when I want to improve surface finish by removing imperfections, enhancing corrosion resistance, and lowering the risk of contamination. Unlike electroplating, which adds a coating, electropolishing is better suited for cleaning and passivating surfaces in medical, food processing, semiconductor, and other industries where a smooth, sterile surface is needed.
What Applications And Industries Commonly Use Electropolishing?
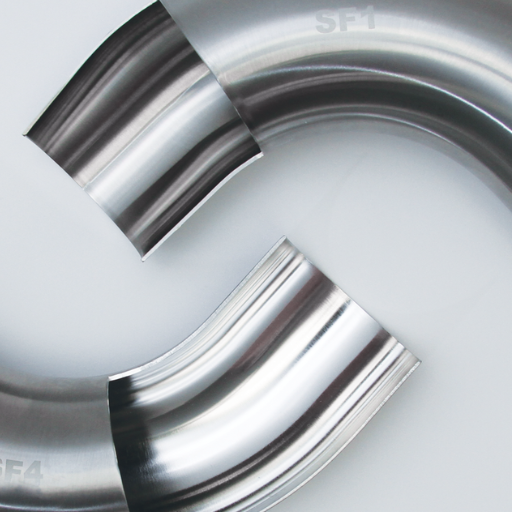
Electropolishing can be useful for industries that require surfaces to be smooth, clean, and free of corrosion. The key applications are:
- Medical Industry: For instruments, implants, and surgical medical devices, maintaining perfection is critical. Hence, surface hygiene is of utmost importance.
- Food and Beverage Industry: For processing equipment, sterility and freedom from contamination are critical.
- Semiconductor Industry: For components that require ultra-smooth surfaces devoid of particles being trapped, polished components are essential.
- Aerospace Industry: For critical parts, polished components help enhance their durability, performance, and service life.
- Pharmaceutical Industry:F or medical-grade devices, equipment must have sterile surfaces and a completely passivated region.
Why Electropolishing Is Commonly Used For Stainless Steel Alloys
Surface enhancement and corrosion resistance are of primary importance when considering the purpose of the stainless steel alloy, which makes electropolishing the ideal choice due to the multi-faceted advantages it offers. The surface of the material is polished to a mirror finish and the surface layer is smoothed out by removing micro peaks and valleys. Studies show that roughness average (Ra) is reduced by as much as 50% through electropolishing, providing better hygiene and cleanliness standards.
The self-healing oxide layer that provides stainless steel alloys with corrosion resistance is one of the reasons why alloys undergo electropolishing. Electropolishing enhances the difference by blasting away trapped particles underneath that are not passive and cover chromic surfaces, ensuring uniform exposure and passive coverage on chrome. Such precision and care guarantee that the alloy will endure harsh and extreme environments without damage. Sterility and hygiene are of utmost importance to the medical and food processing industries, making them heavily dependent on using electropolished stainless steel along with aerospace components due to their reliability.
Also, studies state that the use of electropolishing extends the lifespan of stainless steel parts due to its reduction of wear and stress areas. Components such as surgical instruments and cleanroom piping are greatly aided by this finish because of its resistance to bacterial growth and biofilm formation, which highlights its usefulness and versatility even more. Electropolishing remains critical for attaining optimal results in current manufacturing due to the unparalleled characteristics that are achieved through this process.
Industries That Benefit From Electropolishing Metal Surfaces
With its exceptional capabilities in improving cleanliness, corrosion resistance, and achieving a mirror finish, electropolishing is highly valuable across different industries. Here are some of the primary sectors that utilize electropolishing:
- Pharmaceutical and Medical Device Industry
Electropolishing is one of the critical processes in maintaining sterility and cleanliness in the pharmaceutical and medical device industries. Surgical implants, tools, and cleanroom instruments undergo electropolishing to help reduce microbial contamination. According to one study, surfaces that underwent electropolishing showed up to 50 percent reduction in bacterial adhesion compared to non-polished surfaces , which helps significantly improve patient safety.
- Aerospace Industry
Components within the aerospace industry such as hydraulic systems and turbine blades require an electropolishing treatment due to the necessity for extreme resistance to abrasion, high durability, and low maintenance. Polishing the surface of these parts increases fatigue strength and lowers the chances of surface defects which leads to stress corrosion. These components need to withstand very high temperatures and pressure for long periods of time.
- Food and Beverage Industry
Cleanliness is an indispensable factor in food and beverage processing equipment. The electropolished stainless steel surfaces of the equipment withstand strict regulatory requirements, prevent contamination, and clean with optimum efficiency. Studies demonstrate that surfaces that have been electropolished are easier to clean by 30% to 40% as compared to untreated surfaces.
- Semiconductor and Electronics Industry
Very accurate and very clean is the minimum requirement for the processes done in the manufacturing of semiconductors. The electropolished surfaces offer no particulate contamination and have ultra-fine polished surfaces, which are critical for the manufacture of micro components used in chips and circuits.
- Automotive Industry
Electropolishing is done on fuel injectors and exhaust systems because they are critical to performance, fuel efficiency, and emissions reduction. Improves heat resistance and smoother surfaces contribute to optimum functionality.
The performance of critical components and their hygienic integrity, as well as extending their lifespan, are improved by electropolishing in a wide variety of industries.
When Electropolishing Is Essential For Medical And Food Equipment
Electropolishing is extremely important in the food and medical outputs since all aspects of cleanliness, robustness, and accuracy must be upheld. For surgical instruments, implants, and medical devices, electropolishing enhances their ultra-smooth, defect- free surfaces. This improves the biocompatibility of implants thus preventing the buildup of bacteria and infections. According to some studies, the incorporation of electropolishing into implant manufacturing in medicine makes them more easily accepted by the body while having improved wear resistance, ensuring the safety of patients and the longevity of the devices.
In the food processing industry, electropolishing is crucial for maintaining hygienic surfaces. Tanks, piping, and mixers as some examples of equipment that are made with electropolished stainless steel surfaces. Electropolished finishes reduce the possibility of biofilm formation as well as contamination. Research has proved that electropolished stainless steel surfaces are over 30% more easily cleanable compared to untreated counterparts, bringing better sanitation and lower maintenance costs. Such attributes aid in the compliance with FDA and USDA regulatory requirements while ensuring food safety and operational effectiveness.
How Does Electropolishing Relate To Stainless Steel Passivation?
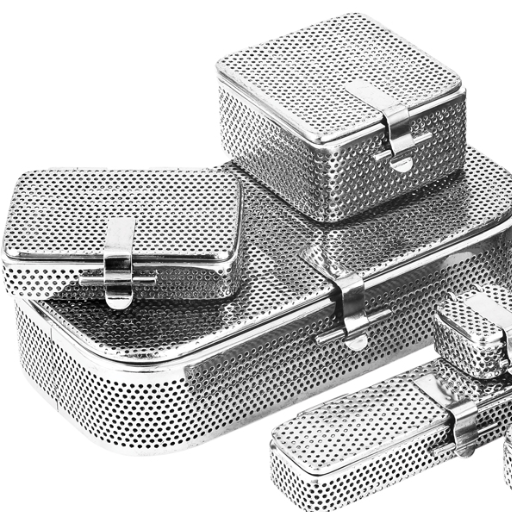
Electropolishing and passivation of stainless steel are interdependent processes that improve surface cleanliness and a material’s corrosion resistance. Through electropolishing, a scrubbed cell removes a thin layer from the object’s surface to achieve a polished, gleaming look, as well as reducing irregularities in the surface. In addition, passivation is an electrochemical process intended to increase the corrosion resistance of a metal by enhancing the oxide layer. Unlike passivation, which relies mainly on the formation of a protective oxide layer, passivation can be further enhanced with electro-polishing, and passivation works best together; they bond precisely. Passivation is enhanced when a surface is prepared by removing a chromium oxide layer with embedded contaminants.
Understanding The Relationship Between Electropolishing And Passivation Of Stainless Steel
In the medical, food processing, and aerospace sectors, components made from stainless steel undergo careful electropolishing procedures to ensure optimal performance while meeting cleanliness and corrosion resistance requirements. Electropolishing is further enhanced by the addition of surface passivation. This is a treatment process where an oxide layer is created to prevent further corrosion. Rather than using an abrasive method, electropolishing works by an electrochemical process that removes some of the material from the surface. This is then followed by passivation, which improves corrosion resistance through the application of citric acid.
All these production steps improve the surface flatness, polish, and cleanness, augmenting corrosion resistance substantially. Actually, conservatively speaking, industry data suggests untreated stainless steel surfaces could have corrosion resistance improved electropolished stainless steel surfaces around of up to tenfold. The more it is treated, the more the bacterial growth is inhibited.
From a chemical point of view, these actions are considered complementary because electropolishing improves surface finish and enhances corrosion resistance, whereas passivation aids in material strengthening and also protects the stainless steel from external environmental factors such as moisture and exposure to acids. In fact, research suggests untreated passivated stainless steel can withstand more chemically and-engineered hostile environments over time. Using them in tandem, this ensures cost-effective maintenance and support for stringent engineering regulations alongside regulations put in place for hygiene.
How Electropolishing Significantly Enhances The Passivation Process
Topside polishing helps achieve a much smoother finish on the surface of a component, which in turn makes it easier for contaminants to form on top of the passive layer. This, in turn, permits the component to have a far more enhanced corrosion resistance, and as such, studies have shown that electropolished surfaces are corrosion resistant compared to mechanically polished ones. Moreover, the removal of surface imperfections such as corrosion pits and rough edges takes away any already added threat of corrosion, which helps in further enhancing the ability of the surface to withstand harsh conditions. Electropolishing surface imperfections not only aids in augmenting the lifespan of a component but also assists with improving hygiene on contamination risk components as well. As a result, it can be said that rough edges and pits encourage the creation of irregular surfaces and contours in metals, which can act as footholds and dramatically increase the ability of a polished surface to resist harsh conditions.
Chromium-iron ratios are further increased, and the passive oxide layer of a rough surface receives a major enhancement after the process. As previously mentioned, unrefined surfaces equipped with bumps and grooves can significantly increase the ability of a polished surface to withstand harsh conditions. This, coupled with the enhancements provided due to electropolishing, makes it possible for surfaces to retain integrity while aiding in expanding their lifespan, protection from contamination, and corrosion resistance, making them viable in economically sensitive fields such as food and health treatment sectors. The combination of polish and passivation also eases the process of cleaning used within the facility, making the procedures easier for hygiene reasons while avoiding biofilm formation, which brings the component in line with international safety and hygiene policies.
Benefits Of Combined Electropolishing And Passivation Treatments
The combination of electropolishing and passivation processes enhances corrosion resistance of stainless steel and other alloys. Electropolishing removes sharp edges and surface micro-chasms while passivation forms a protective oxide layer that defends the material from harmful elements such as chloride and acid. Research indicates these treatments can extend the service life of stainless steel parts in corrosive conditions by up to twofold, diminishing maintenance expenses and intervals.
Improved Surface Smoothness
Ultra ultra-smooth surface requires both of these treatments, especially for industries oriented towards cleanliness and sterility. With sophisticated techniques, electropolishing accomplishes surface finishes of 0.1 μm Ra and improves smooth surface finishes. This lower roughness would reduce the hiding places for contaminants. Smooth iron-containing surfaces leave a free iron residue as surface finishing contaminates non-manufacturing, unattended processes. These smooth surfaces help mitigate contamination, enable easier, more effective cleaning eradicate n.
Reduced Particulate Contamination
The combination of these treatments aims for the reduction of nonsmooth contours and remaining cleanseable impurities, which results in reduced particle contaminants. Such a lack of surface smoothness is essential for devices such as semiconductor or medical devices, as the presence of even nanometer-sized dirt can compromise the product. Users of this integration report as much as 50% fewer incidents of particle contamination on the treated parts after using this integration.
Compliance With Industry Standards
Applying both electropolishing and passivation of the surfaces meets the rigorous requirements of ASME BPE, ASTM A967, and ISO standards of cleanliness. In many industries like pharmaceuticals and biotechnology, these regulatory bodies require specific surface treatment to provide exceptional cleanliness and corrosion resistance. Heating Surface Preparation assists manufacturers to effectively meet these parameters, ensuring consumer safety and product quality.
Cost Efficiency Over Time
While it may seem that the initial investment for combined electropolishing and passivation of the surfaces is more than that of single treatments, the returns from Etched Surface Treatment through controlled surface finish ail in greater benefits over time, spanning many years. Enhanced component lifetime, reduced upkeep, and lower effort required to clean all contribute to significant savings in the long run. Facilities employing this dual treatment have been proven to offset over 30% of their routine upkeep costs, validating its affordability.
Can Electropolishing Be Applied To Different Metal Types?
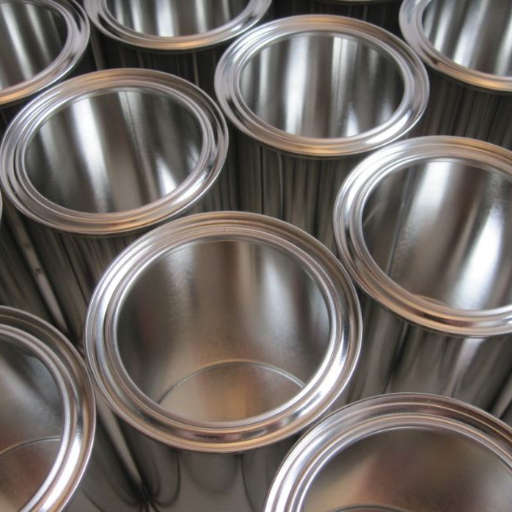
Indeed, electropolishing is applicable to several types of metals. It is primarily used on stainless steel; however, it can also be applied to aluminum, copper, nickel, titanium, and some alloys. Applicability depends on the composition of the metal as well as the type of finish, which makes it a useful process for improving surface finish and resistance to corrosion across various uses.
Which Metals Beyond Stainless Steel Can Be Electropolished
Electropolishing is a common process not only for stainless steel but also for numerous other metals, for which it shows stunning results. For instance, aluminum undergoes significant improvement when electropolished because of its enhanced corrosion resistance and the bright, reflective surface it attains. Copper and its alloys can also be electropolished to enhance their surface finishes and improve the electrical conductivity of these metals.
Nickel and nickel-based alloys, which find application in low-temperature aerospace and chemical environments, acquire enhanced smoothness and surface treatment with lower chemical wear when electropolished. In the same fashion, titanium used in industries such as medical devices improves its biocompatibility and surface contamination level through this processing.
Research suggests that electropolishing has the potential to increase surface roughness (Ra) up to 50%, an important factor when providing surfaces of different metals with a consistent smooth finish. Also, being able to enhance the cleanliness of a surface and remove inclusions makes it indispensable in the food processing, pharmaceutical, and electronics industries, where exacting tolerances and cleanliness are essential. The diverse capability of electropolishing illustrates how this process adapts to different properties of metals ensuring reliable performance and durability in an extensive range of applications.
How Carbon Steel And Other Alloys Respond To Electropolishing
The degree to which alloy differs from one another affects the value proposition offered and, in turn, the benefits obtained from electropolishing. Among alloys, carbon steel and other alloys portray distinct features. In carbon steel, electropolishing is most often done to lift surface residues, further protect against corrosion, and obtain a polished surface. One must bear in mind, though, that carbon steel is devoid of chromium, which is fundamental in self-passivation. This means that additional coatings of protection are needed to prevent oxidation and rust after electropolishing is done.
In contrast, stainless steel as an alloy benefits the most from electropolishing due to the presence of chromium, which permits the development of a passive oxide layer. Stainless steel, therefore, has significantly improved corrosion resistance, which makes it useful in hostile environments such as marine, medical, and food processing industries. Lastly, titanium alloys are widely utilized in the aerospace and medical industries due to the high demand for precision. Such alloys undergo electropolishing to obtain controlled smoothing of surface defects, which optimizes them for the aforementioned applications.
Research indicates that electropolishing is able to decrease surface roughness of some metals by up to 50%, or more, depending on the type of alloy used and the initial surface condition of the metal. Such changes in the roughness of a material improve its visual appeal while also improving its cleanliness and overall performance. With aluminum alloys, the use of electropolishing can enhance reflectivity and smoothness, but due to the softness of the material, more care must be taken to monitor the process. These differences are indicative of the need for more customized methods of electropolishing to suit the requirements posed by each alloy’s specific properties. Understanding these responses enables industries to make optimum use of the benefits offered by this important treatment process.
Comparing Results On Different Metal Surfaces
The outcome of electropolishing often depends on material properties and how the user wants the material treated. For example, stainless steel smooths out and resists corrosion due to its high chromium content, which improves passivation during the process. Research indicates that Type 316 stainless steel undergoes significant surface roughness reductions of over 50 percent after electropolishing, making this type of stainless steel ideal for clean and sterile environments like the pharmaceutical and food industries.
On the other hand, copper alloys can be polished to have a brighter finish but risks surface pitting or excess material being removed due to copper’s high reactivity. The use of aluminum alloys presents a different problem. While the process can enhance the aluminum’s reflectivity and decrease micro-roughness, further polishing can result in weakening the soft structure of the aluminum.
Electropolishing aids in improving titanium’s biocompatibility and lowering its bacterial adhesion, key in biomedical devices. This is especially true for surgical implants where precision and performance requirements are critical. Electropolishing titanium surfaces can result in average surface roughness values of less than 0.15 micrometers, making it favorable for medical applications.
These differences in results of electropolishing each metal handpicked showcases how all metals require different approaches to achieve the best outcome. Other industries which to meet deeper performance and aesthetic needs receive surfaces through advance technologies and equipment which further optimize the technique.
Reference Sources
- Study on Electropolishing of Carbon Steel with Polymer Additives1:
- Key Findings: This research explored the use of natural polymers (e.g., starch, gelatin, chitosan) as corrosion inhibitors during the electropolishing of carbon steel. The study demonstrated that these polymers significantly reduced corrosion rates and improved surface morphology. The effectiveness was attributed to the adsorption of polymers on the steel surface, forming a protective layer.
- Methodology: The study used polarization curves, SEM imaging, and atomic absorption spectroscopy to evaluate the impact of polymer additives on electropolishing efficiency and corrosion inhibition.
- Multi-Factorial Model for Electropolishing Stainless Steel3:
- Key Findings: This study developed a mathematical model to optimize electropolishing parameters (e.g., time, temperature, current density) while minimizing environmental impact. It highlighted the importance of controlling bath contamination to achieve the desired surface quality and reduce metal ion pollution in wastewater.
- Methodology: Experiments were conducted on AISI 304 stainless steel under varying conditions. Surface roughness, gloss, and corrosion resistance were analyzed using XPS, ICP-OES, and corrosion tests. The model provided insights into achieving optimal results with minimal environmental impact.
Frequently Asked Questions (FAQs)
Q: What is an introduction to electropolishing, and how does it differ from electroplating?
A: Electropolishing is an electrolytic process that improves metal surfaces by removing material rather than adding it. Unlike electroplating, which adds a new layer of metal onto a substrate, electropolishing is often described as a “reverse plating process” that selectively dissolves microscopic peaks from the metal surface, leaving it smooth and bright. This finishing process enhances both functional and aesthetic properties of metals, particularly stainless steel. While both processes use electrolytic baths, their fundamental purposes differ – electropolishing removes material to reveal a pristine surface, while electroplating as well adds protective or decorative coatings.
Q: How does the process of electropolishing work?
A: Electropolishing involves immersing the metal workpiece in an electrolyte bath and connecting it as the anode in an electrical circuit, with a cathode also present in the solution. When direct current is applied, metal ions from the surface are preferentially dissolved from microscopic peaks, effectively leveling the surface. The process creates a passive oxide layer that enhances corrosion resistance. The electrolyte solution typically contains phosphoric and sulfuric acids, and the entire process is carefully controlled for temperature, current density, and duration to achieve optimal results. This electrolytic polishing and electropolishing technique works by essentially reversing the principles of electroplating.
Q: What are the main applications of electropolishing in various industries?
A: Electropolishing is used across numerous industries for its unique benefits. The medical industry relies on electropolishing for surgical instruments and implants due to its ability to create ultra-clean, bacteria-resistant surfaces. The food and beverage industry uses electropolished equipment to prevent contamination and facilitate cleaning. Aerospace applications include components where surface perfection impacts performance. Semiconductor manufacturing requires electropolishing for ultra-pure components. Architectural elements benefit from the enhanced appearance of stainless steel after electropolishing. Pharmaceutical processing equipment, automotive components, and consumer products are other areas where electropolishing effectively improves functionality and aesthetics.
Q: How does electropolishing prevent corrosion on metal surfaces?
A: Electropolishing prevents corrosion through several mechanisms. First, it removes free iron and other inclusions from the surface of stainless steel that might otherwise serve as initiation sites for corrosion. Second, the process enhances the chromium-to-iron ratio at the surface, strengthening the passive oxide layer that gives stainless its corrosion resistance. Third, by eliminating microscopic crevices where corrosive agents might collect, electropolishing dramatically reduces pitting corrosion risk. The ultrasmooth surface created prevents biofilm adhesion and product buildup, further reducing corrosion risks. This makes electropolishing particularly valuable in harsh environments like marine, chemical processing, and high-temperature applications.
Q: How does the finishing process of electropolishing improve the surface of stainless steel parts?
A: The finishing process of electropolishing transforms the surface of stainless steel parts by removing a thin layer (typically 0.0005″ to 0.001″) from the entire surface, effectively eliminating imperfections. This process smooths rough edges, reduces surface roughness to as low as 2-4 microinches, and removes embedded contaminants. The resulting surface is not only visually appealing with enhanced brightness and reflectivity but also functionally superior. The process eliminates microburrs that cause friction, creates a more hygienic surface resistant to bacterial attachment, and improves fluid flow characteristics. Electropolished stainless steel parts also exhibit enhanced fatigue resistance and improved weldability.
Q: What factors should be considered when deciding to electropolish stainless steel components?
A: When deciding to electropolish stainless steel components, several factors must be considered. First, the alloy composition significantly affects results – austenitic stainless steels like 304 and 316 respond exceptionally well, while other grades may yield varying results. Second, consider the initial surface condition, as electropolishing magnifies rather than conceals deep scratches or defects. Third, evaluate dimensional tolerances, as material removal must be accounted for in precise applications. Fourth, assess the part geometry, as complex shapes with internal passages may require special equipment. Finally, consider regulatory requirements, cost factors compared to mechanical finishing, and whether the specific benefits of electropolishing align with the application requirements.
Q: What are the limitations and challenges of the electropolishing process?
A: Despite its benefits, the electropolishing process has several limitations. It cannot remove large surface defects or deep scratches and may actually accentuate them. The process involves hazardous chemicals requiring strict safety protocols and environmental controls. Not all metals respond equally well – while stainless steel electropolishes excellently, aluminum and some other metals present challenges. Cost can be higher than mechanical polishing alternatives. Process control is critical, as variations in current density can lead to uneven results. Size limitations exist based on available equipment. Some dimensional change occurs that must be factored into tolerances. And finally, the process may reveal subsurface defects not previously visible, potentially necessitating part rejection.
Q: How can one determine if electropolishing is the right choice compared to electroplating for a specific application?
A: To determine whether electropolishing is the right choice versus electroplating, analyze your specific requirements. Choose electropolishing when you need to: improve the inherent properties of the base metal; enhance corrosion resistance without adding coatings; achieve biocompatibility for medical applications; create an ultraclean surface free of embedded contaminants; or maintain precise dimensions with minimal material removal. Alternatively, select electroplating when you need to: add properties the base metal lacks (like conductivity or hardness); achieve decorative finishes unavailable in the base metal; repair damaged surfaces; protect non-corrosion-resistant base metals; or add thickness to undersized components. To learn more about the electropolishing process for your specific application, consulting with specialists at able electropolishing service providers is recommended.